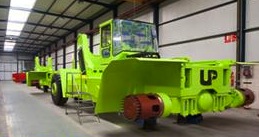 An Up Lifting reach stacker main frame on the assembly line |
What is quality? Can you measure, control or manage quality? How does it affect your business and why?
Melissa Barnett looks at these questions and how after-sales service is inextricably linked to quality in any successful business.
Quality is one of those rare things which are both a concept and tangible. The definition of quality management is the "act of overseeing all activities and tasks needed to maintain a desired level of excellence, including creating and implementing quality planning, assurance, control and improvement. When quality is pursued from design to parts manufacture, through assembly to after-sales service, the cost benefits to the buyer and the seller are both measurable and financially quantifiable. Surveys of customer buying patterns indicate that nine out of 10 buyers make quality their primary purchasing standard
(see more in Quality Digest).
Quality vs priceQuality to many means a higher product price and, in many cases, this is true. But studies also show that purchasers are happy to pay more when they believe they are getting value for money. This seems particularly true in times of economic stress. Keith Miller, sales manager USA and Mexico for attachment manufacture, Cascade Corporation, sums it up succinctly: "In a slow economy, it is even more important to buy quality products because you can't afford to make a mistake."
Antonio Martinez, managing director of Spanish rough-terrain forklift manufacturer Bomaq, notes that a supplier recently told him, "I don't feel rich enough to buy cheap components". Martinez adds that while some may focus on the up-front purchase cost, "the cost is not only the buying price". "You have to think of the whole life of the component or equipment. You have to take into account warranty problems, stop costs, component reliability, operator comfort (and) so many other things that affect the 'global cost' of the forklift. It's nonsense to buy a cheap forklift. The cost of it may end up much higher than the cost difference with another higher quality solution."
Dan Domberg, vice-president of aftermarket customer satisfaction for UniCarriers, says customers have varying needs depending on their size, their industry and their budget. "We believe that we can show the customer that non-price factors such as fuel economy, quality, service performance (and) warranty coverage far outweigh any initial price difference that may exist between offerings." Domberg says that while UniCarriers' forklift prices are competitive, he believes that it is product and service quality that is UniCarriers' advantage. "Our annual customer survey shows that 95% of our respondents believe that UniCarriers' product quality is amongst the best in the industry," he says.
How can companies achieve internationally 'recognisable' quality? There are quality assurance standards which are worldwide, national and industry-focused. For forklift manufacturers, the main internationally recognised standards are the ISO 9000 family which details various aspects of quality management for companies wishing to ensure that their products and services consistently meet customer requirements, and that quality is consistently improved. Environmental standards are covered by ISO 4001, which assists companies to better manage their environmental impacts. Both of these are voluntary, but many forklift manufacturers - including UniCarriers - subscribe to ISO standards. Domberg says that the ISO 9001 certified quality system is mature and well-tested, and is implemented at all levels of UniCarriers' business - from market research and developing product specifications to manufacturing and pre-delivery checks.
Quality control and assurance in action"Quality is not an accident, it is the result of an intelligent effort," according to equipment manufacturer AUSA. Enric Perramon, the company's after-sales director, says that AUSA makes simple-to-use forklifts in the first place but quality is assured by using quality stages AQF1, 2 and 3 at different control points in the production process. He says that this has resulted in almost no defective elements, but new standards and final testing procedures are due to be implemented at AUSA over the next few months.
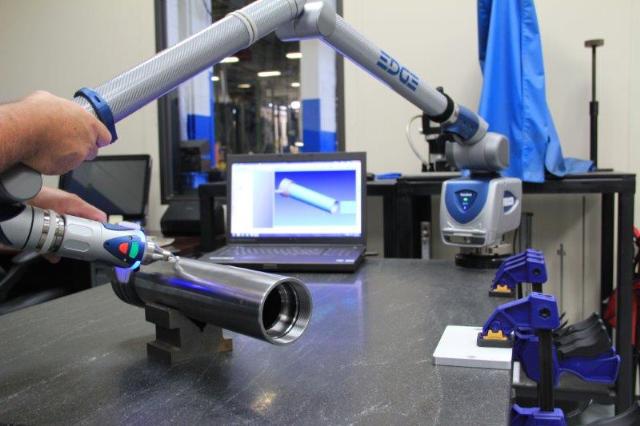 Cascade testing |
Cascade Corporation's motto is "Do it right the first time". Miller says Cascade is not just satisfied with maintaining standards, but continuously striving to improve products and services. "We have an ongoing continuous improvement program throughout the company. All employees receive incentives to provide excellent customer service and produce quality products on time." For its products, adds Miller, there is rigorous lab and field endurance testing prior to release. He explains that after testing, "we do a first article inspection and have a strong focus on vendor responsibility. Post-production, we do weekly audits in shipping to monitor initial quality and we perform sales quote inspections to ensure we have built to customer expectations. We are so confident in the reliability of our products, we have recently announced a two-year "performance pledge" which extends our warranty by an additional year."
Spanish forklift manufacturer Up Lifting offers unique customisation of its products for customers. Roberto Garzo Aguarto, general manager, says that this means engineering and production quality is vital and, for this reason, all key equipment elements are manufactured in-house. "Our quality department reviews each component in each phase of manufacture - cutting, bending, welding - before moving on to the next step. When the machine is finished, testing and recording checks are done on 200 points. We (also) do stringent testing to ensure correct operation of the machine's functions," Aguarto explains.
 Bomaq 4wd rough-terrain chassis in production |
Martinez, whose company has only been manufacturing for one year, says Bomaq sends all its suppliers a pre-control checklist for components. Equipment is checked again during assembly, (and) when complete, every product is connected to a data logging system which stores information including pressures, temperatures, rpm, vibrations noises, etc. in an electronic file for Bomaq's records, in case of later problems. Martinez says that a testing cell for forklifts is in planning stage.
At UniCarriers, quality control starts at the design level. Once the design is validated, the supply chain is monitored using Six Sigma quality assurance procedures. Supplier systems and controls are assessed and rigorous inspections of parts is done to ensure consistent quality. UniCarriers' monitoring ensures that quality levels are 500 defective parts per million or less. As parts move through fabrication, weld or assembly, there are built-in inspections and product audits. Vital welds and other process dimensions are checked and calibrated to international standards by three-dimensional scanners. At the finished assembly point, forklifts are tested at near-maximum capacity for full lift height, speed and cosmetic defects. A final 'customer' check is performed randomly on 40% of shipped forklifts, where critical items are checked to ensure product integrity and delivery complaint issues, such as missing manuals or cosmetic blemishes are corrected. Domberg says that this final assurance process has reduced as-delivered field complaints to nearly zero.
Ongoing quality control - after-sales service Perramon believes that forklifts are "first sold by commercial ... then by service". Dirk Schulz, head of centralised customer service at Jungheinrich, says that there is a demonstrated need to enhance the core product beyond a mere industrial truck to the point where it essentially becomes a complete customer solution. Quality after-sales service is an essential part of that solution.
Schulz believes that customers expect prompt reaction times to issues, prompting Jungheinrich to offer full-service contracts. Jungheinrich's Information System for Stacker Management (ISM) provides customers with an online system that analyses master data, contracts, equipment features, operating costs, verification and optimisation of entire fleet use. ISM offers routine inspections and preventative maintenance, thereby reducing costly downtime. With over 3,800 service technicians, Schulz believes that Jungheinrich can offer extremely short reaction times, supported by state-of-the-art IT tools. Jungheinrich's new spare parts centre in Kaltenkirchen, Germany offers 24-hour delivery readiness, 365 days a year, guaranteeing 'in-night' delivery of spare parts within Europe. Schulz says that the next areas for spare parts logistics optimisation are China and Russia, while America is serviced through a partnership with MCFA.
Most after-sales service is provided by dealers or third-party fleet management services trained and supported by the manufacturer, but Todd Finney, technical service manager, finds that Cascade is moving closer to its end-user. He believes this is due to a combination of increasing technology and high turnover rates in technicians, along with an increase in the speed at which the market demands solutions. Finney says that Cascade's after-market parts department has a 90% fill rate within 24 hours on a standard product. Cascade also provides customers with live technical assistance and warranty, product and application support via a free-call number. Technical documents can be accessed via Cascade's website. Finney says that Cascade technical advisors travel whenever and wherever they are required.
Distance has always been an issue in maintaining high-quality after-sales service. Martinez agrees and says, "Of course, distance is a problem; more so nowadays as international business is the only way to go." Bomaq overcomes challenges of distance by offering free training via Skype to a customer's mechanics and a 'full-kit' maintenance for two years. Training can also be undertaken in-house. All spare parts can be ordered from Bomaq's dedicated website.
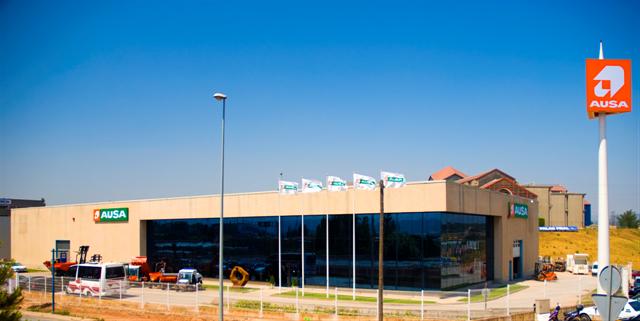 AUSA factory in Spain |
AUSA has machines working in exceptionally difficult and distant locations, including Angola and Mozambique. Perramon says that service to those areas is maintained by close partnerships with companies with a strong presence on the ground and through AUSA training, the AUSA website and a hot line service to AUSA engineers. Europe, America and Oceania are covered by master dealer partnerships in Germany, Ireland, the UK, Canada and Australia, which are located in large industrial parks with ready access to company stock warehouses - thereby decreasing freight costs and delivery lead times.
Birgitta van den Bosch, general manager - after-sales market, Mitsubishi Caterpillar Forklift Europe (MCFE), says, "Parts availability is one of the most important things for our dealers and customers, so it becomes our highest priority." Van den Bosch says that MCFE has 97% full line pick availability on approximately 500,000 spare parts. 'Direct distribution' means that dealers can order parts late in the afternoon and have them delivered by 7am the next day, either onsite, at a dealer site or at the mechanic's home address. MCFE has service teams in Europe, Africa and the Middle East trained by Cat Lift Trucks and kept up to date with MCFE's extended E-learning programs. Service technicians can also access trained staff at head office for advice on technical matters, warranties and spare parts. Van den Bosch says that because technology on its forklifts is constantly improving, MCFE can offer extended service level intervals and longer OEM warranties of up to five years.
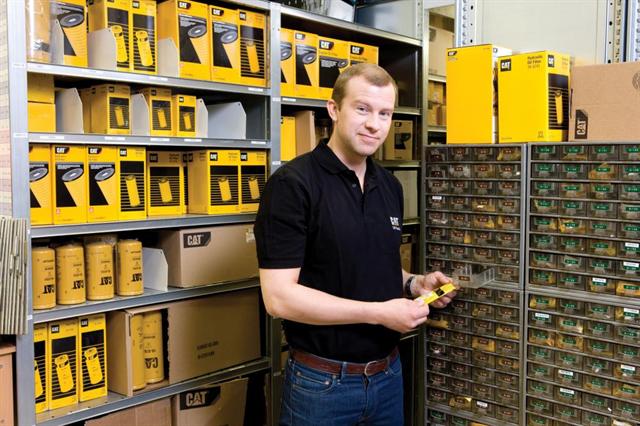 Caterpillar parts distribution |
UniCarriers also offers online as well as in-person training to service technicians. Domberg says that training should involve as much hands-on experience as possible to reinforce theory and manuals content. He believes that UniCarriers' service technicians' experience and technical knowledge on all its makes and brands, even those 20 years old or more, is a service advantage.
Managing consistent after-sales service can be difficult at times, particularly as Domberg points out, when there is a shortage of trained technicians. "One of our main issues is keeping dealer technicians adequately trained, given the shortage of technicians in our industry, the high turnover rate amongst younger technicians and the increasing diversity of technology and products being serviced."
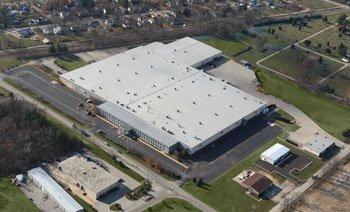 UniCarriers production facility |
UniCarriers is not the only company experiencing these problems; both UPLIFTING and Cascade relate similar problems. "To give better quality after-sales service we have two big problems, technical and human," says Aguarta.
Finney adds, "We balance the need of helping experienced workers embrace new technologies while allowing young technicians to be able to contribute experience, aptitude and attitude to contribute immediately."
It seems that while production quality and assurance in forklift manufacturers in most countries has evolved to a high standard, after-sales service as an intrinsic component in on-going quality may need more work. The lack of skilled technicians is a complaint that
Forkliftaction.com News has heard often over the years from the materials handling industry. Most likely it is just a matter of catch-up but firm and committed support from the industry towards training and service technician apprenticeships, would not it seems, go astray.
Additional information by our contributors:PROVIDING A QUALITY EXPERIENCE
UniCarriers Americas Corporation:
website,
ShopFront------------------------------------
JUNGHEINRICH: COMPLETE ICE TRUCK FLEET NOW MADE IN GERMANY
Jungheinrich AG:
website------------------------------------
UP LIFTING SA, TOTALLY COMMITTED TO QUALITY AND THE ENVIRONMENT
UP Lifting SA:
website------------------------------------
QUALITY BUILT IN WITH THE SUPPORT OF A GLOBAL PROFESSIONAL TEAM
Cat Lift Trucks:
website,
ShopFront------------------------------------
BOMAQ, THE NEW ROUGH-TERRAIN FORKLIFT THAT CAN HANDLE ALL YOUR JOBS
Bomaq Industries S.L.:
website ------------------------------------
CASCADE STANDS BY THEIR PRODUCTS WITH PERFORMANCE™ TWO-YEAR WARRANTY
Cascade Corporation:
website,
ShopFront------------------------------------
AUSA RT FORKLIFT TAKES THE LEAD
AUSA Center, S.L.U.:
websiteSince 2000, the Forkliftaction.com News team has been keeping business people informed with independent industry news, global and local stories, coverage of brand & dealer developments, end-user stories, new technologies and products, corporate moves, safety columns and market reports.
Catch up on past Forkliftaction.com News Special Feature articles here
For full access to our independent news and other business resources Subscribe to Forkliftaction.com News.