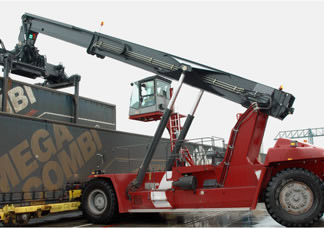 Kalmar DRF450-70S reachstacker |
What makes heavy lift forklifts (10-50T) different from their smaller counterparts? Obviously, heavy forklifts are different by virtue of their sheer size, capability and, of course, price - but essentially there are four main characteristics - working environment, workload, adaptability and the close relationship which forms between manufacturer/dealer and end-user. In the second part of
Forkliftaction.com News' special feature on heavy forklifts,
Melissa Barnett looks at recent innovations and future trends for the leviathan of materials handling.
Heavy forklift essentialsIf forklifts are the workhorses of the materials handling world, then heavy forklifts are the draughthorses - reliable, tough and steady. The size of heavy forklifts means they have limited manoeuvrability and reduced visibility; both factors influence safety and ergonomic design. The huge lifting capacity of up to 55 T exposes them to additional physical stress on parts, engine and chassis and also increases their exposure to potential accidents. According to Richard Umstead, USA regional manager, Cargotec, heavy forklifts are regularly asked to do more than their fair share of work. "Go get the 'big dog' and let's get that thing off the truck", Umstead says, is a common cry across yards in North America. "They know the 'dog' will lift it, they will make it work!" he adds. He concedes that operators often exceed the recommended lift ratings, forcing many manufacturers to "over-engineer" heavy forklifts. Although lifting above the advised weight is not recommended by any manufacturer, Umstead says that Kalmar understands the "big dog mentality" and includes components of a higher rating than the capacity of the truck as standard in their heavy forklifts. The forklifts are rigorously tested in dedicated testing facilities in Sweden or the US before reaching market.
 Linde H160 with rotating cabin |
Colin Flint, head of marketing at Linde's heavy truck division, believes that heavy lifting tasks require that manufacturers invest in a degree of engineering resource in-house not needed by smaller forklifts. "Over 95% of all forklifts manufactured by Linde heavy truck division are bespoke units built to individual end-user requirements," he says, adding "this doesn't happen in the under 10T range".
Dan Johansson, area sales manager at Svetruck, explains that since manufacturing began in 1977, his company has only manufactured forklifts 10T and over, exploiting what he calls a very strong and expanding niche market. Furthermore, there has been a conscious decision by Svetruck to make all components in-house. This, he believes, makes Svetruck one of the few - if not only - forklift manufacturers making their own components in the world today, allowing the company complete control over quality, reliability and design. Svetruck heavy forklifts are "practically built by hand" and, for this reason, the lead time can be quite lengthy - up to nine months. A long lead time is typical for most heavy forklift manufacturers, and customers understand and are willing to wait for delivery of such a costly investment, he adds.
A heavy forklift is an expensive investment - both in its initial purchase price and in on-going maintenance costs - much more than for smaller forklifts. Expect to pay anything from EUR130,000 (USD169,000) for a 10T forklift up to EUR500,000 (USD653,000) for a reachstacker. Container handlers and reachstackers are at the more expensive end, with specialised and bespoke equipment more costly again - task, capacity and cabin comfort are all factors which determine price. Because of the cost of heavy forklifts and the difficulty of replacing one when it's down, reliability is a key factor. Barry Su, deputy general manger of Zheijiang Maximal Forklift, says that heavy forklift systems are more complicated than smaller forklifts, a challenge his company addresses by choosing reliable components, especially in powertrains and hydraulic systems. He believes that components should "meet and exceed" application requirements. Peter Wortley, general manager, big truck operations for Adapt-a-Lift, an Australian Hyster dealer, agrees, adding that because heavy forklifts are so specialised, it is essential to have trained and experienced service technicians to maintain the equipment - more so than for smaller forklifts because downtime is inevitably more costly.
Durability is a word often associated with heavy lift equipment. Ken Mouritzen, managing director of Big Lifts South Africa and dealer in Taylor forklifts maintains that Taylor container handlers and reachstackers have a 40% heavier duty cycle than any other heavy lift forklift. Its rough-terrain forklifts boast welded steel chassis and frames and heavy-duty industrial design steer axles with a single steer cylinder for strength, durability and safety in demanding environments. Taylor's heavy forklift maintenance philosophy is in contrast to most: keeping heavy forklifts easy to operate and simple to maintain.
InnovationHeavy forklift design doesn't happen in a vacuum; it is often the result of intense collaboration between end-user and manufacturer to a degree not usually seen in small forklift design. "Only by visiting the site, assessing the challenges, developing driver training programs and delivering the right features for a particular application can manufacturers and end-users minimise the risks to their work force and ensure that the operating environment for heavy forklifts is optimised," says Linde's Flint.
Patrik Lundbäck, marketing director for Konecrane, believes that in the case of emissions and noise, regulation has driven innovation. Hyster Big Truck Division has a dedicated special project engineering department (SPED) tasked to address design issues - including issues raised by new legislation. Hyster has worked with its engine supplier, Cummins, to address Tier 4I/stage IIIB emission regulations. The regulations require diesel engines to reduce particulate matter (PM) exhaust emissions by 90% and oxides of Nitrogen (NOx) exhaust emissions by 40%. The regulations include all machines over 16T, including reachstackers and container handlers.
Lundbäck also believes that safety, ergonomics and all other innovation is driven by the end-user. Konecranes' NearGuard is a case in point, having been developed from a customer's need to reduce the number of times his staff collided with overhead conveyor belts. The NearGuard system, which won the IMHX 2010 design award, is an early warning system consisting sensors mounted on the forklift and RFID tags. The tags can be placed on sites or clothing around the work site. Once a tag is located, NearGuard warns the driver. The system engages at a range of 50 meters.
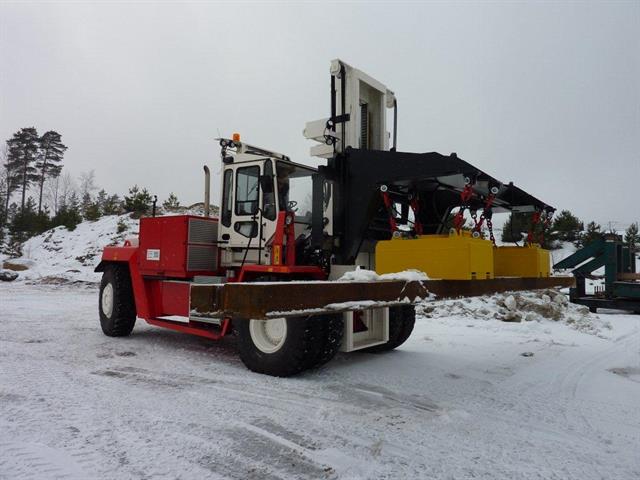 Svetruck 32120-46 with steel carrying magnets |
Johansson has a similar story with Svetruck's hydraulic pipe clamp. The original clamp, with mechanical stop, was designed in collaboration with Coast Centre Base - an oil and gas supply company with bases throughout Norway and the North Sea. CCB needed a faster, more convenient and safer method of transporting gas and oil pipes on and off the supply ships. Previously, pipes were transported using three men, cranes and slings. It was dangerous work, with the risk that the pipes, up to 12 m in length, could roll forward. Svetruck designed the first pipe clamp in 1991 and has recently released new versions with hydraulic stop and in 2011 as an optional attachment.
Safety in heavy forklifts is a recurring theme - the bigger the machine, the heavier the load, the smaller the margin for fatal error. Clark Equipment's Omega E-series has been designed with safety in mind, with one of the highest tip-up safety factors in the industry. The Omega range is built specifically for specialist applications. A spokesperson for Clark equipment Australia says that the Omega range has a core group of heavy forklifts with specialised variants available for specialist applications.
Added Extras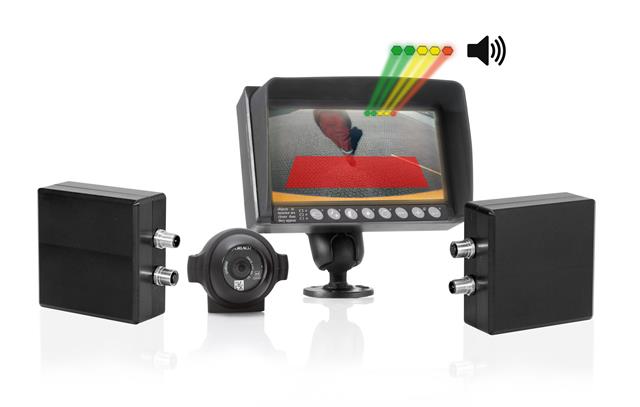 Orlaco RadarEye system |
Most heavy forklift manufacturers need to source parts and accessories from independent suppliers, so certain companies become intrinsic to the functionality, efficiency and safety of heavy lift forklifts. Dutch company, Orlaco designs and manufactures camera systems for heavy industrial equipment as well as supplying a number of OEMs. Orlaco cameras can be fitted to the rear of a forklift to improve rear-views, but can also be mounted inside container handler spreaders. The camera in this position allows the operator a clear view of spreader and twistlocks, enabling him to safely guide the twistlocks into place. A system of cameras mounted around the forklift provides the driver with a clear line of sight around and behind the forklift; all the camera views can be directed to one monitor mounted in the forklift cabin. Laurens van der Rijt, Orlaco's business development manager, explains that close co-operation with heavy forklift OEMs has had a major influence on camera design. Most recently, the company released a radar system in response to end-user requests. The RadarEye alerts the driver audibly and then visually via the inside monitor when there is an object in the forklift's 'danger zone'.
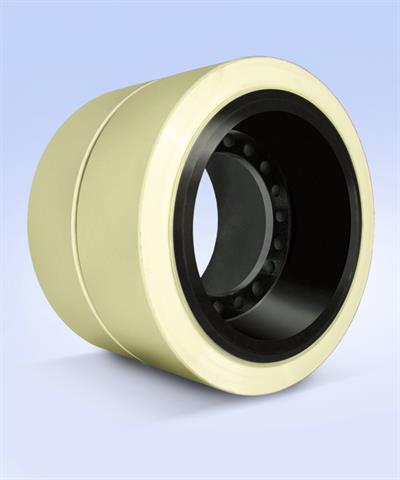 Superior's Cushothane XL |
Tyres are, of course, an essential component of any forklift, but on heavy forklifts, they play a significant role in performance. Changing a tyre on a 50T forklift can be both costly and time-consuming. Hank Le Meur, CEO of Superior Tire and Rubber Corporation, explains that heavy forklifts require different tyres to smaller machines because of the very high ground pressures that they generate through low speeds and greater weight. For this reason, heavy lift forklifts require tyres with a different compound. Superior's Cushothane XL tyres offer extremely high cut-and-tear strength, minimising tyre "chunking" (chunking happens when a patch of tread has loosened and is torn off by centrifugal force at speed). Heavy forklifts have the potential to outlive their original technology, making parts such as tyres difficult to source. Superior has an in-house library of wheel/hub combinations, which means it can rebuild or manufacture new wheels without OEM specifications.
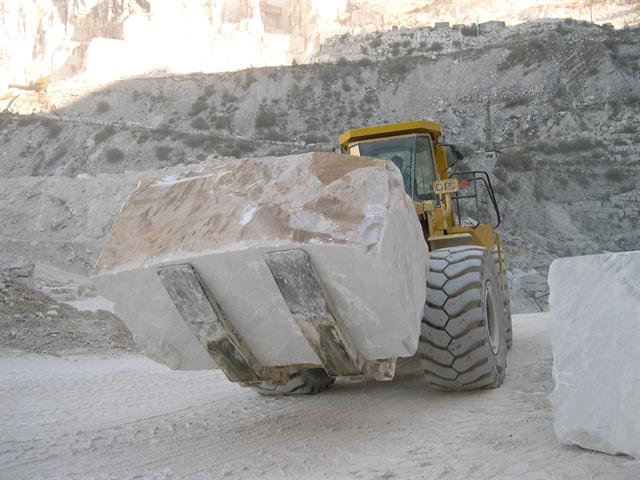 Scana Booforge's heavy duty fork-arms at work |
Bespoke design for heavy forklifts doesn't just stop with cabins and engines. Often they require customised fork arms as well. Strength is extremely important when choosing fork arms. Swedish company Scana Booforge believes that the correct alloy and heat treatment during manufacture provides the strongest arms for heavy-lift requirements. Scana Booforge has developed two steel alloys specifically for heavy lifting purposes - RO651 and HRO774. It notes that fork arms are ideally made using single hammer-forged billet rather than flat rolled bar as fatigue resistance is higher and strength is optimised in forged steel. The arms are then heat-treated. Heat treatment makes the fork very hard on the surface but with a softer core. The more accurate and controlled the heat treatment, the better the result. Scan Booforge has its own in-house, certified heat treatment facility.
Future trendsThe future looks exciting for heavy lift forklifts. Demand is increasing, driven by customers wanting improved efficiencies. "They want to carry more, lift higher and do it in less time," says Konecranes' Lundbäck. He believes that most manufacturers have been tied up for the past few years designing forklifts to comply with the new emissions standards. Now that they have been met, he believes European and North American manufacturers can turn their attention to other projects. Konecranes will be releasing two new products later this year focusing on safety and fuel savings, he says, declining to provide any details.
Ard Stoffer, sales manager for Dutch used equipment dealer Forkliftcenter, believes that ease of use is a future trend for heavy forklifts. He also predicts innovation that addresses noise regulations.
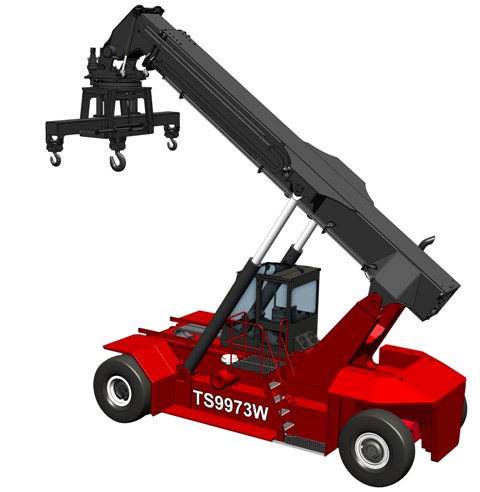 Taylor TS9973 reachstacker equipped with attachment for transporting wind tower and parts |
Thomas Malmborg, vice-president of Cargotec (Forklift), believes that ongoing strategies in response to sustainability and energy efficiencies will drive R&D at Kalmar. His colleague Richard Umstead adds that we will see more restrictions on diesel engines which could result in use of alternative energy sources. He's tipping electric forklifts in heavy forklifts as well as more efficient hydraulics and drive lines to reduce load on the power source. Alternate energy sources are also a focus at Taylor, with a number of Taylor TS-9973W reachstackers being modified to handle and position wind tower blades and parts.
Hyster's SPED is looking with interest at barge handling, which requires a negative lift from below a quayside, design for tyre-handling forklifts particularly for the mining sector, designing heavier forklifts - up to 56T and modifications to heavy forklifts in extreme conditions of heat and cold.
At Doosan, spokesman Jaekwang Lee believes the logistics sector is very important and that Doosan will be concentrating its effort over the next few years on developing heavy forklifts to cope with a constantly changing work environment and improved maintenance services.
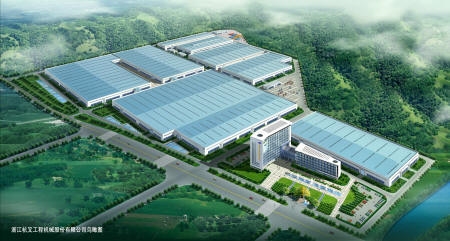 Hangcha is planning to expand its manufacturing facility to cover 399,600 sq m |
Despite the recent downturn in most global economies and the impact it has had on R&D funding, the heavy forklift sector seems resilient, with reports of steady sales and improved order books. Continued concentration by government on legislation for lower fuel emissions, "green" technology and alternative energy sources will no doubt influence future R&D for the majority of manufacturers. Together with strong relationship building and an understanding of the importance of service and reliability the heavy forklift sector looks set to meet the big challenges ahead.
Additional information by our contributors:
THE OMEGA HEAVY TRUCKS RANGE DELIVERS PRODUCTIVITY AND COMFORTClark Equipment: Website,
OMEGA Models Specs-------------------------------------
THE RIGHT FORKS FOR HEAVYLIFTSScana: website,
ShopFront-------------------------------------
NEW MAXIMAL "A" SERIES FORKLIFT: ENGINEERING FOR THE DRIVERMaximal: website,
ShopFront-------------------------------------
MECLIFT VARIABLE REACH TRUCKS - ATTACHMENTS FOR VARIOUS LIFT TASKSBig Lift South Africa: website-------------------------------------
BIGFORKS FOR BIG FORKLIFT TRUCKSVetter: website,
ShopFront-------------------------------------
DOOSAN, THE WORLD'S LEADING VALUE FORKLIFT BRANDDoosan: website,
ShopFront-------------------------------------
INTRODUCING FORKLIFT CENTERFokliftcenter B.V: website,
ShopFront-------------------------------------
A NEW TIRE DESIGN FOR HIGH DEMAND & EXTREME DUTY HEAVY LIFT CUSTOMERSSuperior Tire: website-------------------------------------
HANGCHA, ONE TEAM ONE DREAMHangcha: website,
ShopFront-------------------------------------
LINDE HEAVY TRUCK DIVISION RECENTLY UNVEILED NEW PRODUCTS AT THE PORT OF MINDENLinde Material Handling GmbH: website,
ShopFront-------------------------------------
SVETRUCK, HIGH PERFORMANCE & CAPACITY TO SPARESvetruck: website,
ShopFront-------------------------------------
ADAPTALIFT HYSTER H36-48XM(S)-12 FORKLIFT SERIES MAKES A GREAT TRUCK EVEN BETTERAdaptalift Forklift Rentals & Sales: website,
ShopFront-------------------------------------