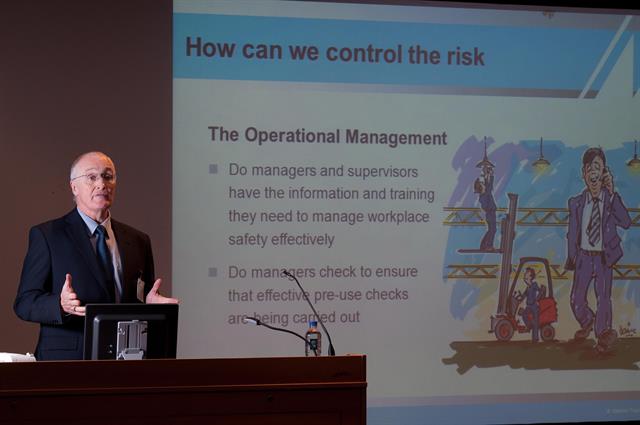 Steve Baldwin |
Steve Baldwin is technical manager with Mentor FLT Training Limited, the UK's leading provider of training and associated services for all types of materials handling equipment and workplace transport.
Most countries will have an overarching set of rules or regulations which govern health, safety and welfare at work. In the UK, this legislation is the Health and Safety at Work Act 1974 which says that, among other things, employers have to provide their employees with such information, instruction, training and supervision as is necessary to ensure their safety.
Unfortunately, many employers don't do all these things and, by not doing so, end up costing their company more in the long run due to damaged forklifts, racking, stock, building fabric, etc. On top of this, they are also leaving themselves wide open to charges by the relevant authority (HSE or EHO in the UK) in the event of an accident, followed by the inevitable compensation claim from the injured employee/s.
So, what is the missing link in running a successful forklift truck operation? Well, it's enshrined in one word: 'supervision'
Most employers these days understand that they have to provide their forklift truck operators with training but, unfortunately for many employers, it stops there as they then rely on the operator to operate correctly from then on.
In an ideal world, this would be fine but, unfortunately, human beings are not like machines that once programmed will continue to operate in the same way. Humans have individual needs, aspirations, frailties and ideas about how things can be done and what is safe or unsafe.
So what information, instruction and training do managers of people who use forklift trucks require to enable them to manage effectively? This falls into three main categories:
Firstly, they need to understand what the law requires of employers and of them as supervisors;
Secondly, they need to know what financial and custodial penalties could be levied upon them for not managing/supervising correctly; and
Thirdly, they need to understand the equipment properly by having a good knowledge of things such as:
➢ the stability characteristics of forklift trucks and the types of operating procedures which would cause them to become unstable and possibly even tip over;
➢ the ability to carry out a pre-use check along with knowledge as to what makes a truck safe or unsafe to use;
➢ the basic rules for operating safely.
Armed with all this knowledge, they can then set about proactively managing forklift operations and taking action against those operators who ignore their training and the company's procedures.
This not only reduces forklift operating costs by reducing the damage mentioned earlier, but it also protects the workforce - including the forklift drivers themselves.
To illustrate this point, I can relate a true story that happened to one of our instructors. He was working for a few days at one of our customers' sites, undertaking counterbalance refresher training. On his second day on site, a counterbalance truck was loading a customer's flatbed vehicle when the vehicle drove off, tipping the forklift onto its side. So how did this save the forklift driver's life? Well, the driver had taken his refresher training the previous day, so knew all about why he should be wearing a seatbelt. When the truck started to tip over he tried to jump off but couldn't because the seatbelt prevented him. If he had not been wearing the seatbelt, he would have jumped - but then would probably have been crushed by the overhead guard, the dreaded mousetrap. The day after the accident, the forklift driver approached our instructor and said that if the instructor hadn't been on site, he wouldn't have been wearing his seatbelt - even though he knew he should and would, therefore, have possibly been killed or seriously injured in the accident instead of just getting a few bruises. It was custom and practice that the site management team allowed drivers to operate without wearing seatbelts. Now ask yourself why they didn't enforce the wearing of seatbelts:
1. Was it because they didn't understand why they should be worn?
2. Was it because they didn't understand their own responsibility to provide effective management?
3. Was it because they didn't have the motivation to manage properly to protect their staff?
Whichever, the result would have been the same had our instructor not been there.
To recap:As well as being a legal requirement to provide effective management, it also makes sense financially and morally that everyone should expect to go home after a day's work with the same number of limbs, eyes, etc.
To those employers who are providing operator training, well done. But please spend the small amount extra needed to arm your managers and supervisors with the information they need to manage effectively as this is crucial and is also THE MISSING LINK.