By Fumitaka Otsubo
President, TCM Manufacturing USA, Inc.Since 1989,
TCM has been building lift truck products in a modern 165,000 square foot facility in Columbia, South Carolina. With the help of a dedicated workforce, our factory has met the demand in the United States for reliable, powerful, and productive
TCM lift trucks.
To meet increasing demand for our products and to attain our objective of delivering maximum value to our customers,
TCM Corporation is in the process of upgrading our factory with a 3 year $2.5 million renovation project to increase output, raise quality, and improve worker safety.
Our Engineering, Plant Management, and Materials Handling staff members started our rebuilding program by thoroughly evaluating our physical facilities and our manufacturing processes. They then studied the most cost-effective ways to improve them and located the best vendors and equipment to use for the project. After the upgrades were designed and the rebuilding schedule was finalized, vendor contracts were signed, our new equipment was delivered, production was suspended, and construction began.
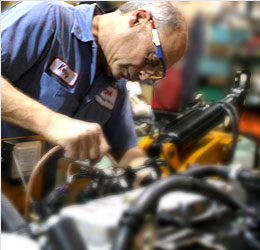 |
The first order of business was to upgrade the lighting system throughout the entire plant to enhance worker safety and product quality. In addition to enhancing lighting levels, significant energy savings were realized as well. In the assembly area, we upgraded the assembly line with an automatic vehicle staging process and also increased the assembly line length to allow for future expansion. This equipment has improved the consistency of our production speeds, and allows our employees to focus exclusively on assembly processes and quality. To support our increased production speeds, we installed additional parts manufacturing equipment including a new plasma burn system and new forming machinery. The equipment increases parts production capacity while improving quality.
All of the new equipment required precise positioning, installation, and setup. Our own
TCM Plant Maintenance staff accomplished this on schedule with assistance from our equipment vendors and outside contractors. Our project started on June 24 with the installation of the automatic towline and plant lighting, and was finished when the new forming machinery was installed on August 25. The construction has been accomplished with minimal disruption to our production schedule and output. Our factory rebuild has not required construction of any additional buildings, but will result in a production volume increase of approximately 66% over the 3 year project. We have improved our efficiency, improved our quality, reduced our costs, and equally important, improved our employees' safety and working conditions.
These advancements will help
TCM compete in our marketplace with even better products at more attractive prices. We at
TMU look forward to building our lift truck products as well as a strong future for
TCM.
Website TCM Distribution USA, Inc.: www.tcmusa.com
ShopFront TCM Distribution USA, Inc.: Click here