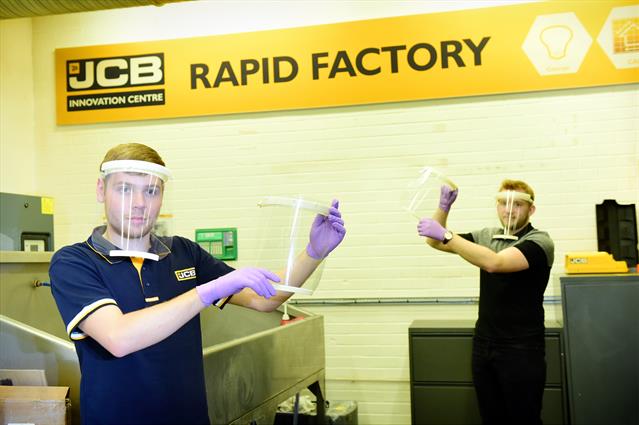 JCB's Joe Mumby and Joe Bagley are producing medical grade visors for NHS staff |
Materials handling manufacturers are applying their skills to address shortages of personal protection equipment (PPE) around the world.
In the UK, JCB and a team of volunteer employees have set up mini-production lines to come to the aid of the nation's NHS heroes in need of personal protective equipment.
Principal electronics engineer and father-of-two James Morley - who is normally based at JCB's World HQ in Rocester - has converted the garage at his Derbyshire home to produce vital supplies.
Inspired by his efforts, JCB has re-opened its Innovation Centre at the World HQ so colleagues and tooling and moulding engineers Joe Mumby, 22, and Joe Bagley, 25, of Ashby de-la-Zouch can also volunteer and have free use of the company's 3D rapid prototype machines to help produce medical grade visors for NHS staff.
The World HQ and JCB's other UK manufacturing plants fell silent last month as a result of the disruption caused by the coronavirus and the vast majority of employees being furloughed.
So far, the volunteer production line set up at JCB has produced 50 visors for distribution to surgeries in the Rocester and Uttoxeter area with the help of material donated by the JCB Academy.
With the visor material now exhausted, the volunteers are concentrating their efforts on producing hundreds of head bands required for the visors before despatching them to a Warwickshire company for final assembly.
Meanwhile, in the United States, the Raymond Corporation has also stepped up in the PPE challenge.
Michael Field, Raymond president and CEO, says: "Like everyone, we at Raymond have heard the appeals for protective equipment from our local healthcare workers battling the COVID-19 pandemic.
"As an essential business, we have an acute understanding of the need worldwide to provide our heroic doctors, nurses and first responders with the PPE equipment they desperately require.
Raymond has the ability and desire to utilise our vast production capabilities to support those crucial employees.
"Within the past few weeks, thanks to Raymond's innovative engineering team and associates, our facility in Greene has begun to 3D print and assemble face shields. We are producing more than 2,000 face shields to be dispersed to our local hospitals and emergency responders."
According to Field, Raymond will continue to monitor the evolving situation to determine how best to support healthcare workers.
Last month, Chinese battery vehicle giant BYD turned its attention to the global face mask shortage by opening what it claims is the world's largest mass-produced mask plant.
The plant is able to produce 5 million masks and 300,000 bottles of disinfectants per day. This allows the firm to help alleviate severe shortages that have affected hospitals and agencies across China in the face of the global COVID-19 crisis.
"A production line for high-quality face masks requires about 1,300 parts for various gears, chains, and rollers, 90% of which are BYD's self-made parts," says company spokeswoman Sherry Li.