In the countdown to the 2019 IFOY awards,
Forkliftaction News is sharing the jury findings on each of the finalists. There were three finalists in the AGV and intralogistics robot category. They are presented in alphabetical order.
 Jungheinrich Miniload STC |
Jungheinrich Miniload STCThis is Jungheinrich's first intralogistics solution that is not intended for moving pallets.
Jungheinrich states that the STC is the most powerful miniload in its class worldwide and, therefore, allows maximum throughput. The acceleration and lifting speeds are indeed very fast, as the data of the IFOY test team shows. The driving speed and acceleration claims were verified in testing.
During development, special attention was paid to energy efficiency. For example, the braking energy is returned to SuperCaps for less energy consumption at the next acceleration. According to Jungheinrich, this can reduce energy consumption and operating costs by up to 25%. The savings are available from the very first use, because the connection value of the system is lower. Also, the generated energy is not fed back into the grid as peak load, but is stored internally temporarily and used immediately, if possible.
In addition, intelligent energy management and innovative construction keep energy consumption at an unprecedented low level.
Jungheinrich uses a scalable, lightweight aluminium mast, which consists of only two parts and in which the drive is integrated. This approach makes the structure approximately 14% lighter and offers the possibility to choose different load handling devices. The system is suitable for the highly efficient and space-saving storage of small parts in containers, trays or boxes.
With the new rail concept, Jungheinrich also uses an aluminium profile, which allows the crane to drive just above ground level. This enables a lower approach size (460 mm instead of 530 mm) and with this, Jungheinrich sets a new standard in this class.
Despite its light weight, high stability is guaranteed, even at the maximum scalable height of 25 m. Jungheinrich estimates the ideal system length of an installation at approximately 110 m. Thanks to the equally unique version with double drive belts, the crane is always moved straight and evenly over the rails.
The powerful miniload can be used in ambient temperatures from +2 deg C to +40 deg C. A variant that can also be used in a frozen environment is expected at a later stage. With this fully in-house developed and manufactured system solution, Jungheinrich is less dependent on external providers and can provide better and faster service.
IFOY test verdict:The Jungheinrich STC sets new standards when it comes to performance, storage density and energy efficiency. It is, according to the manufacturer, the world's most powerful miniload in its class. With fast acceleration and travel speeds, warehouse performance is significantly increased. The SuperCaps, as part of the total drive system, enable particularly intelligent and economical energy management.
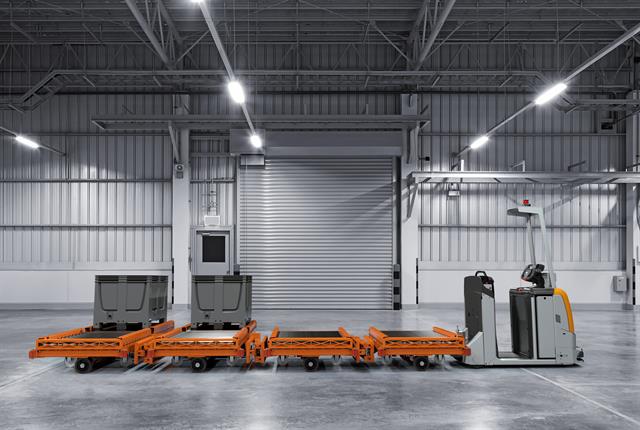 STILL automated tugger train |
STILL Automated Tugger Train with LTX 50 and Automated Load HandlingMore intralogistics processes are becoming fully or partially automated. With the combination of the LiftRunner and the LTX 50 tractor, STILL presents a solution that, for the first time, takes care of both transport and load handling fully automatically.
The standard LTX 50 electric tow tractor, with a maximum pulling force of 5,000 kg, is equipped with automation components from KION sister Dematic. The most striking feature is the automation arch mounted on the front of the truck, which integrates all the necessary components such as laser navigation, WLAN, safety PLCs and two Sick scanners. The KION Option Box, or KOB, is mounted under the hood. This KOB enables easy communication with the controls of the vehicle.
A major advantage of this combination is that the processes can, if desired, also be carried out manually. In addition to the fully automated solution nominated for the IFOY Award, a variant can be chosen in which only the transport is automated and the handling takes place manually, or another version in which the load handling is automatically taken care of and the transport takes place manually.
The automated drop-off and pick-up locations do not require their own power supplies. The roller conveyor on these stops is driven by the trailers of the goods train, which are equipped with 24 v contacts for this purpose. As soon as the trailer is at the right location, contact is made and the roller conveyor starts to run. Data photocells provide communication between the trailers and the stationary roller conveyors. This significantly increases the flexibility of the solution. The system is also characterised by its relative simplicity and relatively low investment.
Because load handling is now also automated, heavier loads can be handled than before. Where the weight of the load was previously limited to approximately 500 kg, loads weighing 1,200 kg per trailer can now be easily transported.
Safety is guaranteed by the safety PLCs and the Sick sensors in the automation arch. In addition, LED lights in the arch make it clearly visible to the environment when activities are carried out by the combination. Furthermore, the truck is equipped with a BlueSpot that only works when there is actual driving. Moreover, the bundling of the transports reduces the intensity of the internal transport. And that obviously benefits safety.
During the IFOY test week, the STILL LTX with LiftRunner provided trouble-free transport. The lifting and delivery of loads through unmanned transport was smooth and controlled.
IFOY test verdict:STILL LiftRunner with LTX makes it possible to handle both transport and load handling fully automatically. The system is scalable, easily adaptable and can be partly manual. The solution is ideal for the supply of products to and removal from production lines, for example, or other repetitive work. By fully automating these processes, reliability and safety increase, while transport and handling are carried out more economically.
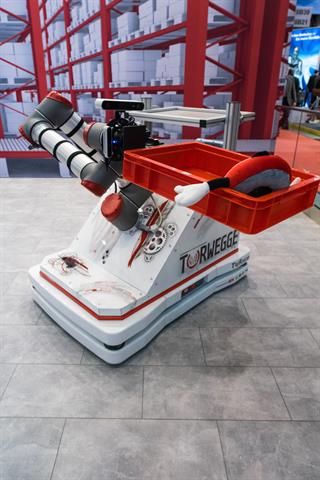 MANIPULA-TORsten |
Torwegge MANIPULA-TORstenIn 2017, Torwegge won an IFOY Award with the TORsten AGV. This year, the company has been nominated for a further development of that award winner: the MANIPULA-TORsten, a mobile manipulator.
The MANIPULA-TORsten consists of a compact TORsten AGV. It is about the size of a europallet and only 230 mm high, on which a manipulator has been mounted: in the case of the IFOY nomination, a PILZ robot arm. Other configurations are also possible.
The system shown during the test days can be used for order picking, e-commerce activities or other tasks where the combination of a precisely navigating AGV and a manipulator offers advantages to perform tasks more efficiently and at lower costs. The combination of both techniques avoids empty transportation trips. The system can be used for both goods-to-robot and robot-to-goods operations.
Using laser contour navigation, the TORsten AGV navigates with a maximum deviation of 5 mm. As soon as the vehicle is at a location, the manipulator positions itself in the current location and the picking process can begin.
A deep image camera is used to reposition the manipulator each time. This camera recognises the tray or box to be picked and automatically identifies where exactly it is to be picked.
The nominated solution offers a load capacity of 6 kg. However, depending on the manipulator configuration which is placed on the AGV, heavier alternatives are also possible. One of the factors determining this is the load capacity of the AGV (1.2 T).
The entire operation is controlled by the Robot Operating System (ROS), which was developed in cooperation with Aachen University. In this middleware, all system components can be easily integrated and configured according to the plug and play principle. ROS can also communicate with other system components in the warehouse.
Because the energy consumption of the AGV is significantly higher with this new nomination, the system is equipped with an inductive charging system. Floor contacts, eg. at fixed AGV stops, allow the battery to be charged quickly and without contact, thus ensuring a high level of availability. However, this charging principle could not be shown during the IFOY test days, as it requires permanent adjustments to the floor which was not possible in the test hall.
During IFOY testing, MANIPULA-TORsten performed the predestined tasks well. The AGV once again proved its practical navigation and transport capabilities. The robotic arm certainly added a further dimension.
IFOY test verdict:The techniques used make the system very accurate and enable an efficient and flexible custom-made automation solution. The combination of techniques opens the door to more efficient, fully automatic transports and goods handling.