Bill Huettl is the operations manager for Conger Toyotalift, a materials handling dealership and service centre headquartered in Green Bay, Wisconsin.
Recently, we got to thinking: What are the most common complaints that prompt a service call? And what are the most common root causes of those complaints?
So, we decided to dig into our records. And by the time we finished, we had analysed 6,220 service calls from 2019.
Here are the most actionable steps, distilled from our analysis, that you can take, starting now, to reduce service calls, keep your equipment running well, and protect your bottom line.
1. Stop leaks before they startWhile leaks can happen from any of the fluid systems that exist within a forklift, we found hydraulic hoses to be the most common leak point. And while the bad news is that these leaks can't be completely prevented, the good news is that regular maintenance can reduce them.
It is important to understand the structure of a hydraulic hose in the first place, in order to understand when they are at risk of failing. Hydraulic hoses are coated in thick rubber, but underneath that rubber is a wire substructure. Because the pressure from hydraulic fluid can be as much as 2,300 PSI, that wire structure is necessary to cope with the extreme pressure. Problems arise when the rubber is cracked and the substructure becomes exposed.
That's why regularly checking hydraulic hoses for wear should be part of any operation's maintenance schedule. This is especially important for any hoses that move frequently during operation, such as free lift hoses. If the wire substructure in the hose can be seen or felt, the hose should be replaced immediately to prevent a costly (and messy) failure.
2. Don't neglect your batteriesFrom batteries without enough water to ones that would sputter out after only a few minutes in operation, we found battery problems to be a major reason for service calls. Overall, we saw battery issues manifest themselves through rough running complaints, no start calls, travel and lift problems and error codes.
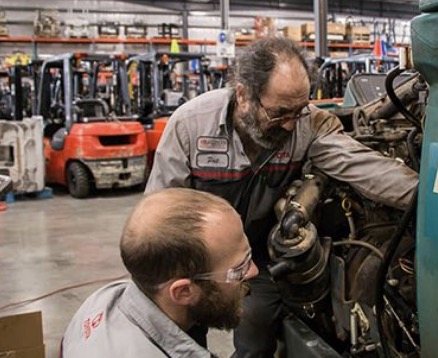 Make sure to schedule regular maintenance |
If properly maintained, the average industrial battery should last for five years. And considering that the cost of a new battery can run in excess of USD5,000, you'll want to make sure it is properly maintained at all times.
The problem with battery maintenance, though, is that it's time consuming, exposes workers to chemical hazards, and can be difficult to perform with certain types of trucks.
Sit-down riders, for instance, are easier to check than stand-up trucks like order pickers and reach trucks. That's because the battery can be accessed simply by lifting the hood of the former in many cases. Stand-ups, on the other hand, hold their batteries within compartments only accessible from the side. This means that the battery must actually be removed from the unit in order to perform simple maintenance, like checking the water level.
So, what's the solution? Try a battery watering system. These allow for batteries to be filled with water using a hose system, eliminating the need to actually remove the battery from the truck and individually water each cell. Not only can a watering system make it easier to fill the battery, it also cuts down on time and lessens the risk of chemical exposure.
3. Clean your fuel systemsSymptoms of fuel system problems include loss of power, sputtering and backfiring, not starting or running, and sometimes higher emission levels. The last symptom is especially worrisome, as it can directly interfere with the safe operation of a facility by potentially endangering employees and shutting down production.
But what goes wrong inside the fuel system that ends up causing these issues? The answer has a lot to do with the fact that liquid propane gas (LPG) is a dirty fuel. While it does in fact burn clean, the problem is actually the tank itself.
Propane tanks are vulnerable to oxidation, both inside and outside the tank. So, if your gas company doesn't regularly purge its tanks, the rust from the inside can be released with the fuel through the fuel line. Once inside the fuel system, the rust clogs up the regulator and fuel filter, compromising the machine's operation in the process.
That's why regularly cleaning the regulator and replacing the fuel filter is key to the continued proper operation of your forklift. So, make sure that such cleaning and replacement is included in your regular maintenance program.
4. Guard your accessoriesBy "accessories", we're primarily concerned with components like horns, travel alarms and lights.
More and more, we're seeing accessories like blue lights, red zone lights, and LED headlights becoming standard equipment. That's because they offer greater safety by improving visibility. But greater prevalence of these accessories means more things can go wrong. Of course, some components do wear over time, like light bulbs and horn contacts. But operator-caused damage is a major and ongoing cause of accessory failure.
How can you help reduce damage to your machine's accessories? The first step is to ask questions about your operation. Where will the equipment be used? Are there obstructions and damage points in the environment that are likely to cause continued problems? Typically, the most common causes of accessory destruction are racking, semi-trailers and dock equipment, and narrow doorways and low ceilings.
Once you've identified what areas in your facility are most likely to cause accessory damage, you can work towards prevention. That largely means mounting accessories inside the overhead guard or within the body of the machine. Because if the accessories aren't outside the machine, they're less likely to suffer impact damage.
5. Beware of built-up debrisDebris can compromise many systems in a forklift, including electronic and control systems (handles and levers) as well as the cooling system (especially the radiator). Even the movement of the machine itself can be affected. When substances like plastic and bale wiring wrap around the drive axle, movement can be arrested and damage to the brake components can follow.
Of course, debris affects some industries more than others. Operations that are especially vulnerable to debris-induced forklift problems include paper mills and recycling plants; manufacturers of plastic wrap and insulation; lumber and wood yards; machine shops and scrap yards; and plants that process organic materials like animal hides.
How can you help with the debris problem if you're in such an industry? Regular blowouts with compressed air are key. Do them once per shift, unless the operation requires more frequent action. And make sure to schedule regular maintenance, which can help to clear debris from harder-to-find spots.
ConclusionIf you run maintenance in-house, try incorporating these suggestions into your routine. If you don't have an in-house team, then it's advisable to sign up for a planned maintenance program with a qualified provider. While regular maintenance is an extra expense, doing so can help to prevent these common causes of service calls. And that means less machine down time, more productivity, and a better ROI over your equipment's life cycle.