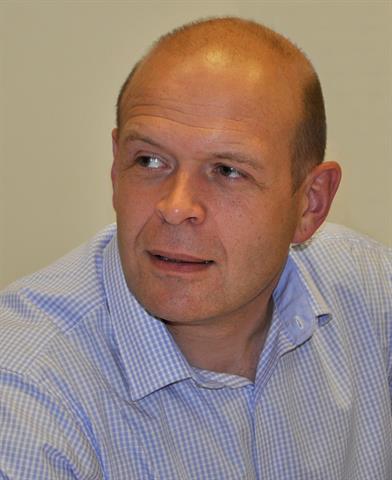 Stuart Taylor |
Stuart Taylor is Managing Director of Mentor FLT Training Limited, the UK's leading provider of training and associated services for all types of materials handling equipment and workplace transport.
Forklifts may appear innocuous, but their capacity to injure shouldn't be underestimated. Nor should their training requirements, as a leading household name recently found out.
Just last year, the company in question received a six-figure fine after a new starter had a serious accident while using materials handling equipment, resulting in reconstructive surgery.
The investigation revealed that the company relied on job shadowing, rather than a standardised training program, to provide operators with the relevant skills. As a result, the company was fined for not providing structured and necessary formal training.
Cases like this demonstrate the real-world impact of the proportional sentencing guidelines introduced last year. But, more than that, they underline the importance of ensuring you're delivering structured training that covers all three essential elements, as required by law.
What the law saysIn the UK, Regulation 9 of the
Provision and Use of Work Equipment Regulations 1998 (PUWER) makes it very clear that an employer must provide adequate training for all persons using work equipment - including how it's used, the risks involved and the precautions to be taken.
Our industry's
ACoP, L117 offers details on what this means. It outlines three types of operator training which must be satisfied by employers.
1. Basic trainingJust as it says 'on the tin', this training imparts the foundation-level skills, knowledge and hazard awareness necessary to operate the type of forklift and handling attachments (if any) that will be used.
While it's possible for an in-house, qualified instructor to deliver this training, many companies prefer to pass this responsibility onto experienced and accredited training providers, an option which often offers good value and makes certain that legal obligations are being met.
The next two training stages can, and should, be delivered by the employer, on site. Importantly, these two elements should be delivered under close supervision by someone with appropriate knowledge.
2. Specific job trainingNormally, this follows basic training and, like basic training, this should take place 'off the job' - away from production and other pressures.
It will be tailored to the employer's needs and include, where appropriate:
- the operating principles and controls of the forklift to be used
- routine inspection and servicing of that truck
- use of the truck in conditions that the operator will meet at work
- instruction on site rules
- training in the work to be carried out
- safe systems of work
This vital training element gives your operators a working knowledge and understanding of the equipment that they will use day-to-day and, importantly, how their truck should be used in the workplace.
3. Familiarisation trainingThis is carried out 'on the job' and under close supervision from an individual with appropriate skills. It allows operators to put into place what has been learned - in normal conditions. This could include:
- applying the skills learned in basic / specific training
- becoming familiar with the forklift activities of the employer
- any other feature of the work which it is not practicable to teach 'off the job' e.g. site layout, local emergency procedures
Why go beyond 'basic'?Most companies recognise the importance of 'basic' training. But this alone doesn't give your operators the tools, skills and knowledge necessary to work as safely and efficiently as possible in their role, with their equipment, in their working environment.
Missing out on specific job and familiarisation training does more harm than just helping you fall foul of the law. It means your business will lose out on the enhanced safety, productivity and profitability associated with properly trained operators; and instead, you'll be at higher risk of accidents, injuries and costly damage.
These two additional stages shouldn't be considered a luxury or even optional; they are a legal requirement. This essential training ensures your workforce fully recognises and appreciates the challenges and risks they'll face every shift.
Most importantly, oversight of these stages is likely to mean your operators will miss out on the close supervision they need in the first few weeks to ensure that they're working safely. This is crucial, with statistics showing that a new starter is more than three times more likely to be injured in the first six months of employment than a long-standing member of staff (more about that next time).
By delivering the three types of training as prescribed by the HSE, you equip your workforce with the skills, knowledge and confidence necessary to keep them and their colleagues working as safely and efficiently as possible.