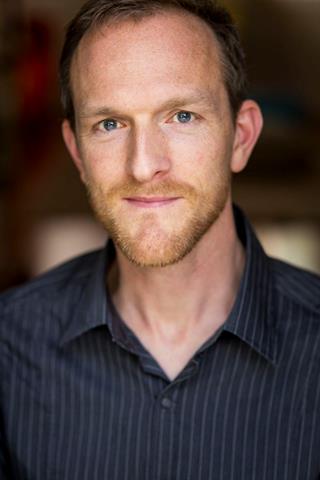 Darren Cottingham |
Darren Cottingham is director of DT Driver Training, a provider of online training courses for drivers of forklifts, trucks and cars.
Myths have crept into forklift training over the last 25 years in New Zealand and the confusion perpetuated by some training establishments is contributing to the more than 2,000 incidents a year.
Our Health and Safety at Work Act 2015 is based on the Australian legislation and is managed by government agency WorkSafe. The responsibility falls on the PCBU (person conducting a business or undertaking) and its officers to implement safe work practices. There's no opting out of the system and you can't buy insurance against potential fines (which can be in the millions of dollars). Understandably, everyone fears WorkSafe, but no-one has the time to wade through 60,000 words of tedious legislation.
When it comes to forklift training, the HSWA2015 and the Approved Code of Practice create a confusing situation. The ACOP, published in 1995, is a set of recommendations and 'best practices' - it's not mandatory to follow them and people have been interpreting them to their own ends. Almost everyone we talk to (including accredited trainers and the industry body, Competenz, that is its custodian) either is unfamiliar with the contents or they have wildly varying ideas about how the ACOP should be implemented and administered. This leads to trainers telling untruths when trying to get business and even Competenz delivering mixed messages.
Common myths are:
1) if your Operator's Certificate expired more than three months ago, you must do a full course rather than a refresher course.
2) you must use a Competenz-approved assessor to conduct a practical assessment.
3) you must do extra 'certificates' for the different types of forklifts you use.
The Act gives much more flexibility to a company to follow its own training path than most people realise. Clause 226(4) states that you can comply with the Act by following the ACOP, but you can also comply with the Act by doing something in a demonstrably better way. So, let's deal with these myths:
1: While it might be a better outcome to do a full course, the ACOP does not say it's a requirement. In fact, you can do a refresher course even if you haven't taken a forklift course in 10 years; obviously, a full course is more expensive, which is why training companies push this.
2: You could use a Competenz-approved assessor for a practical assessment, but you could equally use an experienced forklift operator, H&S manager or knowledgeable training manager following a checklist. Using an external assessor in no way absolves a company of its responsibilities under the HSWA2015 to provide training, supervision, monitoring and information. The reason it's often better to use an internal person is because under the HSWA2015, those internal people are responsible every single day for checking that the operator is operating the forklift correctly (effectively they assess practical driving every day). The practical assessment will then be conducted on the forklift the operator would usually use, lifting the loads they would usually lift and operating around the hazards that would usually be present.
3: Manufacturers make a lot of money out of providing certificates for showing someone how a particular forklift works. While they are useful if someone has no experience on a specific model of forklift, they are not legally required and, under the Act, the PCBU is still responsible for providing its own induction on any equipment used; the PCBU cannot use the fact that a manufacturer issued an arbitrary certificate as a defence that the operator was trained and inducted on the equipment effectively.
The traditional way of supplying forklift training is to send a person on a course. A brief practical assessment follows a theory session. The whole process should take around four hours for a refresher course. The issues with this method are:
· attention span difficulties for trainees that are not used to learning
· no proof the trainees learned or understood the material
· language and literacy issues
· practical assessment is sometimes skipped if time is short
· peer pressure to not ask questions
· difficult for shift workers due to fatigue
· the test is open book
· instructor bias (unintentional or intentional racism or sexism in the classroom, or simply taking a dislike to a trainee)
· it usually uses a forklift the operator is unfamiliar with.
Given the flexibility in New Zealand's legislation (and possibly in other H&S legislation worldwide) every PCBU must ask itself whether the method of forklift training and assessment that it employs is actually the very best that it can provide. We would like to see a focus on the upskilling of all operators and managers so that they are all capable of conducting a practical assessment. That way, they will be best placed to immediately identify incidents of poor or dangerous driving and to suggest remedies.