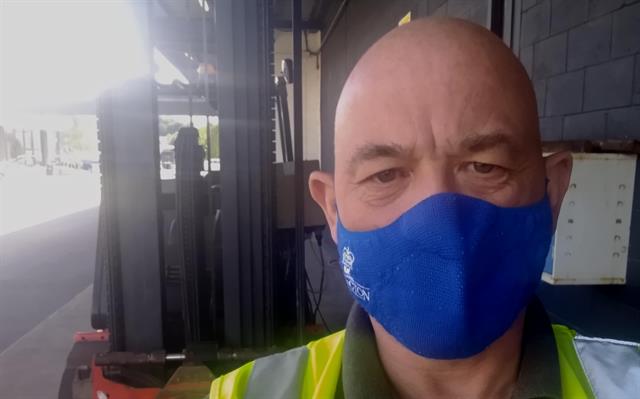 "The most rewarding aspect of being an instructor is passing on the skills and knowledge to help an individual progress in their career." |
It's been a 'long and winding aisle' for warehouse manager and forklift instructor Peter Faiers in Glasgow. He shares stories from his 35 years in the industry and provides some interesting insights into the changing landscape of safety training.
My journey into the weird and wonderful world of materials handling started back in the mid '80s, having secured a position as a warehouse operative within a large distribution centre. This was after having left the Army and training as a commercial diver. I received an introduction to the use of an LLOP (low-level order picker) that lasted about 90 minutes and then was let loose to pick stock.
A few months later, I was asked to operate a HLOP (high-level order picker) and the training was interesting, to say the least: "This is the on/off switch, forward and reverse, this is the steering (a very large ship's wheel almost), this is the height selector and away you go..." This was accompanied by lots of clanging as people attempted to negotiate the narrow aisle entry!
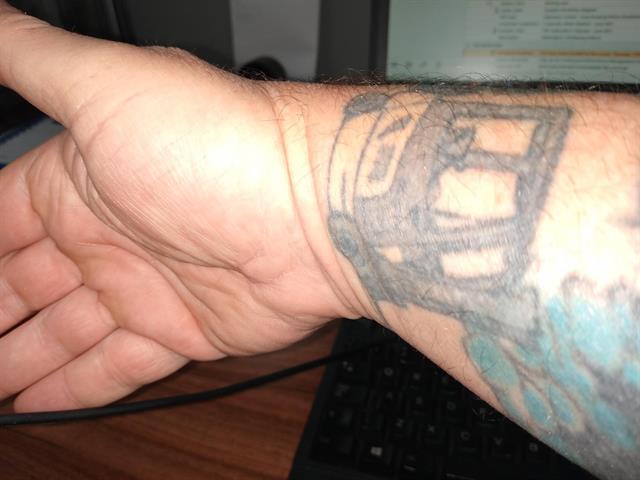 "Yes, I do have a forklift tattoo." |
It was to be almost 10 years (1995) before I attended a proper course and learned how to operate counterbalance and reach trucks. While doing the courses (and passing both by the narrowest for margins), I started thinking that maybe I could be an instructor. Unfortunately, at the time, finances and lack of a vehicle prevented me pursuing this option.
In 2005, I was working as a warehouse manager and the materials handling equipment fleet we operated consisted of five order pickers working up to 5 m. There were several instances where I had to request an external trainer who would take members of staff for five days and monopolise one of the order pickers, which was not ideal. I decided to bite the bullet and attended the course that allowed me to do all the training myself. With my new qualifications, I could train staff to use the counterbalance, reach and VNA (we were able to borrow the equipment from the landlord).
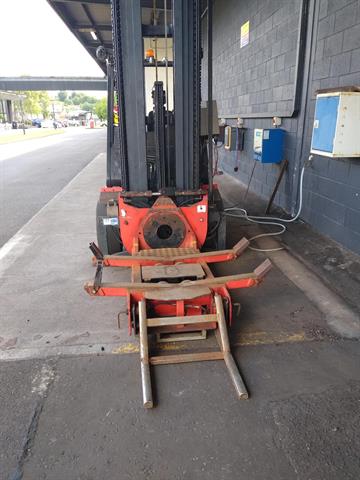 "One of the beasties we use in Edrington for handling casks of liquid gold." |
There were many benefits to taking the plunge: it thankfully reduced the turnover of staff because they gained a greater skill set. I enjoyed the staffing flexibility provided by staff being trained across several equipment types. It gave me the opportunity to cut training costs, and I liked knowing that staff couldn't say they were not taught something when they did something wrong.
My current role is mobile work equipment training coordinator and I have been at Edrington Distillery for almost 18 months (hopefully, my last role before I hang up my safety boots). The staff who operate equipment here are previously certified, so I am currently responsible for refresher training and ensuring everyone remains competent - as well as working with non-MHE colleagues to ensure they understand the dangers of being around forklifts, etc.
With the current pandemic situation, I am aware of the rise of e-learning and have been successful in creating an in-house package for the theory side, which means I can concentrate on the practical assessments when required. I am also trying to drag pre-shift checks into the 21st century and am working with IT to produce a company-wide application that will record safety checks and audits as well, so a slight move away from the traditional style of training.
I think the key to creating a solid safety culture starts from the top and ensuring that management understands the dangers associated with materials handling equipment operations, because not every manager/supervisor has operated a forklift.
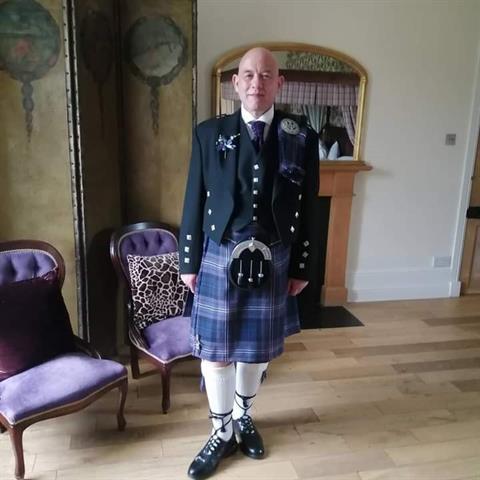 "Normal every day dress for an English Instructor living in Scotland (okay so it was my wedding last week...)." |
|
It also involves empowering individuals to be able to say something to anybody who is acting irresponsibly - without fear of retribution.
But most importantly, it is having a consistent and fair approach to safety in the workplace. Training and, with that, making sure the trainee understands and is not overwhelmed by everything, is the most important factor.
If you work with forklifts and materials handling products in any capacity, we'd love to hear your stories. Drop us a line or two or send us some photos here.