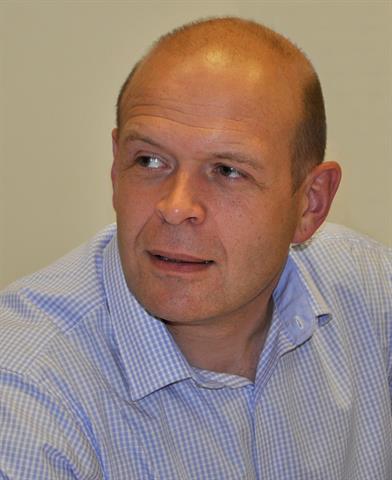 Stuart Taylor |
Stuart Taylor is Managing Director of Mentor FLT Training Limited, the UK's leading provider of training and associated services for all types of materials handling equipment and workplace transport.
Every business knows that time is money. But when an accident happens, everything stops. Not only is the safety of your most important asset - your team - compromised, but the productivity of your business as well, and it can cost you greatly. In the short term, dealing with the immediate effects can lead to operational delays, missed deliveries and unsatisfied customers. Then there's the resulting investigations, staff absences or cover, and repairs to think about.
But by focusing on a few key areas, you can greatly reduce the risk of forklift accidents and the downtime they can cause.
1. Train your operatorsProper training ensures that operators have the skills and knowledge to work safely and efficiently and understand the importance of doing so. It encourages them to be more proactive and to take ownership of the safety of themselves and their colleagues. Investing in your team in this way can also help them to feel safe and valued, impacting on staff retention rates and morale and, as a result, your overall productivity.
2. Maintain a safety cultureIn order to establish and maintain a safe working culture on site, the whole workforce must be considered. Risk assessments should be completed, followed by Safe Systems of Work (SSOW), which are then communicated to all parties to ensure everyone understands the risks and how to carry out their duties safely.
Forklift awareness courses ensure that everyone required to work around forklift trucks (whether operator or not) is aware of the hazards and consequences of unsafe operations, as well as the benefits of upholding safe working practices.
Remember, statistically, those most at risk of injury from forklift accidents are pedestrians, so it's vital that they understand the dangers. Ensure that everyone has a safe route around your site and that they follow it, with physical segregation between pedestrians and lift trucks in place wherever possible.
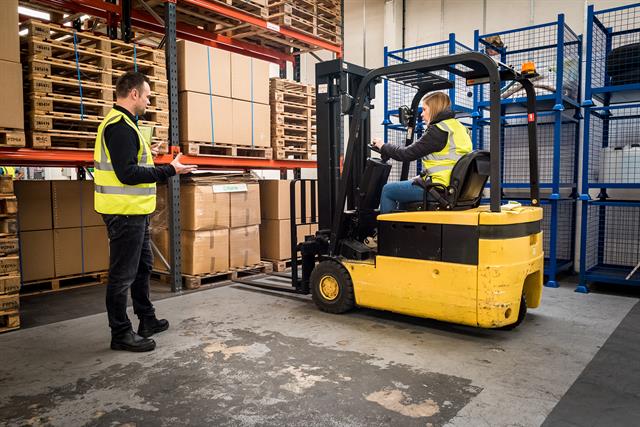 Monitor operations regularly |
3. Monitor operations regularlyRegularly monitoring operations will allow managers to assess how operators are working, correct behaviour where necessary, and minimise accident risk. By consistently overseeing operations, they can nip any unsafe practice in the bud before it becomes accepted as the norm and spreads throughout the workforce.
This relies on your managers and supervisors having a sound knowledge of the relevant hazards so that they know what to look out for. Should they need guidance, there are training courses available that are specifically designed for those managing operations, to help them understand and meet their responsibilities for safety.
4. Update your proceduresBusinesses are constantly adapting. As a result, operators may be tasked with using different equipment, carrying new types of loads, or navigating an updated site layout. When things change, it is important to make sure that you review processes and SSOW to ensure that they are still relevant, and update them if they are not. Remember: clear, communicated, monitored SSOW are key to ensuring that your safety message is not misinterpreted or ignored, so it's vital that they remain applicable.
Not only are these simple measures easy to implement, they are all cost-effective - many can be actioned internally and require only your time. So when weighed against the often serious and costly repercussions of accidents and resulting disruption, it's definitely worth taking steps now to protect your staff and your operational productivity going forward.