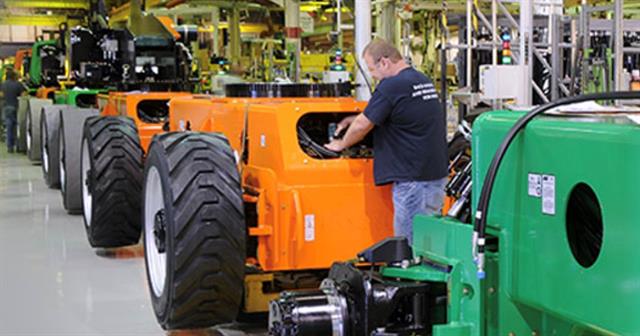 JLG has suspended production in many of its facilities |
With materials handling classed as an essential service in many jurisdictions in the United States, it is almost business as usual for the forklift sector.
Forkliftaction News contacted many manufacturers, distributors and dealers, and hasn't heard of any complete halts to production or supply activity.
In a statement,
The Raymond Corporation says it is "making the necessary localised adjustments to our work and our operations" in the face of the COVID-19 crisis.
"We, along with our network of sales and services centres across North America and around the world, continue to strive to serve our customers/ needs during these unprecedented times with forklifts, flexible solutions such as rentals, virtual and in-person service, maintenance, parts distribution, optimisation efforts and so much more, supported by our entire Raymond team's remarkable efforts," the statement continues.
Raymond continues to prioritise employees' well-being with the utmost care and concern, "while respecting Raymond's designation as an essential business in keeping the supply chain running so that food, pharmaceuticals, medical devices and other essential goods keep moving".
Since Monday, Raymond's Greene, New York plant, has had limited operations "to produce a limited number of critical components for essential businesses". The remainder of the Greene plant will remain closed, with plans to resume production on 6 April.
Toyota Material Handling North America notes on its website that "Toyota and its dealer network are at your service for immediate repairs and critical planned maintenance to keep you up and running during the COVID-19 outbreak".
Yale notes in a statement that it is "taking extra precautions to protect you, our employees and the communities we serve".
"Our Global Task Force continues to evaluate the impact of COVID-19, which involves monitoring the well-being of our associates around the world, working with our supply chain to identify any potential delays in production and keeping an open and regular line of communication with our dealers. These measures ensure we act on the latest information and prepare contingency plans to navigate a very dynamic situation.
"Measures adopted so far include suspending international air travel, limiting domestic air travel, asking employees to hold meetings virtually, limiting visitors and encouraging social distancing wherever possible.
"While we cannot forecast the full impact of the situation, we are proud to support our dealer partners and customers as they work to keep this world moving. Without them, many companies would not be able to move medicine, food, or the staples that are needed during this critical time," the statement adds.
JLG has suspended production in many of its facilities, including the US and Mexico, which will remain offline until 13 April.
Like other manufacturers, the company has taken many preventive measures to limit the potential spread of the virus and mitigate the impact to its business and customers. Measures include increased cleaning frequency of high-touch areas in their facilities, cancellation or rescheduling of company events, limitations placed on global and domestic business travel and staggered work shifts and work zones to limit the spread of germs.
Richard Wright, senior manager, global communications and community engagement, says JLG rose to meet local healthcare challenges in the communities around its McConnellsburg, Pennsylvania headquarters.
"When the operations team learned about the personal protective equipment shortages across the country, they knew immediately that they wanted to do something to support healthcare professionals. We use the N95 masks in our operations and made the decision quickly to donate more than 3,000 masks to local hospitals in Bedford, Fulton and Franklin County. We are proud of our team for taking action to help where they can, and we hope that our example will encourage other businesses to evaluate ways they can support our healthcare professionals during this unprecedented time," he explains.
The JLG parts distribution, service and call centres remain open.
Parts and accessories flowingAttachments maker
Cascade is continuing production globally "except in some regions that have limited ability to produce and ship products in order to comply with local government mandates," Davide Roncari, president and CEO, tells
Forkliftaction News.
"During this period of limited manufacturing availability at these facilities, we are maintaining customer relations with our remote working ability. In addition, as a company with operations around the world, Cascade is able to leverage our global footprint to meet future orders and minimise any short-term impact to our customers," he explains.
Roncari stresses that the health and safety of employees continues to be of the utmost importance. "We have implemented strict procedures at our global facilities in order to comply with directives set forth by the World Health Organisation and local health authorities. For example, Cascade has indefinitely suspended both domestic and international company travel. In addition, a majority of our office employees have been directed to work remotely and our production teams have applied countermeasures in the plants, such as temperature checks, proactively cleaning and sanitising high touch areas, maintaining proper social distancing, reallocation of production shifts and more. As circumstances surrounding this virus change constantly, our HR and executive teams are committed to regularly providing the most up-to-date information to keep all employees, customers and suppliers informed."
Battery systems maker
Navitas has also taken a number of steps to ensure the
safety of employees, customers, suppliers and the broader community.
"We are encouraging our employees that can work from home to stay home in order to help prevent exposure to our employees that are on site preparing â?¦ orders," says Samer ElShafei, vice president â?? sales.
"We are doing everything possible to provide you with the uninterrupted, dependable service that you have come to expect from Navitas. Our onsite housekeeping has been increased and we are actively providing a clean and sanitised environment to our employees to the utmost extent," he explains.
Like others, Navitas has asked employees to cease all travel unless critical to the operation, and is limiting site visits. "We have also asked employees to limit contact which means handshaking is off limits for the next 30 days."
In the face of the chaos created by COVID-19,
TVH Parts is working hard to do its part in bringing stability to a rapidly changing situation. As a crucial member of the supply chain to critical industries such as materials handling and logistics, TVH is in an important position to help keep daily necessities such as food, medication and medical supplies travelling to where theyâ??re needed the most.
"Every day that we continue to ship parts is a day that our customer can and will keep a machine in operation somewhere across the globe," says Dirk von Holt, president of TVH Americas.
The company is making every effort to follow governmental regulations regarding social distancing, essential travel and good hygiene practices, as well as continually monitoring the updates and making the necessary adjustments to ensure customers and employees are safe and healthy.
"TVH is working tirelessly to minimise the impact of a lack of replacement parts for these critical industries and ensure that our customers can continue to have access to the parts they need, when they need them," von Holt adds.
Business as usual for dealersDealerships appear to be trading around the US.
The large
Wolter Group, which has been classed an Essential Business for COVID-19 Response, says it is committed to supporting customers and maintaining its level of service.
"We will still come to you and adapt to your company's policy on visitors. If your protocol restricts our technicians from working inside your facility, we can arrange to perform service on equipment in an outdoor space," says a company statement. "A 'no customer signature required' policy has been implemented to limit contact."
Where clients' protocols prohibit technicians coming to their facilities, Wolter is offering discounted cartage and freight rates for shipping equipment to its facilities for service.
Noting increased demand for materials handling equipment at the moment, Wolter says its rental departments are stocked and ready to go.
Smaller dealers like Pearland, Texas-based
Frontier Forklifts & Equipment are also in full operation. "We are proud to be deemed an essential part of keeping our customers up and running during this time of confusion and uncertainty. We are here and ready to serve you with the quality customer service you have come to know and expect from us," the dealership says in a statement.
Frontier is taking significant steps to reduce any health risks, including daily monitoring of all inside and field staff for signs and symptoms associated with COVID-19. "All inside activity involves social distancing and special provisions for work spaces and pick-up/delivery areas. All employees have been informed of the importance of consistent hand hygiene, social distancing, work space sanitation, etc. We have made changes to procedures involving customer interactions in order to limit customer contact as much as possible."
Associations take actionThe
Industrial Truck Association (ITA) continues to lobby US leaders for recognition of the vital role played by materials handling.
ITA has written to the National Governors Association, urging members "to ensure that the state and local policies safeguard the ability of essential businesses to continue operations".
"As our nation continues to confront the coronavirus's challenges, we want to underscore the importance of powered industrial trucks, often called forklifts, in the nation's supply chain that enables restocking of every grocery story, pharmacy, convenience store, big box store and hardware store in the country. In addition, powered industrial trucks play an indispensable role in virtually every production facility, warehouse and distribution facility used to get products to the market for sale," ITA president Brian Feehan notes.
"Powered industrial trucks, both new and old, are essential to ensure that the public can get food, hospitals their medical supplies, and other necessities of life continue to move through the supply chain. The continued production, sale, rental, replacement parts distribution and servicing of powered industrial trucks is essential to enabling the nation's economy to continue to meet the demand for products and services that the public relies on in their day-to-day life."
Meanwhile, distributor representative
MHEDA has assembled a range of resources to help material handling companies and their employees.
The MHEDA COVID-19 webpage includes assistance in determining "essential" business classification, a summary of state "stay at home" orders, guidance on managing the workplace during this crisis and details of webinars on a variety of topics to help manage their business during this crisis.
"During these difficult times, it is more important than ever before to connect and rely on one another to conquer our personal and professional challenges," says MHEDA CEO Liz Richards.
The resources can be found
here.