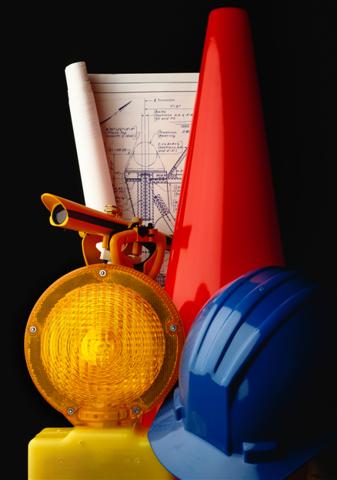 Companies that select trainers based on operating experience alone do themselves and their trainees a great disservice. PHOTO: SHUTTERSTOCK |
Rob Vetter is technical director and managing partner with the Ives Training Group, in Blaine, WA, USA, a leader in North American mobile equipment training systems since 1981.
Recent US Bureau of Labor Statistics (BLS) reports show that worker injury and fatality rates are at all time lows. Whenever the numbers show that fewer people are getting injured and killed, it is good news, but let's not give ourselves a pat on the back just yet. First, we need to stand back and look at the big picture to see if we can identify why the numbers are down; then we need to ask ourselves how we can keep them down.
So, why are the numbers down? The struggling economy has led to a reduction in work and more people out of a job. In turn, less work being done by fewer people means fewer work-related incidents, causing fatality rates to dip. So, it's obvious why worker fatalities are down. However, in relation to the second question, how can we keep them down, the answer is not as obvious. Or is it?
Some economic indicators suggest a dim light now glimmers at the end of the recession tunnel, and people are beginning to trickle back to work. As this occurs, it follows that company safety budgets and training activity will begin to return to pre-recession levels. How quickly this happens depends on which industry sectors recover the fastest and how far safety has been allowed to slip during the economic turbulence. The recovery time of many safety programs is also subject to the unfortunate fact that, in many cases, the first victim claimed by economic strife - and the last to be reclaimed when the scales tip back again - is safety.
Avoiding clashes with regulatory authorities may also affect how quickly safety returns to the forefront. The US Occupational Safety and Health Administration (OSHA) and several provincial regulatory agencies in Canada have made it clear with announcements and demonstrations of aggressive enforcement policies that their tolerance level of regulatory contravention is extremely low.
In any case, the factors driving the economic and industrial recovery are both numerous and diverse. However, the factors that support the rationale behind maintaining a vibrant and effective safety culture, which, of course, includes safety training, are pretty much the same as they have always been. Danger does not ease up or take a break for any reason, and neither should training. The numbers are all well and good, but in the end, they are just numbers.
If your company has let safety slide, citing economic factors as the reason, remind the powers-that-be that maintaining a meaningful safety program is an excellent way to enhance the company's financial performance by eliminating many of the costly consequences, like product and equipment damage as well as bloated insurance premiums, often associated with worker injuries.
Regardless of how many employees work at your company, remember that lack of training or improper training are still the leading causes of workplace injuries and fatalities. More importantly, keep in mind that even with a depleted workforce, it is still just as painful to have to inform someone's family that a loved one will not be returning.