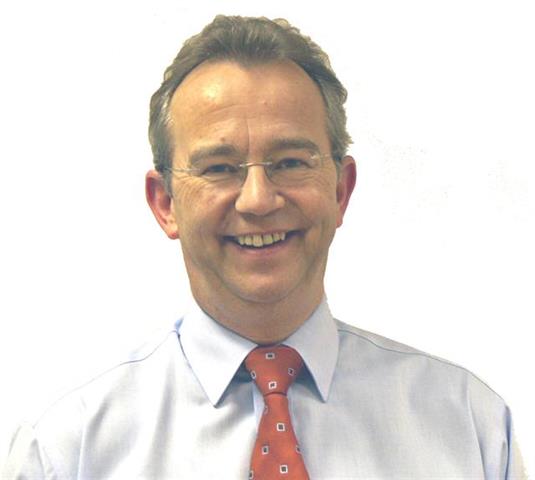 Richard Shore |
Richard Shore is managing director of Mentor FLT Training Limited, the UK's leading provider of training and associated services for all types of materials handling equipment and workplace transport.
Recent years have seen a decided shift by all industry sectors towards outsourcing of services such as forklift operator training to specialist external providers - a move that I warmly applaud, for perhaps obvious reasons. The main reasons for the move have been:
* Flexibility - getting training for employees when and where it best suits the business needs;
* Management - it is usually easier to manage external providers than internal staff, particularly if the management knowledge of what is required for compliance is vague;
* Quality - accredited external training companies have to comply with the standards of their professional bodies that are regularly checked to ensure the maintenance of standards;
* Availability - this is particularly relevant to businesses with multiple sites that may require training services at different locations at the same time;
* Reassurance - that the external provider is up to date with all the latest best practice and industry standards - a difficult task to achieve if it's not your core business;
* Cost - when all the costs of training are considered, including personnel, management and administration, then in the vast majority of cases, the cost of outsourcing is lower. (I have been through this exercise more than once with venture capital owners of companies and if you can prove it to them, then believe me, it's true)
In-house solutions There remain, however, certain instances where it may be more cost-efficient for a business to employ its own in-house instructors. By and large, this applies to large companies operating from large sites where the number and turnover of staff mean an almost constant and regular requirement for operator training to be carried out. While cases will vary depending upon a number of factors, my own yardstick is that sites with more than 100 operators (typically the large distribution sheds) can make a valid and viable cost case for training and employing their own instructors.
Managing the costsCompanies taking this route need to be careful that while they can prove the cost case, there are other factors that they need to be wary of if they are to uphold the standards of training and operation they seek. I have often come across businesses where the same manager has been responsible for the operators and the instructor and frequently the temptation to take short cuts with training to save time (and therefore money) has meant inadequately trained operators, resulting in damage to goods, equipment and - in the worst cases - personnel. When this happens, the carefully crafted cost/benefit case clearly goes straight out of the window and the potential costs move into a completely different league.
So, how can this loophole be closed? One potential way is to train operators using in-house instructors but then supplement this by using qualified external examiners to test the operators before they are let loose on the warehouse or factory floor. Another route is to open the in-house instruction and administration of training to external auditing or verification. Recent discussions within the Accrediting Bodies Forum with encouragement from the HSE have been focused on the merits of this approach and how it can be achieved.
My own view is that the regular monitoring of in-house instructors is at least as important as it is for external training providers - companies taking this approach need to have the reassurance that what they're doing is right.