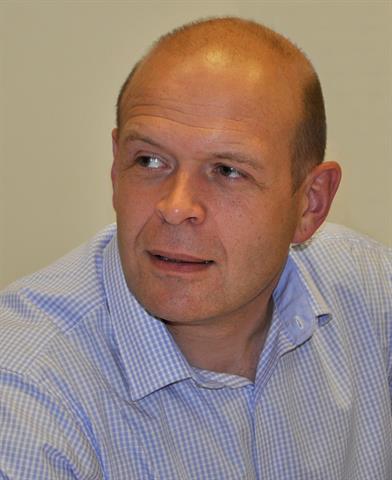 Stuart Taylor |
Stuart Taylor is Managing Director of Mentor FLT Training Limited, the UK's leading provider of training and associated services for all types of materials handling equipment and workplace transport.
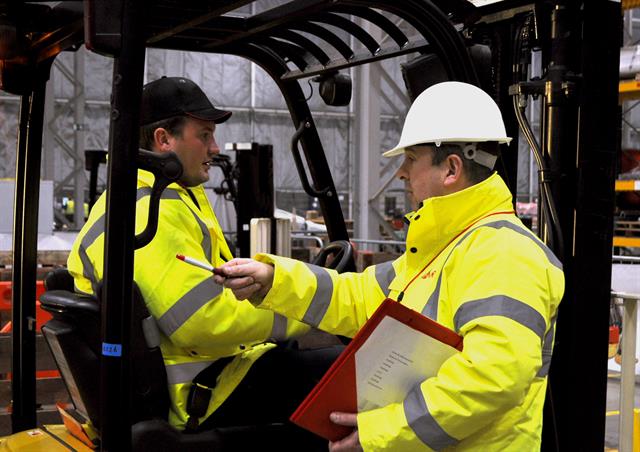 Most companies have recognised the need for operator training and fulfill their basic obligations. |
'What can we do to improve site safety?' is the kind of question we're often asked. Though the specifics vary from site to site, each with its own unique hazards and risks, we have definitely been able to identify some clear themes over 27 years in business.
Obviously, there's no magic formula but, at its simplest, there are three key areas on which the most safety-savvy businesses tend to focus in order to actively promote and maintain a safe working environment: traffic routes/segregation, training and engagement.
And for good reason. Get this holistic trinity right and you can anticipate a significant - and lasting - improvement in safety on any site.
Let's start by being clear on who are the real victims. It's people on foot. Pedestrians account for 60% of the many hundreds of forklift-related accidents each year and that almost invariably means serious and life-changing injuries (there's only ever one outcome when humans come into contact with several tonnes of steel).
Regrettably, the number of these accidents remains stubbornly - and depressingly - high with forklifts responsible for the great majority of workplace traffic accidents. Damningly, during a 10-year period when road traffic accidents fell by 46%, forklift accidents came down by just 10%.
We can do better. We must do better. Doing so need not be costly and, what's more, improvements to the safety regime are almost certain to reduce operating costs and enhance any company's bottom line.
Let's look at those three key areas:
Traffic Routes and SegregationCreating a clear, physical separation between employees on foot and forklifts may sound obvious, but in an online Hazard Perception Test, developed by Mentor in association with the Fork Lift Truck Association, only 50% of managers and supervisors recognised the dangers. In many ways, that comes as no surprise.
From our own experience of running Managing Forklift Operations courses, it emerges that less than 50% of attendees have ever operated a truck. Worse still, 90% simply aren't aware of their legal responsibilities or the real consequences of an accident.
TrainingMost companies have recognised the need for operator training and fulfill their basic obligations. However, not all take account of human nature and the need for constant monitoring.
Operating a forklift is a skilled job, one that involves a high level of repetition. Unfortunately, performing the same task many hundreds of times a day can easily lead to complacency and bad practice. Why? Because people calculate risk based on what has (or hasn't) happened previously, even when they know they shouldn't. Because "nothing bad happened when I did that before", people relax and their performance levels plummet. As road users, how many of us can claim to be blame-free? The difference is that on the highway we are held to account - by cameras, the police... but especially by our peers.
It makes sense, therefore, for every single employee on site to receive a short, sharp and thought-provoking training course of the dangers posed by forklifts - and how to avoid them. It both informs the unaware and refocuses the experienced who have fallen into bad habits.
EngagementAs mentioned a little earlier, peer group pressure is immensely powerful, so one of the most important steps to reducing accidents is creating a positive safety culture - a shared belief about risk, hazards and accidents. The aim: to establish a self-policing environment where bad practice is simply not tolerated by the community (like smoking in a restaurant).
It starts with buy-in from the top. Senior management must recognise the benefits and have the commitment to demonstrate that the safety culture is genuine - and involves everyone. Employees need to be engaged and involved in an open and meaningful way, not least because they are most likely to have the solutions to any challenges. By making them part of the process and the solution you will have their all-important buy-in.
Finally, sustain the commitment. Working safe and staying safe needs to be part of every shift, day to day, year upon year, to avoid the threat of complacency.