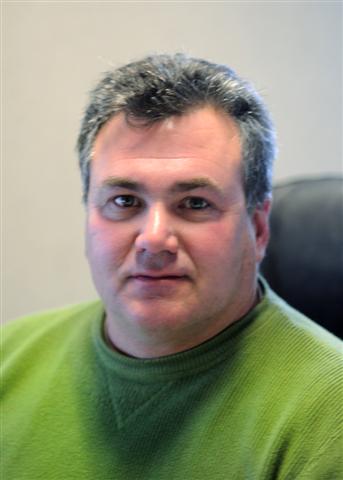 Frank Sterner |
Most operations that run a large fleet of forklifts tend to select a single new forklift manufacturer because it's more convenient dealing with a single company when arranging purchase or lease agreements. But that is not the primary consideration. The big issue is maintenance.
Full-service leases are supposed to cover maintenance costs up-front. Ideally, they allow you to plan maintenance schedules and costs, and then forget about it for the duration of the lease.
There are two problems with this pretty picture. For one thing, most full service leases do not cover repair costs on the failure of components that are out of factory warranty, or on the failure of wear items such as brakes, etc. You can never be absolutely certain what maintenance costs will be.
On the face of it, this is an additional argument for selecting a single supplier, since it means that you will only have to stock one set of parts and train your people on one machine (or at least machines from a single manufacturer). True, this will save you a little, but at what cost?
Not all forklift manufacturers are good at everything that a forklift does in your operation. There are just too many variables. Electrics are quiet, inexpensive and non-polluting, but of limited range. In some narrow-aisle warehouse applications, turning radius can become a major consideration. In extreme cases, turret trucks may be required.
To get the most efficient vehicle for every job, you would have to determine the features and characteristics required for that job, and then buy the necessary number of forklifts from the manufacturer who makes the best truck with those features and characteristics - and then repeat the process for every job in your operation. A multi-location facility could easily end up with four or five different makes of forklift.
Is this the making of a maintenance nightmare? Not necessarily.
Remember, you are still only using one brand of forklift for a given task, and because you have selected the brand with the best performance for that function, your maintenance for that brand is likely to be reduced. The periodic service requirements are the same, and component failure is less likely to occur if the vehicle is better designed for that specific application.
Keeping a larger inventory of parts may cost a little more to begin with, but maintaining that inventory over time should result in no significant additional expense.
As for training, it may be possible to specialise there as well. For example, instead of training two people on maintenance for a single brand, you might train each of them on one of the brands in use - for little or no additional expense.
New vs. RefurbishedAnother accepted truth that may no longer be true is that refurbished forklift trucks, while less expensive than new ones, are less reliable and therefore not a good investment.
With the ever-increasing costs of capital equipment, refurbishing used forklifts has finally become big business. Not so long ago, the market for reconditioned forklifts wasn't big enough to justify the expense of setting up an assembly line to tear down, inspect and re-assemble a vehicle with enough quality control to ensure reliable operation in heavy use conditions.
The term refurbished means different things to different people. Before you even consider this option, make certain that the unit has been disassembled to the bare frame, sandblasted, painted and rebuilt.
Even the engines should be completely broken down, refurbished and repainted to work and look like new. Purchasing used forklifts can be risky, but buying quality refurbished ones doesn't have to be. For years, third parties have been refurbishing trucks for small users who could not afford new units. They had to do it by themselves to ensure quality, and the number of quality refurbished forklifts on the market was extremely limited.
That is no longer true. The market for renewed trucks has grown to the point where there are now factory reconditioned forklifts available at perhaps one third the cost of new trucks. Not only that, but they are available in quantities that should be attractive to a fleet user.
The quantities are there and the price is certainly attractive, but what are you really getting when you buy a refurbished forklift? Is this where you can find yourself in a maintenance nightmare? Again, not necessarily.
Renewed vehicles have had some run time, a kind of shakedown cruise after which the weak components are replaced. The result is a more reliable unit. Obviously, a refurbished forklift has less of its reliable service life left than a new one, but consider the following scenario: You purchase a refurbished unit at one-third the cost of a new one. You have already skipped the first wave of high maintenance costs that occurs during the run-in phase. You maintain it regularly and retire it perhaps a year earlier than you would a new unit, thus avoiding the last stage of high maintenance as it nears the end of its useful life. You have saved considerably in terms of capital investment, and your maintenance costs may actually go down as well.
Name BrandsThe last myth I would like to bust concerns brand name versus off-brand parts. It seems obvious that an operation running a particular brand of forklifts will be safest stocking spare parts from that manufacturer, even if they do cost a little more. Fortunately, that isn't always true.
Many of our customers in the manufacturing business are up in arms over China because they have become such a tough competitor in recent years. However, the same pricing that creates this frustration with China as a competitor can be helpful to forklift buyers. Factories in China that have produced parts for other name brand forklifts for years are now selling direct in the United States at significantly reduced prices over name brands.
Notice that these are often the same people that made the "brand name" parts. The parts are not less expensive because of lower quality. They are less expensive because of the distribution strategy. There is no dealer taking a percentage off the top. There is no forklift manufacturer using overpriced spare parts as a profit centre in order to lower prices on new trucks and in order to lock in brand loyalty.
With these lower prices for spare parts, there is less reason to fear the possibility of higher maintenance costs with a multi-manufacturer and/or refurbished fleet of forklift trucks. More than ever before, it is possible to put together a fleet based on the only questions that should really matter: what do forklifts really do in your operation, and which forklifts - new or refurbished - can most effectively and economically do the job(s)?
Frank Sterner is a Solutions Specialist at SJF Material Handling Inc, a Winsted, Minnesota-based full service provider of new, used and "renewed" material handling equipment and services. This article, which first appeared in Material Handling Wholesaler, is reproduced with the author's permission.