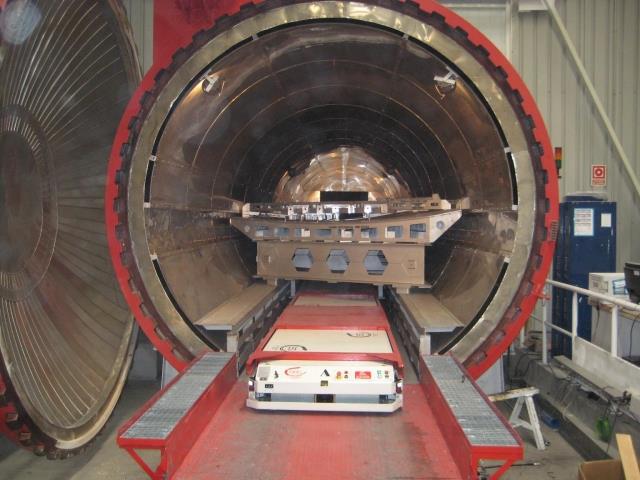 AGV designed for autoclave loading process. Click to view larger image. |
Often, we spend too much time and effort moving a product from place to place along the different production steps.
All these handling tasks imply costs which enlarge the total production cost, even though they do not improve the product value.
When producing complex goods, handling difficulties are increased and, with them, the costs.
It seems obvious that the solution would be to reduce the handling tasks by using suitable equipment that enhances or automates transport, saving time, worker effort and costs, and more importantly, minimising risk.
To achieve this,
ASTI has developed and installed for
Aries Estructuras Aeroespaciales (ARESA), part of the ACITURRI group, two
made-to-measure solutions that improve load handling, guaranteeing the safety of workers and facilities without losing the strict quality controls required for the aeronautics sector.
Nowadays, ACITURRI is one of the three first level suppliers (TIER 1) of aero structures for the main aeronautical constructors.
The production centre at Valladolid is specialised in producing composite material aero structures. Over recent years, this kind of material has progressively increased its presence in the aircraft fuselage, substituting metal such as titanium or aluminium, with the main aim of reducing weight and fuel consumption.
The use of pre-impregnated carbon fibre requires a very precise production process that goes through different stages and areas, such as a preparation area, thermoforming tables or autoclaves. Optimising this process has become one of the priorities for the industrialisation, production and engineering departments over the last year.
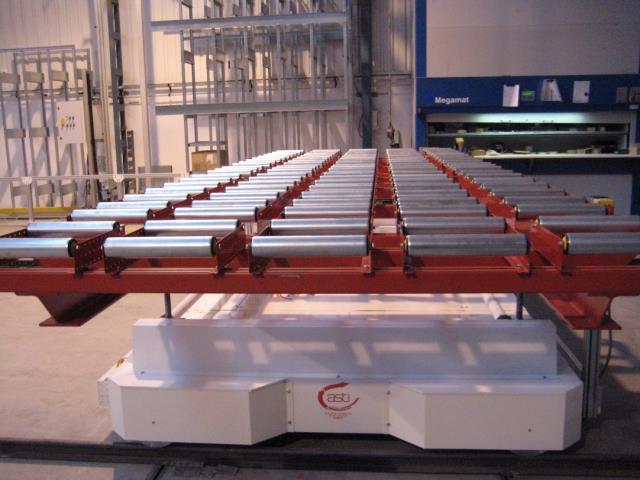 Custom built conveyor. Click to view larger image. |
For transporting materials between working and thermoforming tables,
ASTI has developed a
conveyor custom built for the company's needs.
This conveyor which is
6 meters long has a free roll table to enhance the material conveying. The rolls are distributed in five racks that leave free space for the loading or unloading of the product by a truck.
As the working thermoforming tables are at different heights, the conveyor includes an ascending/descending system in order to reach the same height and maintain the same level to prevent crashes and so to guarantee the piece integrity.
It is designed to be able to
transport loads up to 3,000kg.
The system is
simple to operate, avoiding the need for extensive training. The installed system makes it easier for workers to carry out their tasks as the
conveyor takes the materials to the worker, improving the work ergonomics as well as the process efficiency.
Meanwhile, the autoclave loading process requires utmost precision. To automate these movements,
ASTI has designed a very special
AGV (Automatic Guided Vehicle), able to fulfil all requirements set by the ARESA production process.
The solution is
11 meters long and allows the company to transport different tools among all the stations safely. The length of the line provided some challenges. For example, a very large turning circle would be required using normal wheels, so the
AGV uses multi-directional wheels able to turn 360º, which significantly reduces the necessary space and avoids load movements when manoeuvring.
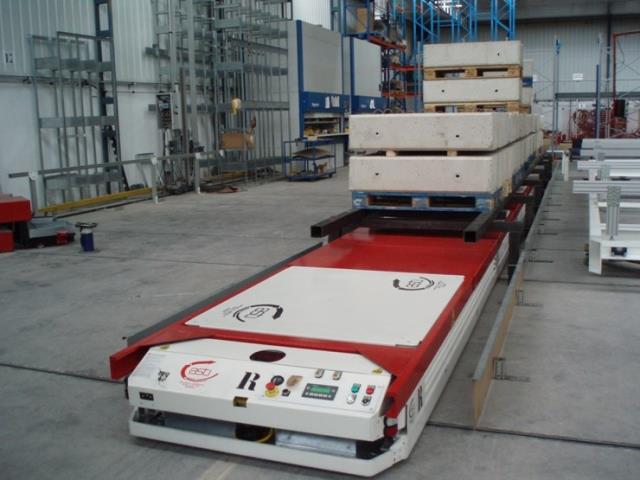 AGV multi-directional. Click to view larger image. |
Another unique aspect of this
AGV is its
triple guiding system that was necessary to guide the vehicle along a fixed route that crosses various different environments.
For the open area at the entrance to the autoclave, it uses a
magnetic band guiding system. This required the installation of a magnetic band on the ground and a guiding device installed in the AGV that detects the band and follows it.
This guiding system would not be appropriate inside the autoclave or when picking the tools, where higher precision is required. Because of this, a second guiding system more suited to narrow spaces was installed. The system consist of a scanner laser that sends a beam of light that bounces on the walls and thereby sends information about distance and angle that determine the vehicle location with high precision.
To guarantee even higher precision when entering the autoclave and when picking up tools, a third guiding system uses
laser pointers to laterally correct the position of the vehicle. The laser pointers determine the distance to the internal part of the tool or the autoclave, avoiding any collisions and guaranteeing perfect picking and depositing of material.
These three guiding systems work in combination and they automatically spring into action at specific route points or vehicle tasks.
The vehicle recognises these changes through an
RFID system that marks the different areas and the tasks to be followed at that determined areas. At the key points such as picking or depositing the tool and loading or unloading the autoclave, a pre-programmed tag is buried with all the information about actions to be carried out, that the AGV will read to be able to carry out the loading and unloading cycles automatically. These markers also adjust the AGV's height, for example raising it to deposit loads on the stands installed at both sides of the autoclave. In the same way, it will get lowered after detecting the exit tag.
Like other
ASTI AGVs, the system
can also be usual manually which is useful for movements outside the fixed route. For its use in manual operations, it has a remote control to direct the vehicle along all its different working modes. A display lets the user know under which mode the vehicle is working at any time.
In order to guarantee the safe coexistence of the AGV with facilities and workers, it has
various safety systems. For example, apart of guiding the vehicle, the lasers can detect any obstacles in its way, slowing down to a complete stop if necessary. Distances are completely configurable according to the speed at which the vehicle is travelling. The laser pointers also avoid lateral collisions when detecting obstacles alongside.
The vehicle is equipped with warning signals - acoustic as well as beacon lights - and emergency stop buttons. In addition, there is another emergency stop button on the remote control to stop the vehicle without having to press any button on the AGV.
The vehicle has a
battery set that allows the AGV total movement autonomy. The on-board recharger allows it to be connected to the general power supply during the non-work periods, avoiding stops during work periods.
These two solutions have contributed to improving ARESA's production flows, improving its efficiency from various points of view. As the materials transport and conveying among stations has improved, there have been increases in productivity and significant ergonomic gains have been identified by ACITURRI. Meanwhile, transport is carried out automatically without direct human intervention, resulting in cost savings. And finally, these vehicles are especially designed to handle loads safely, avoiding crashes and damaging of the materials, reducing wastage.
These developments come from
ASTI, Automatismos y Sistemas de Transporte Interno S.A.U., an engineering studio from Burgos, Spain, that has been providing internal logistics solutions for companies from all kind of sectors for more than 25 years. This is only possible through its ability to develop turnkey projects and custom solutions which is totally adapted to the customer needs.
This project is the result of significant R&D carried out by this company which has set the development of new technologies as a key objective in its aim of sustainable growth.
For more information contact us:Email:
asti@asti.esPhone: +34 947 177 210
AUTOMATISMOS Y SISTEMAS DE TRANSPORTE INTERNO S.A.U.Web: www.asti.es
Blog: www.asti.es/blogAutovía A1 km 213,5 Polígono industrial
09390 Madrigalejo del Monte (Burgos)