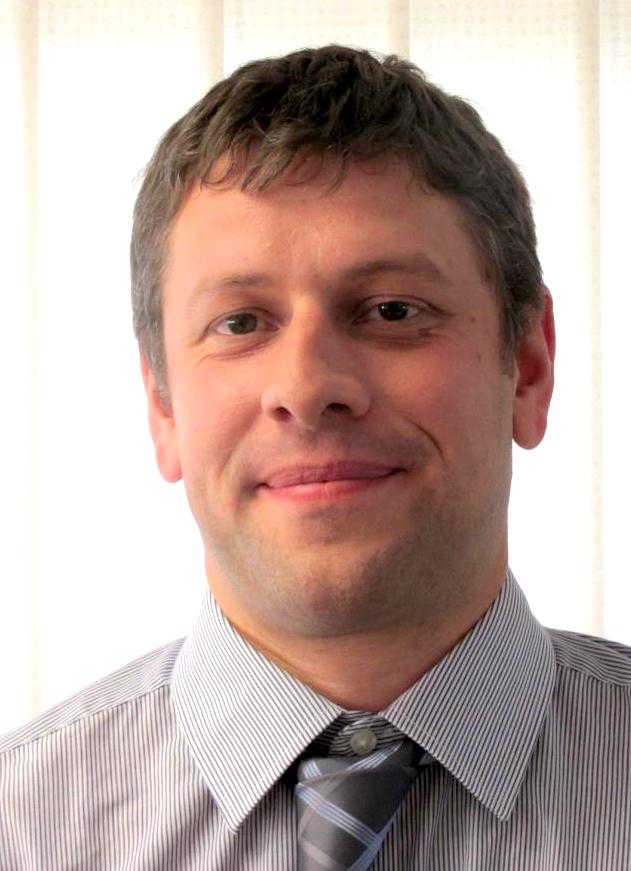 Ben Dobbs |
Ben Dobbs, Technical Manager at the Lifting Equipment Engineers Association (LEEA).
Lifting gear failure can have dramatic consequences for both those directly affected and those held responsible. To ensure safe practice, it is crucial that users are fully aware of issues surrounding Design Working Period and maintenance responsibilities, writes
Ben Dobbs.
The sad litany of in-service failure of cranes and other lifting gear has many causes, from criminal negligence downwards. One recurrent, and, to the uninitiated, rather baffling, theme is the failure of equipment that appears to be operating well within its 'safe working load' and 'design life'. Such incidents are seen both in ageing and in relatively new equipment, and suggest that those responsible for safe maintenance and operation do not always fully understand the 'life cycle' of the crane and its implications for safety.
To concentrate directors' minds, it is worth noting that recent crane-related fatalities have resulted in hefty fines, corporate failure, disbarment from being a director and, in some cases, jail sentences. Age-related failures are entirely avoidable provided everyone in the chain of responsibility performs their role and understands that, unlike their Victorian forebears, the modern finely engineered crane does not necessarily last forever - you have to look after them.
Part of the problem may be that the simple concepts of 'design life' and 'safe working load' are not really valid in modern practice. The whole approach to the design of cranes has changed in relatively recent times.
Greater understanding, combined with the ability of Computer Aided Engineering to enable a less conservative evaluation of stress and strain calculation, has enabled engineers to design close to the 'limit state', not just in terms of static loads but in terms of cyclical or fatigue loading, and in the effects of wear and tear. That has yielded great benefits in terms of initial cost and ease of transport and assembly, and indeed the giant tower cranes seen on construction sites would not have been possible under the old design approach.
However, this also means that cranes are designed, and classified, for particular patterns of duty. Structures are designed for a lifetime measured not in calendar years but in working cycles (and mechanisms similarly for a life in running hours). Working cycles are related to the load spectrum - the average load handled by comparison with the nominal rated load.
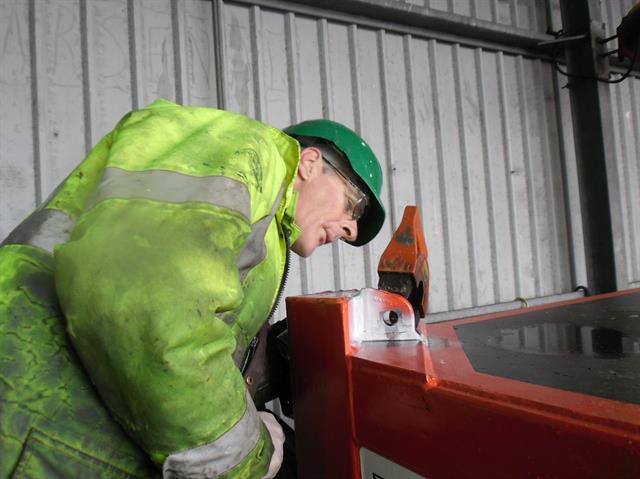 Where does the responsibility lie? |
So, for example, a crane rated at 10 T and intended to perform occasional maintenance tasks will be designed differently, and have different vulnerabilities, than a 10 T crane intended for continual use on a production line. If the inspection, maintenance and use of the crane takes due account of what is now a quite complicated specification - not a 'design life' but a 'Design Working Period' (DWP) - all should be well, but there is little margin for error.
This does not just apply to structures. There are similar considerations around motors, brakes, wire ropes and other elements. Various components and assemblies may have DWPs, which are not the same as that of the crane as a whole.
It is easy to see how things can go wrong. The intended usage may have been inadequately defined when it was bought or hired; usage may change, perhaps because production increases; it may be used for purposes it wasn't intended for. It becomes very important to maintain a history of usage and to relate that to the design parameters: that may not be easy; for example, with a hired crane, or when a new owner takes over a site or factory with cranes already installed. It isn't enough to depend on the periodic inspections and examinations specified under
LOLER (Lifting Operations and Lifting Equipment Regulations) as incipient failure, whether in structural members or, for example, in wire rope cores may not be readily visible.
BS ISO 12482 describes a method of monitoring the actual duty of bridge and gantry cranes relating it to the original duty envisaged in the classification. That then enables the prediction of when design limits are being approached and, in turn, the timely targeting of special inspections, maintenance and refurbishment. The philosophy of BS ISO 12482 should apply to all cranes.
The duty holderWhere does the responsibility lie? In the first instance, of course, with the 'duty holder', but there are many other parties that also carry responsibility. Nor does appointing a duty holder let the company's owners and directors off the hook. Safety inevitably carries commercial costs, although nothing like the costs of a fatal accident. Even minor injury or near misses can also be expensive, depending on the extent of the negligence. The company owners are responsible for ensuring that the financial and other resources, and the 'corporate culture' required for safe operation are in place.
Formally, the duty holder's responsibilities include:
- Ensuring that cranes brought in (bought or hired) are fit for purpose.
- Creating a risk assessment using manufacturer's data, environmental details, and usage information to identify critical or vulnerable components and determine maintenance and inspection intervals.
- Ensuring that cranes are maintained, inspected and thoroughly examined to ensure they are safe to use.
- Ensuring that they are not unduly susceptible to foreseeable failure modes.
- Keeping records of crane use, maintenance, inspections, repairs, modifications, exceptional events and so on, so that the history of the crane and thus its remaining safe life can be determined. The duty holder also has to keep and supply information required so that anyone modifying or upgrading the crane can calculate a revised DWP.
- Ensuring that cranes are overhauled or replaced before they reach their DWP.
Unless the company is actually a crane specialist itself, the duty holder will probably not have the required level of knowledge to carry out all of the above adequately and so will delegate to Persons competent for the required task. But the duty holder is responsible for ensuring that the necessary level of competence is possessed.
It shouldn't really need stating, but the duty holder is of course responsible for ensuring that any remedial actions that are flagged up - whether they be special inspections, parts replacements, changes in usage - are fully and promptly acted upon.
Examiners, inspectors and maintenance staffThe 'thorough examination' by a 'competent person' is carried out in accordance with statutory requirements. Routine inspections of critical features may be carried out in-house, perhaps by maintenance staff, to a frequency determined by risk assessment - which they may have been responsible for creating.
In accordance with statutory requirements, a competent person will take into account the age of the crane using actual or estimated information on the DWP expended to decide what actions to take or recommend, from deeper inspections to partial or complete disassembly, or precautionary replacement of parts. But the duty holder needs to realise that, unless specifically contracted for, the competent person isn't responsible for assessing how much of the DWP the crane or its components have remaining. Obviously, records of inspections, actions and recommendations need to be kept and passed back to the duty holder. Planned and preventative maintenance may reset the DWP clock for particular components or assemblies.
Manufacturers, modifiers and resellersSuppliers have the responsibility of providing all the information necessary for classification and assessing DWP. Modifiers are responsible for assessing and informing the duty holder of the remaining DWP.
ProcurementLogically, purchasing should come at the head of the list. Those bringing in - whether buying, hiring, or letting a contract for crane services - have a responsibility for ensuring that the specifications they issue, and the bids they accept, properly reflect the likely usage of the crane, and that it will be able to perform safely under all foreseeable conditions of use, for the specified classification of crane duty, as determined by risk assessment. They must ensure that equipment meets, and is marked and documented for, all relevant safety requirements and standards.
They also bear responsibility for ensuring the safety of bought-in spares and replacement parts, the competence of any contract maintenance or service firms, of contracted examiners, of trainers and so on.
It is particularly important that procurement is not exposed to undue financial pressures that might lead to the acquisition of equipment underspecified or unsuited to the task. This is ultimately the responsibility of the company's owners and directors to ensure.
Finally, it is always worth remembering with these issues the importance of seeking out a LEEA member. Members are fully audited and trained to ensure they offer excellence and compliance to standards and legislation.