Only forks make a truck a forklift truck. VETTER knows that and is focused on forks like almost no other company in the world. Being a world-wide leading manufacturer with 50 years of experience, VETTER offers a complete range of forks for all types, makes and sizes.
When it comes to
BIGForks up to 120 to capacity and beyond, the demands to forks are once more increased because of their mere dimensions and capacities. From raw material to heat treatment and logistics, the complete production process needs to be aligned with toughest application demands.
It all starts with the fork material Fork material is an essential factor for the whole product quality. Invisible at first view, the selected steel mainly affects lifetime and operation of a fork.
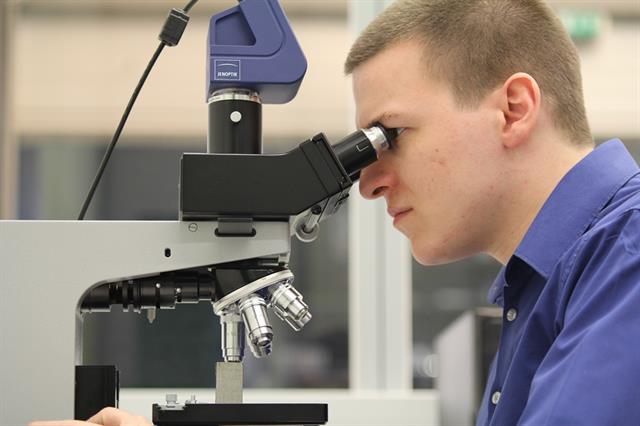 Unique, consistent material quality, approved by in-house material engineers. Click for larger view. |
VETTER BIGForks are manufactured from a very special Fork
Steel - decades-long developed and continuously optimized. Only certified steel suppliers, dedicated delivery specifications and frequent tests lead to a unique, consistent material quality. In-house material engineers and an own laboratory assure that only best steel is used. For high-demanding applications, even ultra-high strength steel providing a superior capacity can be offered.
All VETTER Fork
Steel offers wear-resistance, high yield strength, high dynamical resilience, best welding characteristics, titan-stabilization, superior purity grade and is optimized also for low temperatures. This makes the VETTER Fork
Steel one of the best in the market which bears the comparision with highest steel specifications.
Most sophisticated production line for BIGForks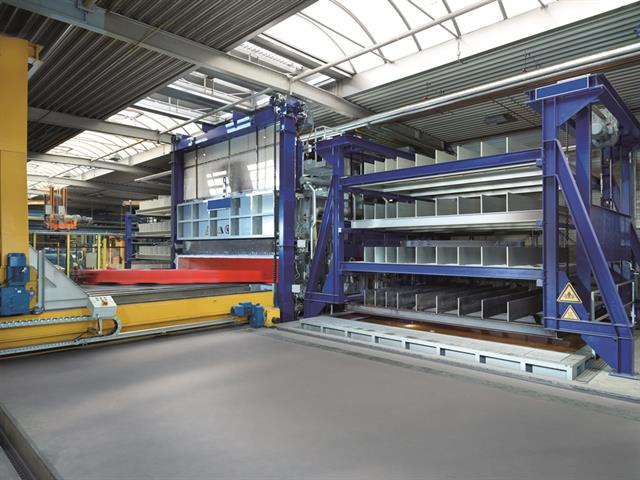 Fully-automised heat treatment facility. Click for larger view. |
In 2012, VETTER revolutionized the manufacturing process for
BIGForks. Having one of the most sophisticated production lines world-wide, VETTER decided for closed die forging as it is state-of-the-art for nearly all industrial high-quality parts. Benefits for the customer are obvious: Only closed die forging is able to offer tight tolerances, best reproducibility and an optimum material structure. Smooth surfaces never achieved before in the range of BIGForks offer best dynamical stability.
A further essential production step is heat treatment. The goal is to achieve the best combination of durability, wear-resistance and toughness of a fork. For optimum results,
VETTER installed a fully-automised heat treatment facility with precise temperature and time control. The computer-operated quenching and tempering facility enables exact reproducibility - a technology from the automotive and aviation industry for best product and material characteristics.
A comprehensive machinery park for mechanical processing, highest welding quality according to ISO 3834-2, highly-skilled and experienced personnel as well as a high vertical integration ensure optimum safety and flexibility.
Forks are controlled by a strong quality team and continuously approved on static and dynamical testing facilities. A standard safety factor "3" let customers feel safe and confident.
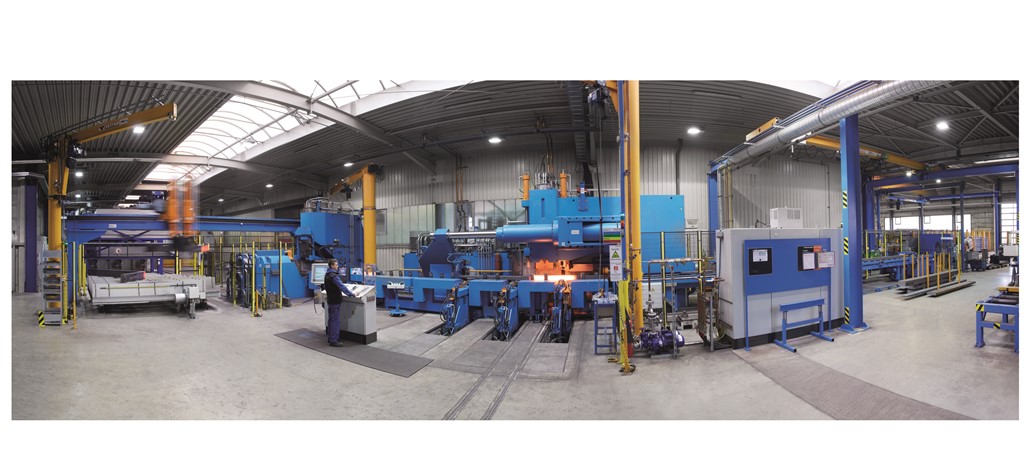 New, sophisticated production line of BIGForks. Click for larger view. |
|
The best fork is worthless without best serviceFor this reason
VETTER offers a wide range of benefits only a manufacturer can provide.
It starts with a high flexibility by a comprehensive stock of raw material and manufactured forks.
Best advice can be guaranteed by one of the most skilled fork engineering departments in the Industry. An extensive database of more than 28,000 living articles helps to find the best fork for each application. Various logistic and packaging options make life easier.
Finally, many satisfied OEM and dealer customers world-wide trust in
VETTER as responsible and fair partner.
Please contact:
VETTER Umformtechnik GmbH
Phone: +49 2736 4961-0
Email: Send an email
Website: www.forks.com
ShopFront: www.forkliftaction.com/cards/vetter
Carl-Benz-Straße 45
57299 Burbach / Germany