Kent O'Sullivan is a Certified Master Instructor Trainer with The Columbia Compliance Group. Columbia Compliance Group is a safety consulting firm that specialises in offering professional mobile equipment safety training programs & publications throughout North America.
Periodic refresher training is required by many regulations, codes and standards. It is essential for keeping safety skills sharp and preventing a dangerous sense of complacency. However, once you have said it all, how do you say it all again, year after year? If employees come to repeat training sessions with the attitude that they have heard it all before, how are you going to keep them from tuning out?
One of the best ways to start a repeat training class is with a pre-test to find out how much trainees remember from previous training sessions. That way you can quickly review what they already know, then concentrate on new information and material that may have slipped by them during their last training. Instead of the same old paper and pencil test, why not turn it into a competition? That gets everyone involved and paying attention. Divide the group into two teams and ask several questions about the training topic. While trainees are having fun playing the game, you can zero in on knowledge deficiencies that must be addressed during the session.
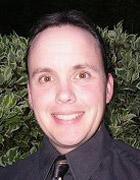 |
To make refresher training new, interesting and relevant, emphasise what has changed since the last training session. Are there any new policies, work rules or regulations that need to be discussed? Have new hazards been introduced into your facility? Have new work procedures been instituted or has new equipment been installed? Have new systems or processes been developed and deployed? Have there been any accidents related to the subject of your training?
Do not use the same training techniques every time. If you gave a lecture last time, try a video this time, or use a computer-based product, such as a PowerPoint presentation, to liven up the session. Bring some drama to repeat training with real-life accident or near-miss stories. Alternatively, do a demonstration. For example, demonstrate the effectiveness of a steel-toed shoe by dropping a weight on it. Seeing is believing and it enhances retention. Here are some other ideas to help make training fresh and new:
- Have trainees pair off and do an activity, such as going into work areas on a scavenger hunt to look for and record as many hazards as they can find.
- Bring in slides of different work areas, equipment, and operations related to your topic, and ask trainees to identify any hazards they see as the slides click by. Called "safety scanning", this technique encourages and trains employees to continuously look for hazards in their work areas.
- Bring in props that trainees can see and touch, such as a damaged tool that is unsafe, a hazardous chemical container that is missing a label, samples of PPE for inspection, or a piece of equipment for a demonstration.
- Invite a guest speaker- someone from outside the company with expertise in a particular area of safety, like a firefighter or a rep from your PPE supplier.
- Lead a discussion about safety problems, encouraging trainees to describe any problems they have had recently. Brainstorm with the group for solutions. Do not give trainees a chance to get bored in refresher training.
These tips are designed to get everyone involved in the training process. They will go a long way in creating a safe, hazard-free workplace.