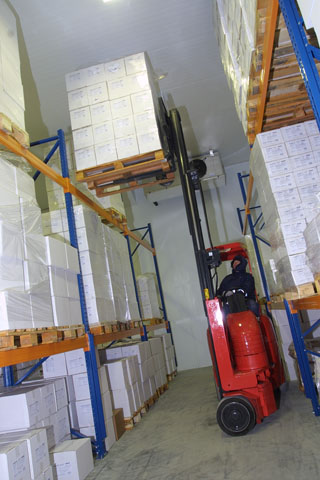 Narrow Aisle Flexi EURO |
Two different narrow-aisle solutions are proving invaluable for their buyers.
Car-maker Mercedes Benz has deployed Narrow Aisle Flexi's latest EURO compact four-wheel articulated forklift to streamline production in the Stuttgart factory that builds E-Class cars.
The factory manufactures and assembles car subcomponents for car doors. Suppliers deliver components to the production lines on a just-in-time basis and the car doors are individually produced in a range of colours and materials within a four-hour window.
The Flexi EURO is suited to the work flow because of its compact dimensions and its ability to work both inside - within the aisle ways - and outside to unload incoming deliveries of door components.
John Maguire, sales director of Narrow Aisle Flexi, says its client is using the articulated forklift to do the work that previously required both counterbalance and reach trucks. This has led to a significant reduction in forklift fleet operating costs.
The counterbalance machines unloaded the door components as they arrived and then the reach trucks would deliver the loads to the racking aisles.
"Thanks to the Flexi EURO's ability to work in aisles as narrow as 1,642mm wide (with a Euro pallet) or 1,762mm wide (with an ISO pallet), the company has been able to reconfigure its lineside buffer store," Maguire says.
"By significantly reducing the aisle widths between the pallet racking in the store from their original width of 3.8 metres (12 feet), the company has increased its pallet capacity dramatically, which means more components can be held on site."
The main difference between this machine and others in the Flexi range is its size, the Flexi EURO being smaller. It is ideally suited to low bay warehouses, where high lift performance is not a priority and space is at a premium.
The Flexi EURO can lift 1,500 kilograms (3,306 pounds) to heights of over seven metres (22 feet).
Maguire says the Flexi EURO is in demand in Germany after demonstrations at several trade fairs.
"It is creating a lot of interest in Germany and the feedback we have had has been overwhelmingly positive," he says.
Meanwhile, haulage and warehousing specialist Sheldon and Clayton Ltd has chosen Jungheinrich forklifts for its new factory to give it an edge over competitors.
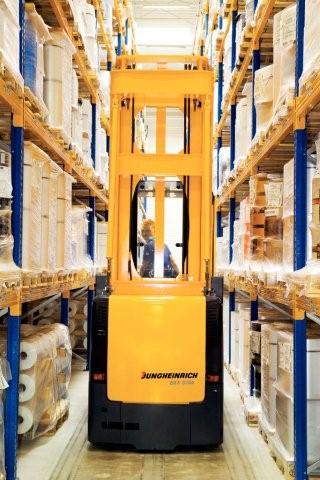 Kombi EKX |
The company has purchased Jungheinrich's electric-powered Kombi EKX range of very narrow-aisle stacker/order pickers. The machines will be used at Sheldon and Clayton's new GBP1.5 million (USD2.67 million) warehouse.
David Sheldon, managing director of Sheldon and Clayton, says Jungheinrich's forklifts offered the best value for money of all the trucks that the company evaluated.
"The Jungheinrich trucks offer a cost-effective, value-for-money solution that will give us an advantage over our competitors in what is an extremely competitive business," he explains.
Sheldon and Clayton operates double shifts at the West Bromwich factory, which means it requires trucks that can work two shifts without the need for a battery change.
The Kombi's third-generation AC motors are highly energy efficient with productivity further enhanced by the motor's high torque that gives high acceleration and greater throughputs.