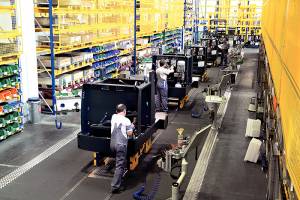 Production at all Jungheinrich plants is up and running |
Germany's forklift manufacturers appear to be maintaining production and services in spite of the spread of coronavirus.
"The production at all
Jungheinrich plants is up and running," says spokesman Benedikt Nufer. "As of (24 March), production is ensured by various measures. However, due to the stricter measures taken by many countries and the resulting backlogs at many external borders, there may be delays in supplying our plants and delivering our products. We are working flat out to minimise the effects and pursue pragmatic solutions."
Nufer says hygiene measures have been stepped up in accordance with WHO guidelines "and we are providing comprehensive, continuously updated information on measures to prevent infections. This includes strict hygiene and behaviour guidelines, a global travel ban and a significant reduction in meetings and conferences."
Jungheinrich has activated additional office space in which departments that are essential to operations, such as IT, are duplicated. "The employees in these departments are split between the existing and new sites in order to reduce the risk of infection within the teams," he explains.
"In the current situation, protecting our employees and safeguarding our ability to deliver are our top priorities. Jungheinrich has established a crisis team for this purpose, headed by the Board of Management, that makes daily decisions based on the current appraisal of the situation.
"A number of preventive measures have also been put into place to protect the workforce. Production at all plants is ongoing, and after-sales service technicians are deployed throughout the world.
"So far, we have been able to prevent the situation having a negative impact on Jungheinrich's supply chain and production processes, and our ability to deliver is currently stable" he notes.
Production is also continuing at
Linde Material Handling. A company statement assures customers that "we ensure that material flow is maintained - this includes the continuity of public life, the economy and the necessary supply, not least with food and medical supplies".
The statement stresses that the safety, health and well-being of employees is a top priority. "Linde Material Handling has introduced comprehensive measures to protect our employees. A crisis management team has been set up; rapid implementation of measures is guaranteed across site and national boundaries."
According to the statement, while production continues, delays may occur at some sites due to border closures and other official measures.
"We are trying to keep the impact on our customers as low as possible," it continues, assuring customers of ongoing service and repairs. "There are restrictions only in the 'red zones', where the freedom of movement of everyone (including our service technicians) is currently restricted."
Linde will prioritise important supply chains like medical and food suppliers, so warns that it can't rule out delays and waiting times. The supply of spare parts, however, is guaranteed for the next months.
KION stablemate
Still notes on its website that it will continue to look after customers and partners "as best we can and will be there for them whenever they need us". This service is now moving towards digital communication channels in order to reduce the direct physical contact, where possible. "Personal meetings of employees, customers and partners who are or were in one of the declared risk areas are avoided," it notes.
The company is sticking to its service contract obligations and insists its supply of spare parts is intact. "Our technicians are equipped in such a way that maintenance and repairs can be carried out as usual and ideally on the first visit," Still states.
Across the border in Austria, production is also continuing at
Liebherr-Werk Nenzing, according to Wolfgang Pfister, head of strategic marketing and communications.
"Our manufacturing facility has not yet been affected. There are several quarantine measures in operation ... (which mean) that more than 100 employees cannot come to work anymore. However, the supply of our factory (since we are located outside Nenzing) is still possible," he says.
"The protection of human health is our top priority in all of our business activities. We are aiming to reduce the risk of infection among our employees and their relatives as well as our business partners," Pfister emphasises. "Our HR departments, company doctors, paramedics, safety specialists and all employees working in production and administration are helping us to make the right decisions and act in the most decisive way possible. We are also working closely with several local, national and international authorities."
Specific measures adopted by Liebherr include a ban on staff travel and visits by external partners to the company. All external and internal events have been cancelled or postponed, while internal meetings, where they go ahead, are limited to five people, who have to maintain a minimum distance of two meters at all times.
Meanwhile, in Italy,
Bolzoni, which was still in production
last week, has announced that, in light of the COVID-19 emergency and taking into account new government indications, it has suspended the production at its Italian factories in Podenzano and Prato, from 23 March to 3 April 2020.
While production has halted, the company assures customers that "full operations of the sales and after sales" divisions are being delivered through remote work.
Sideloader manufacturer
Baumann has also halted production but, following discussions with the Italian Manufacturers' Association, is confident it can continue supplying parts due to the strategic role of logistics equipment in the supply chain.
"We are also ready to restart production at short notice as soon as it becomes acceptable to do so," the company says in a statement.
In another development, the industry associations representing the equipment sector are meanwhile calling on European authorities to roll back the deadline for Stage V emissions regulations in the wake of the COVID-19 pandemic.
In a joint letter to the European Commission, a number of industry bodies including
FEM are asking for a moratorium on the application of 2020 and 2021 deadlines listed in Regulation 2016/1628/EU on exhaust emissions.
The associations point out that the COVID-19 outbreak is causing complete interruptions of supply of parts and components. Without essential parts like tyres, axles, hydraulics, lighting and electronic equipment, manufacturers are effectively prevented from completing the construction of the machines by the imposed deadlines. As a result, they will not be able to place the machines on the market with the transition engines they had already acquired. Since it will be no longer possible to use them, these engines will have to be scrapped, which will lead to avoidable economic damage and unnecessary waste of raw materials and resources.
"The situation is critical," says FEM secretary general Olivier Janin. "A temporary moratorium must be granted, with deadlines postponed until the situation can be reassessed. Neutral from an environmental point of view, the measure would prevent further economic damage caused by the COVID-19 pandemic to our manufacturing industries and the jobs that depend on them."