Long gone are the days when you must head to the store with a shopping list in tow. Today, e-commerce surrounds nearly every aspect of our purchases - from clothing to furniture to even groceries - making the hustle and bustle of our daily lives a bit easier. While having the world at our fingertips may be a consumer's dream, it's creating an ever-intensifying headache for warehouse and manufacturing facilities with increased resource demands and labor shortages. In order to meet these challenges, facilities need to become forward-thinking and optimize operations. Those that don't will continue to fall behind or risk becoming obsolete.
In the past, manufacturers often turned to expanding the facility footprint to meet increasing resource demands. Doing so, however, brought additional operation costs as well as new labor requirements. Reimagining workflows with innovative process systems will help facilities realize the full potential of already available resources and employee labor. This can be done by improving productivity and capacity, without sacrificing cost efficiency. And it all starts with the right material handling equipment.
Give vehicles the work they were made forAccording to an analysis by
CBInsights that measured overall equipment effectiveness (OEE), the average warehouse operates at just 60 percent of its theoretical capacity, and even the most cutting-edge facilities only reach 85 percent efficiency. While production lines and warehouse operations are only as efficient as their employees and vehicles, employees and vehicles can only be as efficient as their environment enables them to be. Adapting material movement processes is one of the simplest approaches to improving facility performance, time and cost savings.
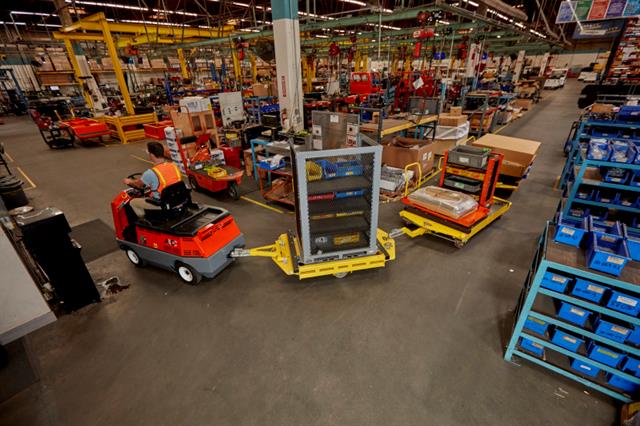 |
Currently facilities rely heavily on forklifts for both vertical and horizontal material movement, but development of new vehicles such as tow tractors and tug systems offer new alternatives with greater ROI potential. While forklifts are a viable solution for loading and unloading trucks, as well as vertical goods storage, when used for horizontal movement, forklifts create undue challenges and risks to the operator, the product and the entire warehouse operation. Without proper training, workplace safety is at risk every time a forklift is on the floor. In fact, OSHA estimates that forklift accidents cause injuries to nearly 35,000 workers every year. And OSHA predicts that 70 percent of those accidents could have been avoided through proper training. Additionally, forklift usage includes additional costs that limit effectiveness and increase operating expenses year-over-year, including frequent maintenance intervals and fuel costs.
Modern manufacturing facilities and warehouses can optimize costs, productivity and safety by focusing on matching task to vehicle. For example, by simply differentiating between vertical and horizontal material handling and movement, facilities can uncover horizontal movement processes where forklifts do not offer advantages over other industrial vehicles, such as tow tractors and tug systems.
Tow tractors and tug systems that are designed for horizonal material movement move higher load volumes in fewer trips - reducing material delivery time by up to 50 percent. Tow tractors and tug systems are also designed with safety in mind. They eliminate the risks created by limited visibility, instability, fork strikes, hydraulic systems and unconventional travel requirements. In fact, since 2002 there have only been eight total OSHA-reported tow tractor incidents, compared to the over 500,000 reported injuries by forklifts in that same timeframe.
Say goodbye to yesterday's workflowA
Global Manufacturing Competitiveness Index (GMCI) study recently found nations who actively invest in exponential manufacturing technologies and innovative ecosystems are more competitive than those facilities that choose to compete on price alone. Systems that can improve product quality and deliver long lasting margin improvement are the key goals driving many of these innovations across industries and workflows.
In the current warehouse environment,
Deloitte estimates that two million manufacturing jobs will remain unfilled by 2025. Warehouses that stick with outdated workflows will continue to struggle to keep up with resource and labor demands Reimagining yesterday's workflows by investing in new material handling systems will offset the need to increase staff size by reallocating quality workers for optimal workflow.
With limited hauling abilities and OSHA regulations, forklifts require additional higher paid and skilled workers to haul materials to key areas of the facility without slowing productivity. Being that forklifts perform best in loading and unloading operations and vertical material movement, using them in other manners leads to a more cumbersome operation with additional trips needed for material movement and greater transportation bottlenecks on the floor.
Taylor-Dunn tow tractors, on the other hand, were made for horizontal material handling movement and are up to four times more efficient than a forklift, allowing facilities to do the same amount of work with far less labor. By using a combination of tow tractors and forklifts, facilities can more easily scale up to meet rising resource demand by reducing transportation bottlenecks in the warehouse, achieving new
labor efficiencies,
increased overall productivity, and
increased safety.
Being four-times more efficient than forklifts for moving materials horizontally through a warehouse, tow tractors further increase productivity by reducing congestion in high-traffic areas due to fewer necessary trips and vehicles. Additionally, less labor needed for vehicle operations helps eliminate labor inefficiencies by moving skilled worked to areas they can create the most value and maximize output.
Get the most out of your investmentTow tractors have minimal upfront costs and a potential to deliver significant savings over the life of the vehicle. By replacing forklifts where performance is sacrificed with more efficient tow tractors, facilities get a cost-effective option up-front that also immediately begins to capture efficiencies and long-term cost savings. In fact, for every forklift that is replaced with a tow tractor, warehouse and manufacturing facilities can see an average of $22,200 in total cost of ownership savings over five years. Savings that is supplemented through increased workplace safety and more strategic labor allocation. Workflow efficiencies and increased productivity also have the potential to generate revenue growth as a direct result of tow tractor adoption.
With lower operating costs, lower acquisition costs and increased longevity, Taylor-Dunn tow tractors have an up to 70 percent lower total cost of ownership when compared to forklifts. By converting forklifts to tug systems in horizontal material flow areas, companies can save millions of dollars in operational expenses - all while creating a warehouse eco-system that stands up to the ever-increasing demands of today's e-commerce world.
For more information, visit
www.polaris.com/commercial.
POLARIS COMMERCIALTel: +1 844 239-3627
Web: www.polaris.com/commercialEmail: send an emailSocial Media: LinkedIn |
YouTubeFind a dealer near you