KOOI-REACHFORKS® "the standard" for hydraulic telescopic forks
Improve efficiency and safety"Save time, space and money", this original slogan from Meijer Handling Solutions since decades. Always companies scrambling to find new ways to cut costs in order to remain competitive. The expense of hiring external experts for analysis or the implementation of automation systems are simply expensive but most companies can use simple and inexpensive solutions which will create positive influence on their bottom line earnings.
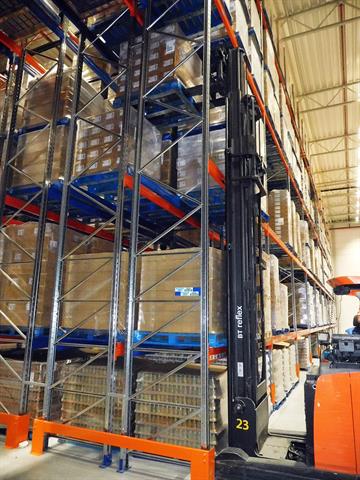 Double-deep |
In many circumstances, the simple solutions are often overlooked. Meijer Handling Solutions is proud to offer some cost effective solutions for helping companies reduce their operational costs.
Something as simple as changing the forks on your lift trucks from standard forks to
hydraulic telescopic KOOI-REACHFORKS® can help you speed up
(un)loading time, cut internal transport costs in half, improve space utilization and reduce damages to both goods and pallets.
Forty years of experienceMeijer Handling Solutions B.V. is based in the North of The Netherlands. This 4th generation family business has grown to become the world's largest manufacturer of telescopic lift truck forks which are sold under several trade names but the most well-known trade name is
KOOI-REACHFORKS®. Meijer Handling Solutions B.V. is the original inventor of the hydraulic extendable forks, and with almost 40 years of experiences and thousands of satisfied customers, the KOOI
®-FORKS have become "the standard" for most forklift manufacturers. Also more and more attachment manufactures decide to make use of the KOOI
® forks (instead of own manufacturing) because of specialization in deep-boor drilling technology and the experience provided by its sister company, Meijer Metal (a specialist in laser cutting and bending), Meijer offers the highest quality products available.
One sided loading/unloading saves valuable time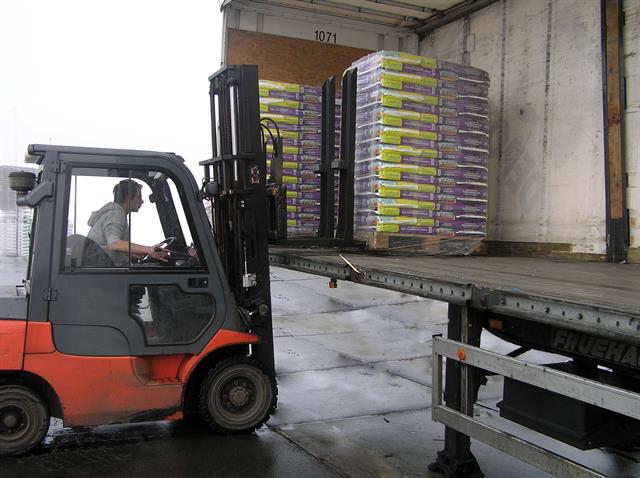 One-side (un)loading |
Many companies still load and unload trucks from both sides. The lift truck driver has to drive around the truck repeatedly. By using telescopic forks it is possible to load and unload pallets from one side. This not only saves 25% in time, it is also much safer because the lift truck is always at one side of the truck. This creates more space which can be used for extra storage. Because of the extra space trucks can sometimes even be (un)loaded indoors.
Dual load transport can help cut costs by halfMany companies have lift truck operators transporting single pallets back and forth all day long. The simple addition of telescopic forks can allow two pallets to be carried at one time instead of just one. Not only does this reduce internal handling by 50% it also lowers fuel consumption and maintenance costs since the forklift is only making half the trips as before.
Double-deep stacking leads to 30% extra storage volumeStacking pallets
double deep with hydraulic lift truck forks has become an easy way to increase storage density and maximize space utilization. By stacking pallets double deep, four pallets can be stored between each aisle which offers 30% extra storage volume. This can help companies avoid offsite storage or building expansion costs as it allows them to utilize the full potential of their facility.
Reduce damage to pallets and goodsAnother example of more efficient handling can be achieved when telescopic forks are used as
hydraulic extensions. A lot of companies are unaware of the fact that lift truck forks that are too long often damage the goods. Research points out that this is an important issue, but, despite the detection, it seems an underestimated problem and those damages treated as hidden costs. For example when different sized pallets are used, goods and pallets can be damaged very easily. The lift truck driver is always in a hurry and therefore he will always drive the forks completely in a pallet without thinking about the size of the pallet. When using smaller pallets, forks will stick out at the back of the pallets and will damage the goods that are behind it, with the result of all kind of extra costs. With
hydraulic extendable forks these damages are prevented.
Only an occasional need for handling variable load lengths?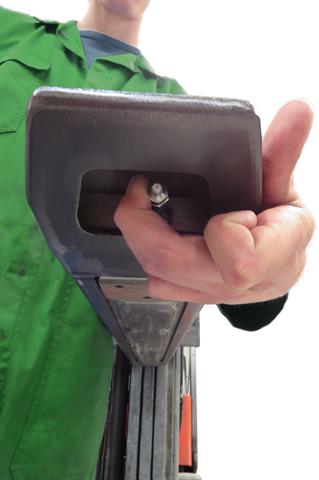 MME |
If you only have an occasional need for handling variable load lengths,
manual extension forks provide an ideal solution. They don't require hydraulics and they offer a lower investment cost so they provide a nice option for companies with budget constraints. The operator simply releases a fingertip locking lever at the end of the fork and slides them into position where they lock into place. They are always available when needed and no heavy lifting is required. They help keep your employees productive and safe. The unique
extendable sleeves offers some important USP's:
- Closed locking slots protect the locking pin.
- No loose parts needed to lock the sleeves.
- Extension in just one simple movement by moving a pin.
- Eliminate safety risks and inconveniences typically associated with loose fork extensions (outer sleeves).
From design to safe usageMeijer Handling Solutions (MHS) invests a lot of its turnover in development and improvement of new and existing products. Safety is an important factor at MHS and partly because of this, the KOOI telescopic forks are prescribed by all main leading lift truck manufacturers.
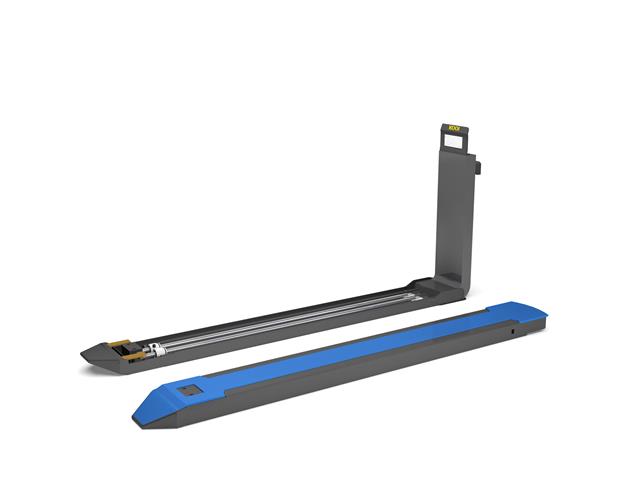 Open Fork |
With a constant focus on improvements it was MHS who developed the special outerforks. The design has been achieved thanks to specific expertise at the sister company Meijer Metal in the field of laser cutting and sheet metal work, and higher quality demands placed on the inner fork. The final result provides several significant benefits:
- The outer sleeve can be assembled with a reduced tolerance gap. This means that the sleeve bends less when fully extended.
- This wear zone is made up of a 6 mm thick plate that is robot-welded into the sleeve. This wear strip is made of wear-resistant steel (400HB) that has been specially developed for heavy-duty applications, e.g. in the construction (cement mixers, shovels, dumpers, etc.), agricultural (ploughs, conveyors, etc.) and mining industries.
- An ingenious combination of laser cutting and sheet metal work construction ensures that sleeves do not catch when withdrawing from pallets. The sleeves corners are fully rounded off along all edges.
- The sleeve is folded all round which gives the sleeve tremendous rigidity and ensures that static and dynamic loads are evenly distributed throughout the entire profile and not weakened by any welds.
High-quality standardsAll KOOI-FORKS's telescopic forks are produced according to the specific ISO standard 13284. This international safety standard specifies that all forks need to be tested and approved with a safety of 3 just like ordinarily standard lift truck forks. This means that when the nominal capacity is 1000 kg for example, the telescopic forks needs to carry 3000 kg without a permanently deflection. The telescopic forks are always tested as a pair and will leave the factory after all kind of intensively tests and quality procedures.
Third parties are testing KOOI-FORKS's telescopic forks to a dynamic duration test of 1 million cycles with an overload of 25%. This extreme safety test is done including all their drillings, like oil channels and cylinder holes. This test shows that KOOI-REACHFORKS
® can safely be used just like standard long forks. Considering that the forces in the materials are the same for both, standard forks and hydraulic forks, the safety regulations ISO 2330 for standard forks should also be the same for telescopic forks.
Within a few weeks MHS will have 11 deep-drilling machines and can continue to grow as a world market leader. The number of
KOOI-REACHFORKS® is still growing year by year, and Meijer Handling Solutions has decided to build a complete, new production facility which has been finalized last year to attain the optimum layout for its production.
For more information please contact:
Meijer Handling Solutions
Tel: +31 (0) 518 49 29 92
www.Meijer-Handling-Solutions.com
Send an email