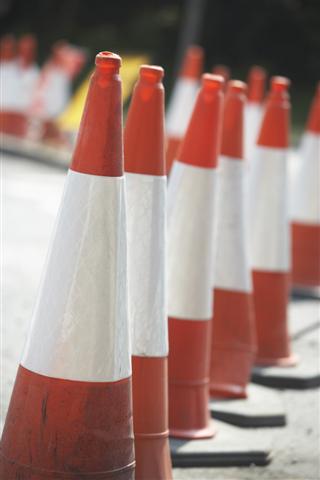 A solution that removed an immediate safety hazard. PHOTO: SHUTTERSTOCK |
Rob Vetter is technical director and managing partner with the Ives Training Group, in Blaine, WA, USA, a leader in North American mobile equipment training systems since 1981.
In my neck of the woods, forklift operator training must include components that address the specifics of the equipment being used by the operators and the workplace in which it is used. These site- and equipment-specific requirements are meant to ensure that operators get training that applies to what they actually do on the type of equipment they actually use, which is a good thing. Unfortunately, the framers of the regulations neglected to include another vital component, addressing the specifics of the trainee. In a sense, you could say that operator training must be equipment-, site-, and trainee-specific.
For example, I once delivered an operator program at a location where six people intermittently used the single forklift they had. One of the six, a bright young fellow who was refreshingly eager to take part in the training, had completed the classroom theory portion of the program brilliantly. Based on his classroom performance and what I had learned of his driving history, I figured he was a shoo-in to pass the practical evaluation.
As I watched him approach the forklift later that afternoon in the warehouse, he fumbled his cell phone after shutting it off and dropped it. Then, he turned around, bent down, picked it up and continued on his way. I couldn't quite put my finger on what exactly it was, but something seemed amiss. It was just that his movements seemed, for lack of a better term, unnatural. As I watched him engage his first load and start to back out, he twisted his entire upper torso around in the seat in a tremendous effort to perform a (decidedly unacceptable) look to the rear before reversing. Then it hit me, he could not move his head independently from his shoulders - and if it continued, he was not going to pass his evaluation.
After the second load, I stopped and asked him about it. He told me he had chronic arthritis in his neck.
"Does it come and go?" I asked.
"No, it's pretty much always there," he answered.
"How often do you drive the forklift?"
"Hardly ever. Maybe once a month." So much for my earlier 'shoo-in' assessment.
"But you can't look behind you."
"Well...no, not really." Unbelievable!
"Hmmm. OK, here's what we're going to do. I'm going to continue with this evaluation but from here on, I am going to act as your spotter. I want you to make eye contact with me each time before backing up and wait for my signal. If everything goes smoothly, I am going to tell your boss that you need to have a spotter each and every time you drive the machine."
"Works for me, I hardly drive the thing anyway." And on we went.
His boss wasn't happy, and that was without my telling him how incredibly irresponsible I thought he was to put a driver with an arthritic neck on a forklift. Was it the best solution? I don't know, but the way I look at it, I served the one by accommodating a disability (which, by the way, I am required to do) and I served the many by putting in place a solution that removed an immediate safety hazard. What would you have done?