Forkliftaction continues its reporting on the finalists in this year's IFOY awards with reviews of the contenders for the AGV category honours.
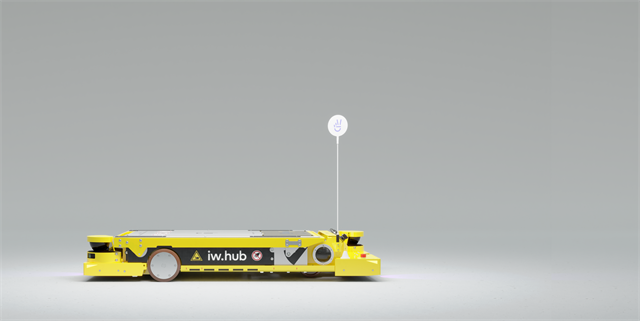 iw.hub |
idealworks: iw.hubWith the iw.hub, idealworks, a wholly owned subsidiary of the BMW Group, delivers an autonomous mobile robot (AMR) at a competitive price. According to the manufacturer, the innovative solution is up to 50% cheaper than existing solutions on the market, while offering the same functionalities.
The AMR measures 641x1,440 mm and has a minimum underride height of 22 cm. In mixed traffic - with other, manually operated and/or autonomous vehicles - the iw.hub reaches a speed of about 2.2 m/s (just under 8 km/h). This makes the iw.hub one of the faster AMRs. The maximum payload is 1,000 kg.
At least as important for the application is the flexibility of the AMR, which drives completely autonomously with the help of Simultaneous Localisation and Mapping (SLAM) navigation technology. A starting position and the desired pick-up locations are all that is needed. The robot then independently creates a map of the surroundings.
Sensors on the AMR continuously scan the environment and optimise the route in real time. Temporary obstacles are detected by the AMR and bypassed independently. Even if a load is not positioned correctly, the robot detects this with the help of a 3D camera on the front. In this case, the iw.hub automatically corrects its position so that the loads are always picked up correctly.
A lithium-ion cell from the BMW i3 powers the iw.hub. A fully charged battery is sufficient for at least eight hours of operation. Intermediate charging is possible via any standard 220 V socket.
The AMR is programmed to charge only when the battery capacity is less than 50% and no transport orders are scheduled. When approaching the charging station, the iw.hub automatically checks its position and corrects it, if necessary, with the help of reflectors mounted in the charging station. A charging cycle takes 1.5 hours.
According to the manufacturer, the system can be implemented in about two days, without structural changes. Deployment in a new environment is shortened by the support of an AI-based digital twin.
The iw.hub has a cloud-based control platform (AnyFleet) that enables standardised integration of third-party devices based on the VDA 5050 interface. The control platform is used for mapping, order control, and fleet and traffic management and has an intuitive user interface. This makes it easy for new users and logisticians to learn and operate the system.
IFOY test verdict:
The iw.hub mobile robot from idealworks is fast, fully autonomous and automatically adjusts its route as needed. It is a particularly flexible solution that can be installed in just a few days and is also attractively priced, bringing a factory-in-one-day within reach. Even the battery charging stations can be installed quickly and flexibly. All that is needed is a standard 220V socket. HAIPICK A42T |
HAIPICK A42TThe HAIPICK A42T is the world's first telescopic autonomous case handling robot (ACR). The telescopic lifting function allows a flexible range from 250 mm to 6.50 m. The robot itself maintains its standard height of 3.70 m.
The advanced robot enables intelligent and efficient goods-to-person picking in warehouses with irregular heights. The available space is utilised to the maximum, resulting in high storage density, even in environments where the warehouse height varies.
The system intelligently identifies, locates and collects the desired item. Each storage location has a DM code for this purpose. The HAIPICK robot first scans the position code and then the bin code.
The system is designed for mixed picking of both totes and cartons of different sizes. The ACR can pick up to six totes at a time and transport them to one or more workstations.
Obstacles such as sprinklers, doors, fans and other height-limiting objects are registered in the HAIQ software platform. The ACR knows where the obstacles are, can adjust its height and continue the route. To further increase safety, the mast can be equipped with additional sensors.
By default, the robots are active in a closed area. If pedestrians are also on the move there, the system can be expanded with additional sensors. These detect possible obstacles and ensure that the robot comes to a safe stop.
ACRs included in the HAIQ software platform can automatically switch from one area of operation to another. The robot can also control lifts if they are connected to the HAIQ software platform. In that case, DM codes are installed in the lift to control the ACR and allow it to be used on multiple floors.
The lithium iron phosphate battery allows for quick and easy intermediate charging. According to the manufacturer, the battery can be recharged in just 45 minutes. This makes the system suitable for 24/7 operation.
The HAIPICK system is scalable and can be easily expanded with more ACRs, more workstations or more racking systems depending on requirements. Other storage systems such as miniloads or shuttles can also be integrated.
Unfortunately, the HAIPICK A42T could not be verified live in Dortmund for testing. Verification was carried out by means of video streaming and manufacturer interviews.
IFOY test verdict:
The HAIPICK A42T is a unique autonomous case handling robot (ACR). Thanks to the telescopic lifting function, the robot's mast can be extended to a height of 6.5 metres. It can also be used in environments where the storage height varies. The height of the robot is automatically adjusted to achieve a high storage density.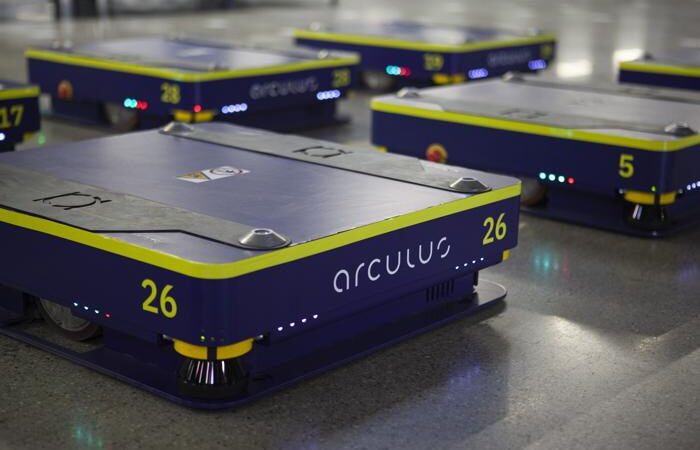 arculee 2 |
arculee2The arculee2 from the manufacturer arculus is the successor to the arculee1. It is available in three sizes with load capacities of up to 1 T.
The arculee2 is controlled by a robot control unit that enables fleet learning and over-the-air updates.
All data converge on an integrated card from which the AMR is controlled. The advantage is that the number of components, and thus the costs, are significantly reduced. Ultimately, users get more for their money.
In combination with the arculus Modular Production System, the arculee2 transports containers and pallets from one workstation to another without predefined routes. The AMR locates and navigates freely based on sensor data fusion.
The robot collects information using multiple sensors, accelerometers, cameras and even body microphones. Based on this data, the arculee2 creates an image of the environment and the robot's performance. This enables dynamic driving and navigation behaviour and also helps to optimally and efficiently plan reloading and service.
The exact positioning also behaved extremely flexibly in the test. For example, if the load was not completely straight, the arculee2 recognised this and easily adjusted its position in relation to the load.
Most of the calculations are performed in the robot itself with minimal energy consumption. Thanks to the patented electronics and software architecture, upgrades can be quickly and easily transferred to AMRs, for example via 5G or WiFi.
arculee2 is a universal platform. Its functionality can be extended with various attachments if required. The integrated battery is charged online, ensuring maximum availability. New charging points can be added flexibly and within just 10 minutes.
The test team is convinced that this system can further increase efficiency in both production and logistics environments while saving valuable space. The availability of goods remains high.
IFOY test verdict:
As the variety of products in AMRs grows rapidly, the differentiator is not so much the hardware as the software. Easy implementation and integration as well as management and possible changes are in demand. In this regard, the arculee2 performs above average compared to the competition. The arculee2 is extremely robust, extremely compact and, thanks to the flexible customisation and update options, also future-proof.See our AGV feature here.