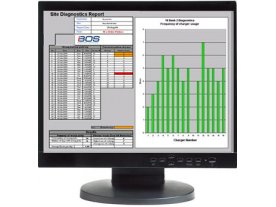 iBOS Pro provides enhanced analysis tools. |
The value of vehicle management systems (VMS) has been an ongoing discussion in the materials handling industry since they were first introduced over a decade ago in car and truck fleets.
End-users and management companies of large car and truck fleets were the first to use electronic devices in their vehicles as a means of monitoring vehicle performance and productivity. The process involves data being collected from the vehicle's onboard computer, transmitted to a central server, collated and then analysed for appropriate response by the fleet manager.
Most devices 'ride on top' of vehicles rather than being integrated into their design; however, there are a number of OEMs, including Caterpillar, Komatsu and Toyota, that now build management systems into the design of the forklift. This, however, can pose a number of problems for fleet managers using machines of different brands.
The information is sent wirelessly and analysis can be done anywhere in the world, as long as the operator has access to a computer and the internet.
There is almost no limit to the types of data collected, but the data can be grouped into two categories: machine maintenance and performance; and driver safety and accountability. Software companies often work with fleet and asset management companies and end-users to develop software to track data across a broad range of requirements.
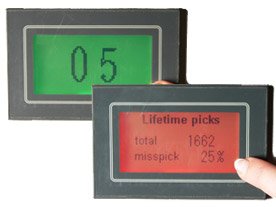 The iBOS basic system fits all types of chargers. |
The data collected for maintenance and performance can provide day-to-day information on hours, load work, parts wear and engine temperature, as well as suggesting an optimal service date based on actual hours worked rather than a calendar date and pre-emptive repair information.
Current offerings include the iBos system by Philadelphia Scientific, a USA company which develops management systems for batteries. This system tracks battery usage and charging and advises the user which battery to take next from the battery room. This reduces time spent by the driver in searching and increases battery life by ensuring that all batteries are fully charged and evenly used.
Safety features for drivers are diverse. The most common are personalised driver identification systems where each driver is issued with a keycard which mobilises the machine's engine and holds their personal information such as level of driving experience and training.
Other safety features can include remote engine stop, remote braking and hazard recognition. Davis Derby, a UK-based software company, recently provided software to GlaxoSmithKline's Gloucestershire manufacturing plant forklift fleet to record potholes and other areas of rough terrain around the facility.
The collected data has noticeably improved safety and work conditions by alerting drivers to existing hazards and reducing the amount of driver back injuries and wear to the vehicle.
Driver management systems can also provide geotracking, monitoring a vehicle's location and limiting its access to certain areas, as well as alerting fleet managers to vehicle abuse, impact detection, and the number of hours the machine is actually in use.
Fleet and asset management systems aim to improve efficiency and productivity as well as workplace health and safety. As Koen van Grimbergen, general manager of fleet management software developer Sofico, says, "Effective fleet management solutions provide the ability to reduce costs by allowing a business to utilise assets more efficiently. That way they're working on the cost end of the equation rather than the margin end."
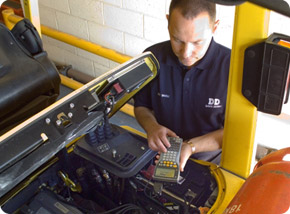 Davis Derby's TruckLOG system in use. |
So it is surprising to hear that that the materials handling industry was initially slow to take up the new technology. According to Shane Curran, a specialist business consultant for Sofico, the sector is five to 10 years behind car and truck fleet management. This, he believes, is due to a number of reasons, such as a smaller market, the difficulty in configuring existing software to a forklift fleet's specific needs and the differences between car fleet assets and forklift assets.
Despite an initial reluctance, fleet management system developers and operators have reported a significant increase in the use of these management systems over the past two to three years among materials handling fleets, particularly in Europe.
This trend was evident before the current economic downturn and the need for a more efficient and productive fleet is now of the highest priority to most fleet managers. In addition, software developers advise that no fleet is too large or too small to benefit from a vehicle management system. However, whether it becomes a valuable tool to the operator depends very much on what data is collected, how it is managed and how it is subsequently acted on.
For equipment managers to get the most out of their fleet management systems, they should ensure that they:
Set clear objectives and define what you want to know from your data;
Choose the right method to get the data and make sure the software is user-friendly;
Analyse the reports, then respond accordingly and in a timely manner;
Check that the installation and support details in the units give you the best deal for your needs;
Manage operators as well as equipment.