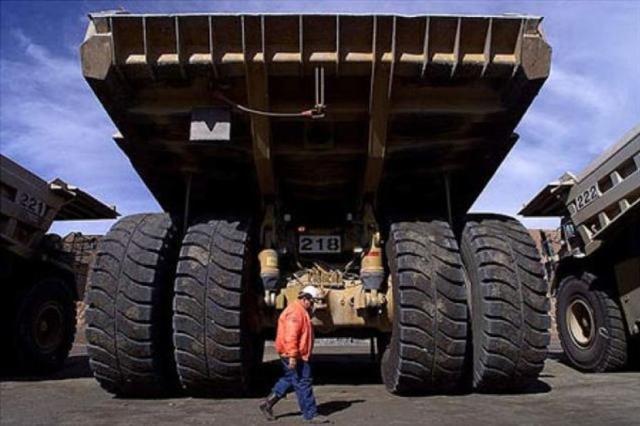 BodyGuard proximity warning system reduces the risk of collision by alerting the driver when someone is detected too close. |
About the ProblemPedestrians and moving vehicles do not mix. Despite safety initiatives used in modern workplaces, too many people are still being injured or killed by moving vehicles and machinery.
Drivers have difficulty seeing people in blind spots or in low visibility conditions (dusty, dirty or low light). In addition to the risk of being hit by a moving vehicle, other outcomes can be very costly to the organisation.
- Higher insurance premiums
- Cost of repair to damaged vehicles or plant
- Expensive equipment and personnel downtime
- OH&S investigations
- Negative reputation for providing safe environment for workers
- Lowered worker morale
Statistics provided by Safe Work Australia (2013)* show 156 (71%) of 220 fatalities in 2010 involved a vehicle or moving equipment. The number of people being trapped or hit by a vehicle has risen over a 3 year period. The figures do not include a further 110 workers killed travelling to and from their workplace and 44 bystanders killed as result of a workers activity.
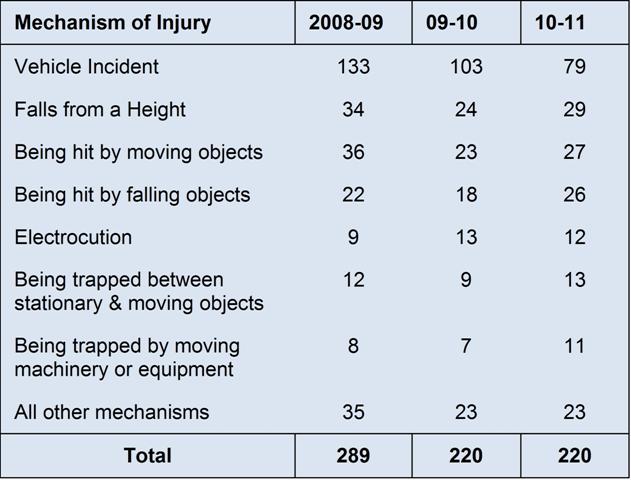 Table 1 Worker Fatalities: Number of traumatic injury fatalities by mechanism of injury |
|
The report highlights several negative consequences of workplace accidents:
- Typical serious workers' compensation claims involved 4 week absence from work
- 25% of all claims resulted in 12 or more weeks off work
- 57,600 notices were issued by authorities
- $15.5 million in fines issued by courts
- Compensation and related costs $60.6 billion (4.8% of GDP)
The cost estimate includes direct costs (payment of wages and medical costs) and indirect costs (lost productivity, loss of future earnings and social welfare payments). The costs do not include the down time for the organisation or vehicle/plant repair costs.
What is being done to reduce risk?There is not one single safety initiative that can prevent accidents occurring. The modern approach involves minimising risk by applying a range of measures, each of which contribute to overall improvement. Safety management programs use "Hierarchy of controls" method (sometimes referred to as "Swiss Cheese" or "Onion" Model) to reduce risk. Various layers of safety processes are used as shown below; (Workcover NSW 2013**)
- Eliminate the hazard altogether. (eg. remove dangerous machine).
- Substitute the hazard with a safer alternative. (eg. replace machine with safer one).
- Isolate the hazard from anyone who could be harmed. (eg. keep machine in closed room and operate it remotely).
- Use engineering controls to reduce the risk. (eg. attach guards to machine to protect users).
- Use administrative controls to reduce the risk. (eg. train workers how to use machine safely).
- Use personal protective equipment (PPE). (eg. wear gloves and goggles when using the machine).
Organisations typically use a variety of these safety layers to lower risk. Initiatives such as driver training, keep out zones, slow zones, rear view mirrors, driver processes, and high visibility vests all help reduce overall risk but an unacceptable number of incidents still occur.
Something more needs to be done to help lower the risks. Blind spots (out of view of mirrors or drivers vision), poor visibility (low lighting, smoky/dusty environment, blind corners) and building entry/exit points all present increased risk of collision. Wearing a high-visibility vest is not effective when the person cannot be seen by the driver.
Rear-view cameras can help but require constant monitoring by the driver (distracting normal driving function). They require cleaning and do not work effectively in dusty/dirty environments. Slow zones and keep out zones, blasting the horn when entering or leaving a building can also help reduce risk. However, these are dependent on the driver following procedures (the "human factor").
What else can be done?Recent advances in technology have led to production of systems capable of detecting people near vehicles. Some of these technologies include radar, ultra-sonic, infra-red, wireless, RFID and GPS.
Each technology has characteristics suited for some applications and not others. No single technology suits all applications.
Each technology has limitations:
- GPS requires view of satellites to obtain fix and is inaccurate when out of satellite view
- Radar can produce false detections from bounce of almost any surface
- Infra-red and ultra-sonic can be affected by heat and interference from industrial switching sources
- Wireless can be affected by reflections from metal objects
- RFID can be affected by low frequency interference and has limited detection range.
Despite the limitations, these technologies offer another "layer" in the overall process of lowering risk to make the workplace safer. RFID and wireless technologies can operate in dirty, dusty and low visibility environments without distracting the driver's normal functions and do not require maintenance (such as cleaning).
When used properly, the wireless and RFID technologies offer a "gap" between people and vehicles (keeping vehicles and people apart). They provide drivers awareness of people or objects close to their vehicle. They can also be used to provide general warnings to pedestrians (such as activating warning lamps when entering or leaving a building).This enables the driver to perform normal duties without distraction.
These systems only alert drivers when a beach of the "gap" is detected. The alert provides awareness to the driver, enabling them to look out and avoid an incident (slow down, stop or swerve as necessary).
Wireless and RFID technology operate by detecting special signals sent from compatible devices fitted to pedestrians or other vehicles. Pedestrians and other objects must be fitted with a device in order to be detected.
BodyGuard proximity warning systemBodyGuard offers flexible risk reduction for:
- Pedestrian to Vehicle
- Vehicle to Vehicle
- Vehicle to Fixed plant or machinery
- Vehicle to Area (operate warning devices when vehicles enter specific zones)
BodyGuard proximity warning system reduces the risk of collision by alerting the driver when someone is detected too close (in the "gap"). The system provides a chance for the driver to stop the vehicle and avoid an incident, offering a second chance to pedestrians that would otherwise not be seen.
BodyGuard improves your organisation's bottom line. Even non-injury collisions can cost hundreds of thousands of dollars every day a vehicle is out of service and downtime resulting from OH&S investigations.
Reducing the risk of collision provides your company real savings by minimizing the chance of collisions occurring in the first place.
The system provides both audible (human voice alert - "Look out! Person behind you") and visual warning. The last 8000 detection events are stored digitally to enable analysis of number of "near-miss" situations and offers a proactive tool for risk reduction management.
Typical applications
- Open-Cut mining operations
- Construction
- Logistics/Warehouses
To see how
BodyGuard can help you lower risk within your organisation, contact Orbit Communications for further information:
w www.orbitcoms.com; e send a messageOrbit Communications:
W: www.orbitcoms.com
E: send a message
T: +61(2) 43 554 554For more company and product information
Click to view the Orbit's ShopFrontIndustry Sources:
*SafeWorkAustralia 2013, Key Work Health and Safety Statistics, Australia, accessed 26th November 2013, http://www.safeworkaustralia.gov.au/sites/SWA/about/Publications/Documents/758/Key-WHS-Statistics-2013.pdf
**WorkCover NSW 2013, Hierarchy of Controls, accessed 26th November 2013, http://www.workcover.nsw.gov.au/formspublications/publications/Documents/yw_heirarchy_controls_2089.pdf