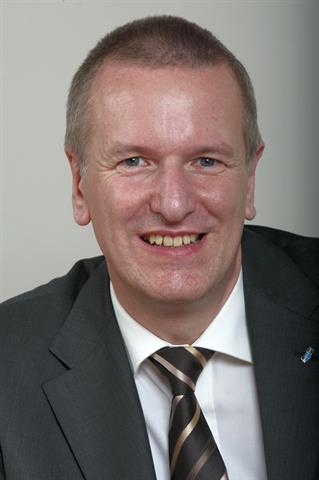 Tim Waples |
Tim Waples is chief executive of the Fork Lift Truck Association.
Site safety is not a destination. It's a journey that requires commitment and attention every step of the way.
Here we offer 10 tips to kickstart your safety culture:
1. Ask yourself: How committed am I?Your commitment to safety (or lack of it) is what always shines through. Your attitudes, expectations and investment are what inspire your workforce.
2. Turn words into actionsDon't rely on safety slogans. They're good, but a lasting safety culture requires more resources. Companies that perform well see safety as an investment, not a cost, and recognise that a strong safety culture has strong financial benefits.
3. Think positiveOutline, in simple terms, what a safety culture looks and feels like for your organisation. Set some clear safety goals.
Instead of focussing on lagging indicators: like accidents or near misses (i.e. the things you
don't want to see), think about leading indicators. Set targets for the positive changes and behaviours you want to see
more of, then make them happen.
4. Don't fall into the complacency trap Bad things never or rarely happen, so your site must be safe, right? Wrong.
Smart organisations stay ahead of the curve, proactively looking for risks and resolving issues before more serious problems occur.
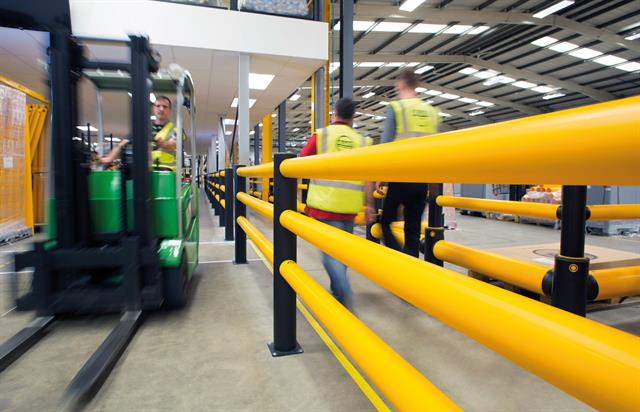 Make safety your priority |
5. Tap into your best resource: your workforceGreat leaders get out onto the shop floor and into the yard. It's where the real work gets done. Take time to chat. Offer easy, open-ended questions. You'll gain respect and more insights than you might expect. The people doing the job usually have the answers.
6. Make safety your priorityCompeting deadlines create pressure to work fast. But safety should be your highest priority every time, otherwise all your other measures are worthless.
When you say "I want this done safely, but I need it by lunchtime" which part do you think the listener hears loudest? Switch your emphasis to safety. Always.
7. Involve and inform staffIn great safety cultures, every employee has a working knowledge of health and safety topics. They know their stuff and recognise when things are going wrong.
In the UK, FLTA Safe Site Award winner Kellogg's invested hugely in making an old and complex site safer, but recognised that toolbox talks, staff meetings and constant engagement were what really made the difference. Hearts and minds were won over. Attitudes changed. Everyone took the view that safety was their concern and took full responsibility.
8. Give credit where it's dueCelebrate positive safety behaviour - don't take it for granted. I've yet to meet an employee who didn't value praise and bask in the recognition of a job well done.
9. Ensure a guilt-free reporting processFeedback is gold dust but getting staff to speak up can be a big ask. Create an environment where constructive criticism is welcomed, and where reporting is not merely guilt-free but praised. No-one should fear they will be ignored or - worse still - punished for coming forward. In great safety cultures, transparency and integrity are undeniably fundamental.
10. Don't stop nowCommunication, communication, communication. Keep safety alive through every channel available. And make sure that safety is top of the agenda when new recruits are inducted.
And remember, success tends to breed success. When everyone is involved and participation rates are at an all-time high, you can build on the buzz ... giving you further momentum for future initiatives.