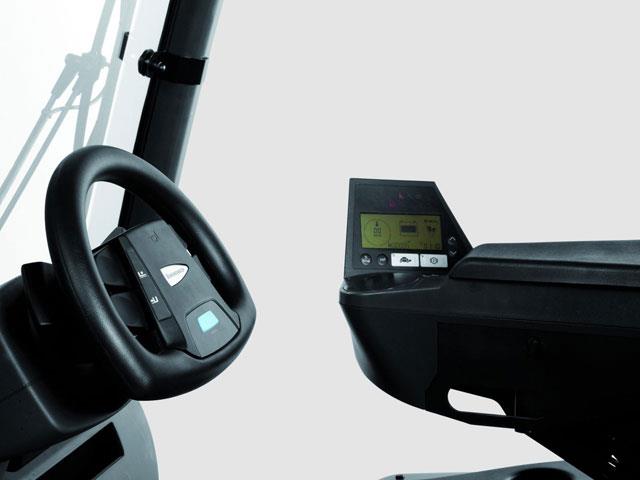 The Jungheinrich JetPilot steering wheel now available as an option for the EFG 425-430 forklift range. |
by Christine LiewThe industry's leading forklift manufacturers and our Safety First columnists share their perspectives on the highlights of the year that has just ended - and their implications for the year ahead.New technologyGerman forklift giant
Linde, bought by Kohlberg Kravis Roberts & Co and Goldman Sachs Capital Partners in 2006, didn't unveil new technology last year but it did complete its EUR10million (USD13.4 million) development centre in Aschaffenburg and launch a new marketing label for its products.
Linde PureMotion was introduced at the Bauma trade show in Munich in April. It was all about the company's affirmation of its corporate responsibility to its forklift users and the environment.
Linde Material Handling's managing director at the time, George Silbermann, said the company had a responsibility to protect people and the environment. Before introducing the program, Linde analysed all its departments and examined its products and services. The protection of "man and environment" were not mutually exclusive, Silbermann said, but belonged together. The program was presented to the European trade press in Frankfurt am Main in November.
Last year, the EU directive 2002/44/EC became a part of German law and Linde's German dealers and European sales organisation offered a service package to help companies fulfil their requirements of protecting workers from risks of vibration exposure.
Linde's partners counsel clients on vibration protection, health monitoring and the new directive, while the company also provides clients with vibration measurement equipment - a seat measurement cushion and software and the Linde PureMotion calculation tool, which allows the comparison of several series of measurements.
Still GmbH, a sibling of Linde in the KION Group that also controls the OM brand, says it is improving warehouse automation and is proud of the work it did for General Electric (GE) Plastics last year.
Using the newly designed MMSi, an IT solution that allows different configurations for an automatic warehouse operation, Still worked with logistics service provider DSV to automate GE Plastics' central European warehouse. Driverless Still MX-X VNA trucks were used at the plant in Bergen op Zoom on the Oosterschelde in the Netherlands. The result of the project was greater capacity and flexibility at the site and the resolution of another pressing problem.
Still says automating the Bergen op Zoom warehouse helped combat skills shortage in the Netherlands. GE became less dependent on the labour market and less affected by worker absence after the automation removed 17 jobs.
The project was challenging because Still worked to convert the manually operated warehouse to one with 18 automated aisles and six manual aisles while warehouse operations continued as per usual. Eventually, the new system enabled over 3,000 pallets to be moved a day.
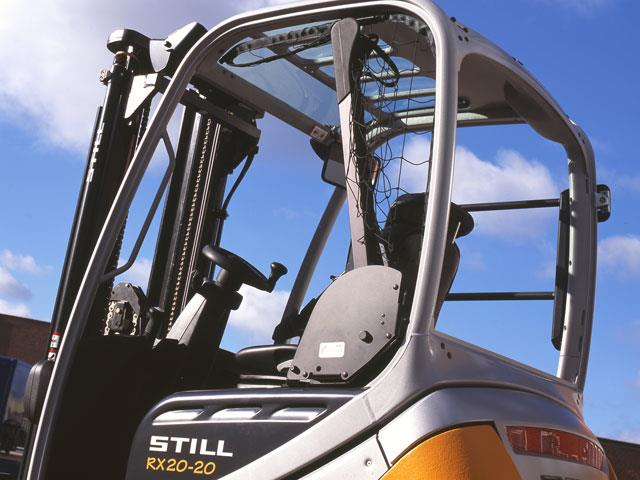 Still has developed "netProtect", a restraint system used in place of a safety belt. |
Still also developed a new restraint system - "netProtect" - used in place of a safety belt. The sensor-controlled "netProtect" consists of a fixed bar on the right hand side of the cabin and a bar moved by an electric motor on the left hand side. During travel, the bar is lowered and closes the access opening with a protective net. The system was tested at a Hamburg port and is available for Still's RX 20 and RX 60 forklifts.
Forkliftaction.com News Safety First columnist and forklift driving trainer David Hoover says many operators do not wear their seatbelts and using a restraint system could save at least 25 lives in the US and many more worldwide.
Hamburg-based
Jungheinrich made its JetPilot steering wheel available as an option for all its electric counterbalanced forklifts in the EFG 425-430 range in September 2007. JetPilot was introduced at CeMAT 2005 in Hannover as a concept study. The steering wheel integrates all main operating functions, making operating levers redundant.
In December 2007 the company launched a new hydrostatic drive internal combustion forklift. Built at the Moosburg plant, the VFG 425s-435s has few mechanical components and so is service-friendly and low maintenance.
Tobias Harzer, head of product management at Jungheinrich Moosburg, says the forklift is "cut out for reversing options" during lorry loading and offloading. The hydrostatic drive enables "fast and smooth change in direction" and fast acceleration.
Both diesel and LPG versions have Volkswagen motors. Bosch Rexroth supplies the variable displacement pumps and motors, and Jungheinrich software controls the forklift's system.
Repeating the design principle first used in the DFG/TFG 425-435 internal combustion forklifts launched in 2004, the counterweight design and high mounted safety steering axle gives the forklift a low centre of gravity. The forklift has improved visibility to the forklift's rear due to the counterweight's low top edge.
Toyota Material Handling Europe (TMHE) launched its "most advanced" internal combustion counterbalanced forklift for the European market last year.
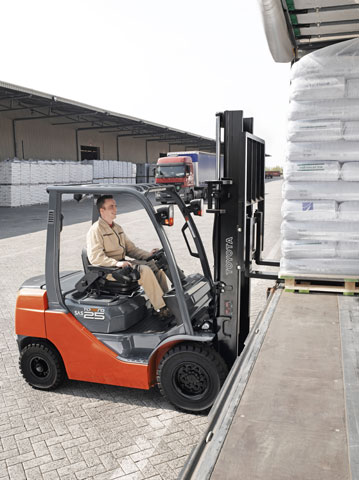 Toyota Tonero loading a truck. |
The 1.5-3.5 tonne (3,307lb-7,716lb) Toyota Tonero that comes in diesel and LPG engines includes Toyota's System of Active Stability and Operator Presence Sensing system. TMHE boasts that the forklift exceeds the emissions standards of EU directive 97/68/EC Emission Stage IIIa and is 99% recyclable at the end of its life. For example, besides the forklift's iron parts, plastic components like the dashboard can be melted down and reused, and engine components that include various metals and allows, are recyclable.
It is built at the ISO 14001-certified Toyota plant in Ancenis, France and its parts suppliers are also ISO 14001 certified.
Forklift users are able to customise the forklift through the Toyota Tonero+ formula, consisting of Tonero+Safety, Tonero+Productivity, Tonero+Durability and Tonero+Comfort. For example, the Tonero+Safety option provides a load weight indicator, maximum drive speed setting and features limiting the maximum drive speed and acceleration rate when moving raised loads.
In May,
Crown Equipment Corp introduced the RC 5500 Series stand-up counterbalanced forklift, which it named "most versatile performer" in the warehouse. Crown says it is thus named because the forklift can be used to load and unload trailers, transport and stage products in the warehouse and store products in racks.
Also new with the series is Crown's FlexRide suspension that the US manufacturer says provides a ride comparable to a "luxury automobile" while protecting operators from shock and vibration while travelling on rough floors and dock plates. FlexRide is currently only available on the RC 5500 Series.
Crown also launched InfoLink, a wireless fleet management tool. Crown told
Forkliftaction.com News it is the first to build a fleet management system as other manufacturers partnered with third party providers to offer customers fleet management systems.
Doosan Infracore of Seoul, South Korea says in the past year, it continued its priority of customising its forklifts for individual needs, meeting environmental standards and enhancing its forklifts' ergonomics. "We are taking steps to maintain a competitive position in the market despite challenges from low-priced models from China," a company spokesperson says.
The spokesperson says China's low-priced models were stepping up the competition and Chinese manufacturers were expanding their shares at the low-end of the American and European markets.
"Demand for operator convenience is increasing, particularly in advanced markets. We are satisfying these needs by reducing noise, vibration and harshness, as well as by developing products that are ergonomically impressive."
Port equipment manufacturer
Kalmar Industries of Stockholm, Sweden introduced the DCF 80-100 empty container handler in November 2007, replacing the DCE model in the European and North American markets. The F-generation unit is based on the same modular platform as Kalmar's DRF reach stacker, and is available with a hook or twistlock attachment. Compared to the older DCE model, the DCF container handler has 10% faster lifting speed because of the rapid response provided by improved hydraulics with variable pumps. Kalmar says it offers the fastest lifting speed on the market.
The new unit also has a more powerful engine and a fully automatic electronic transmission that provides better torque and acceleration over existing models on the market, Kalmar says.
The EnvironmentLinde is investigating technologies like fuel cell drive and start-stop automatic drives to save electric energy and fuel. In the automotive industry, start-stop automatic drives help save fuel by shutting off the motor when the car stops before a red traffic light. The motor restarts when the gas pedal is pushed. Forklifts are idle for about 30% of their operating time. Linde says there is no definite release date for start-stop automatic drives with its forklifts but it is examining the technology.
Meanwhile, Linde continues to save energy at its own facilities. About 90% of energy consumed by air compressors in Aschaffenburg's Plants I and II is wasted in the form of heat. The heat is recovered and used to produce hot water for staff showers or the cafeteria kitchens.
Linde claims it is generating savings of around 16 million kilowatt-hours at Plant II alone - equivalent to the annual heating needs of 140 family homes.
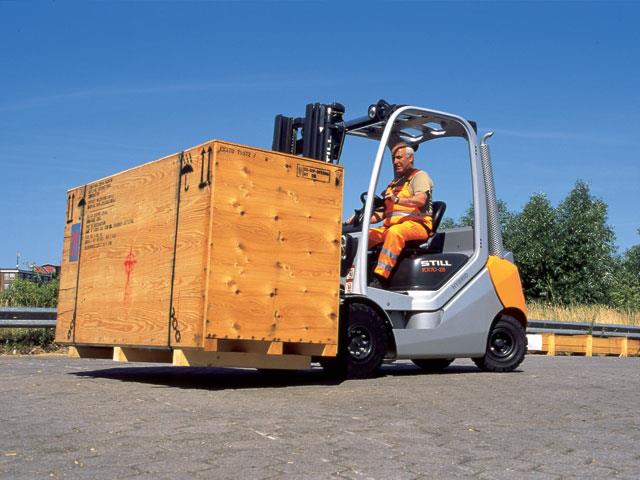 Still says the RX70 is the first forklift equipped with hybrid technology drive. |
Still says the RX70 diesel hybrid forklift introduced in 2006 is the first forklift equipped with hybrid technology drive. A 2.5 ton RX 70 consumes 2.5 litres per hour and emits 6.4kg (14.1lbs) of CO2 per hour of operation. An average passenger car travelling at 50km/h (31 mph) emits (21.8lbs) 9.9kg of CO2 per hour, according to a German transport emission model developed in 1999.
In April,
Jungheinrich and other members of a research group presented a new fuel cell concept at Hannover Messe in Hannover, Germany. The group exhibited a Jungheinrich forklift that ran on direct methanol fuel cell technology. Infrastructure for handling methanol was said to be cheaper than for hydrogen. Both hydrogen and methanol fuel cell technologies could possibly be used together in the future to power large fleets of different forklift types.
Jungheinrich has a group department that specialises in quality and environment issues. The company's environmental policy is comprehensive and is accredited to ISO 14001 standard.
The Moosburg factory is Jungheinrich's "show plant" where over 98% of waste product is recycled. Employees are also regularly informed, qualified and motivated according to their tasks in environment protection.
Hyster Company president Paul Laroia says his company is committed to staying on the forefront of "green research and technology" every step of the forklift manufacturing process. Hyster forklifts are made in plants meeting ISO 14000 environmental standards.
Hyster says all its forklifts exceed 2007 EPA standards and "most" meet the more stringent 2010 CARB emission standards. It boasts that the Hyster GM 2.4L engine has the lowest overall emissions of any 3,000-7,000lb (1,361kg-3,175kg) forklift in the industry.
It also claims to be the first company to use working fuel cells in actual applications. Hyster is actively working on a few areas of alternate energy including hydrogen fuel cells, advanced energy storage devices and battery technology.
Doosan Infracore says it developed engine-powered forklifts in step with each stage of environmental regulatory changes, heavy metal restrictions, recommendations on environment-friendly material use and noise limits in the EU.
Kalmar will introduce "Working Ecodriving" this year. The approach works by teaching drivers the most effective way to operate forklifts, with expectations that fuel consumption can be cut up to 30% without time loss while saving costs and the environment.
Safety Tip-overs were paramount in the concerns for
Forkliftaction.com News Safety First columnists last year.
Joseph Hrinik, who notes that this form of accident was prevalent in 2007 operator fatalities, says increased employer effort is required in providing proper operator training and supervision and in requiring that operators have and use proper safety restraints.
"Most countries do not need new or additional safety standards," he says. "What is needed is aggressive enforcement by the OHS/OSH agencies of their current forklift safety requirements. These agencies should verify the training content and also determine the adequacy of the training that employers claim they have provided to forklift operators."
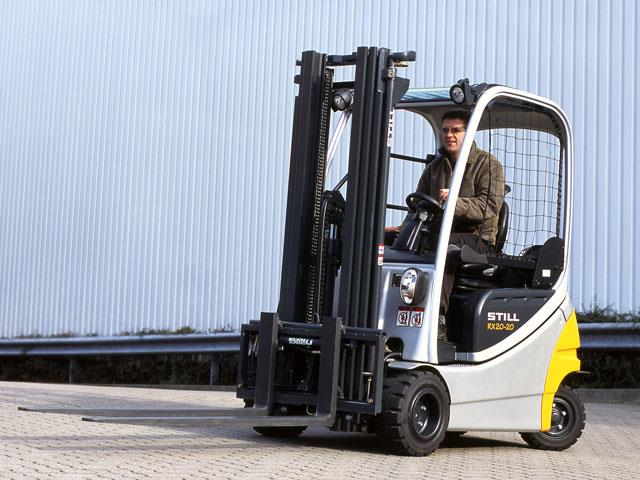 Still's "netProtect" ensures the safety of the forklift operator. |
David Hoover also stresses that tip-overs kill more workers than anything else. "Many operators do not wear the seatbelts and most belts are of no higher technology than they have been for 30 years," he points out. "Even the bright orange belts with electronic cut-outs are not enough; they are easily defeated by bucking them and then sitting on the bucked belt. Putting a guard over the operator like on a roller coaster would not be well accepted, at least here in the US, so what about a 'smart belt' that knows if it is buckled around a person and won't let the lift start or go into gear without being buckled and disables the lift if it is taken off."
Hoover says he rarely, if ever, sees fatalities if an operator is buckled "and it makes the injuries much less severe in both head- on collisions and tip-overs, so coming up with a better belt would save at least 25 lives in the US and many more across the world, by sending the message: "Buckle up or this forklift is going nowhere".
He would also like to see more integrated warning systems in the lift circuits of all forklifts, "creating a warning and eventual shut-down if capacity limits are exceeded". "I know some narrow aisle lifts have built-in scales that may do certain things and that the SAS system has some features having to do with tilt, but I would like to see a more across-the-board approach on all makes and models. This would not only improve safety but also reduce wear and tear on the lifts."
Hoover says he knows companies that regularly lift more than recommended. "They know they are not doing the right thing, but this would engineer safety into the lift and not allow them to perform these types of unsafe operations, or at least not without plenty of warnings being given."
He would also like to see better and more innovative warning systems to warn passers-by "without driving the operator insane (which results in them doing nasty things to the warning devices and defeating them)" .
"I like the idea of the new 'talking alarms' that use a voice to warn people, but I would like to see a sensor integrated into the back of forklifts that provides extra warning to both an operator and pedestrians when the forklift starts to get really close. Taking the concept of proximity sensors to a new level would be a system that could engage the brakes if a forklift backed too close to a person, wall or machine. The cars of the future are starting to use this on the roads right now, by engaging the brakes of a following car when the car in front brakes hard or gets too close," he says.