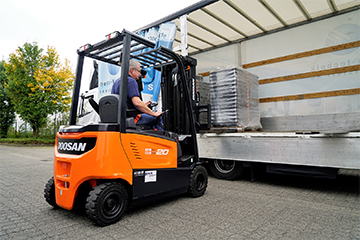 Doosan engineers safety into its products |
Each year
Forkliftaction News receives alarming reports on industrial accidents involving forklifts. Many of these accidents result in injury, disability and, far too often, death.
Melissa Barnett asks manufacturers if good forklift design can improve safety and whether the most common forklift accidents can be prevented at the drawing board stage.
The German Social Accident Insurance Group (DGUV) recently released statistics for Germany showing an increase from 10,500 reportable non-fatal forklift accidents in 2012 to 12,809 in 2016. Meanwhile, in the keynote address at this year's Forklift Truck Association (FLTA) safety conference (UK), Phillip White, head of operational strategy at the Health and Safety Executive (HSE), said that approximately 1,000 people a year continue to be seriously injured in forklift accidents in the UK, and worryingly, there has been no significant evidence of improvement in those numbers in recent years.
Increasing demand on logistics equipment means that forklifts are working faster, longer and in tighter spaces than ever before. They are moving heavier loads and lifting them higher. As demand increases, so too does the risk of injury.
While the number of fatalities remains static worldwide, there is a disturbing upward trend in non-fatal forklift accidents. While proper and comprehensive driver and workplace training is essential, building safety features into forklift design is also crucial. George Rechnitzer, principal engineer and director at George Rechnitzer and Associates, in his discussion paper on the role of design in occupational health and safety states that design "is the stage of any project which represents the greatest opportunity for injury prevention".
Common accidents and design solutionsPaul Watson, sales director (UK) for Doosan Industrial Trucks, says that collision with objects or people and crush injuries are accidents that happen far too often:"Two-thirds of all forklift accidents trigger harm to someone other than the vehicle handler".
"In recent years, a great deal has been done by Doosan to reduce the number of injuries both within the warehouse and in the yard and, while a major influence has been more rigorous training of drivers and better adherence to work practices, a significant factor has been the effort made by Doosan to engineer safety into its products," says Watson. Doosan's new safety feature, the Automatic Electric Parking Brake on the 7-series electric range, ensures that if an operator dismounts the truck without applying the handbrake fully, the machine will not roll away, even if the machine is left on a slope or ramp.
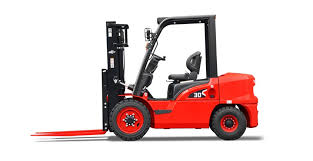 Hangcha X-series IC forklift |
Bob Wang, marketing manager for Chinese manufacturer Zhejiang Hangcha, sees three main areas of potential risk: when getting on and off the forklift there is the risk of slipping; while driving due to tip-overs; and, thirdly, during service or maintenance when service personnel can be injured by sharp parts and components, scalded by hot parts or fluids and injured by rotating parts. Wang says Hangcha follows three design principles: eliminate potential safety hazards through design; isolate any part that may cause personal injury with protection if the hazard cannot be eliminated at time of design; and provide comprehensive safety notes if the first two measures are not practical.
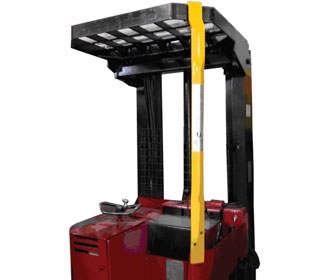 An innovative safety device to protect operators of stand up industrial trucks against accidental rear-ward collisions with racking systems. |
In a perfect world, says Norm Nopper, managing director of Canadian manufacturer Lakeport Metalcraft, we could catch problems before they cause harm. "The initial reaction to an accident is to look at the human error, but that's not getting at the root cause to solve the problem and prevent repeated incidents. We should be looking more closely at forklift design to see where we can adjust, improve or re-design," says Nopper. Lakeport have designed a retro-fitted safety device for pedestrian forklifts. The Backbone for reach trucks addresses the hazard of stand-up forklift under-ride, which occurs when a rack crossbeam intrudes into the operator cabin, crushing the operator between the beam and the front of the cabin and/or the boom. Under-ride happens because the backs of most reach truck cabins are open, with no physical barrier between the operator and horizontal cross beams. The Backbone is an American National Standards Institute (ANSI)-compliant safety bar that acts as a bumper, providing that missing physical barrier.
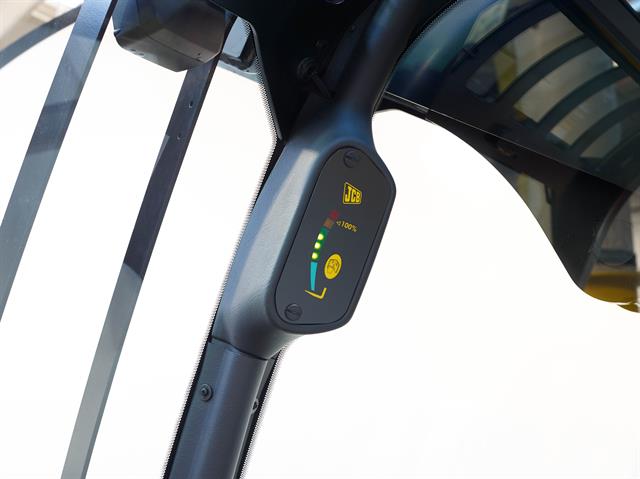 JCB Load Moment Control Indicator |
Paul Murray, general manager for JCB Teletruck in the UK, says collisions due to restricted forward visibility and tip-overs caused by machines operating outside the appropriate load chart/stability triangle are two common accidents he sees regularly. "Design innovation has been central to overcoming safety challenges right from the beginning at JCB Teletruck. Our process is focused on customer needs. We benchmark against existing models, define the required product attributes and set an innovation benchmark; we then design, build a prototype, test and prove. A result of this process is the JCB-patented Load Moment Control Indicator which is designed to warn the operator of a forward-tip risk - automatically cutting out the hydraulics if the machine is operated outside the load chart," says Murray.
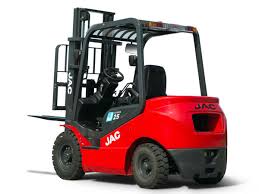 JAC forklift |
Two activities that Damon Yu , sales manager for JAC Forklift says regularly contribute to forklift accidents are driver mis-operation of the mast causing it to go down suddenly and over-speeding causing the forklift to tip over. Yu believes that design can solve both old problems and anticipate new problems. JAC's forklift design incorporates a mast buffering system which ensures the mast is stable when lowered and a lifting/ lowering locking function so the mast cannot be moved unless the driver is in the forklift seat. A turning speed limit function has been designed so when the driving speed is more than 5 km/h and the steering angle is more than the pre-set angle, the driving speed will automatically reduce. "Design also needs to be improved when there is a new problem; the process never stops," he says.
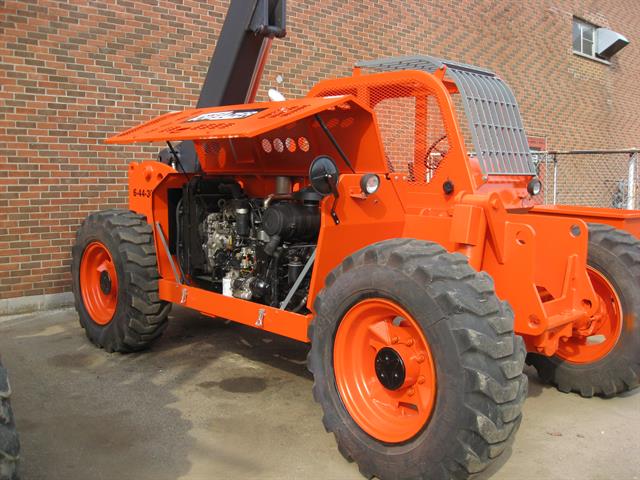 Tovel - designed to be easily serviced |
Often, the action that best reduces injuries is prevention. Sal Franco, vice-president of sales and marketing for Canadian company Tovel Manufacturing, believes that poor forklift maintenance can contribute significantly to injury. "Tovel units are designed to be easily serviced - access to all regularly maintained items and components is designed to be quick and easy so there are no excuses not to properly maintain equipment," explains Franco.
Johnson Hsu, sales director for Tailift, says that while safety training is important, it is essential that equipment manufacturers meet safety compliance standards. "In our design process we use 3D computer imaging to match the mechanics and to simulate the hydraulic system before assembling, this helps us to meet CE certification and compliance standards"says Hsu.
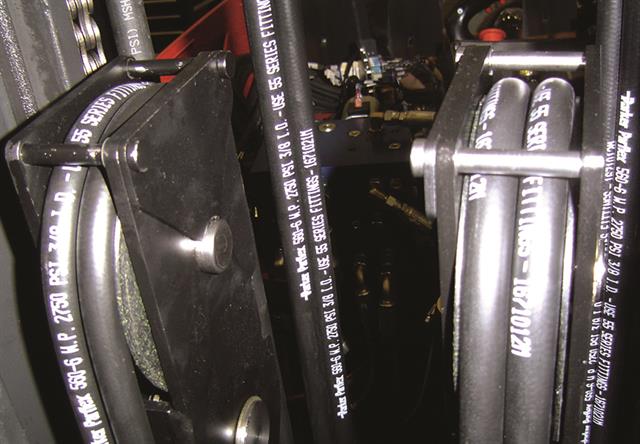 Parker Hannifin Toughjacket oversheaf for forklifts |
Greg Hayes of US-based Parker Hannifin Corporation believes that there should be an understanding that all injuries are preventable and manufacturers should establish a complete commitment to preventing them. "Today, even with the use of programs or processes like Failure Mode Effects Analysis (FMEA), problem solving, virtual reality, functional test stands - processes that can identify and resolve problems during design, there is still a need for customer feedback from product use to ensure expectations are being met," says Hayes. Parker has designed the Toughjacket, a thermoplastic sleeve that covers the sheave hose on a forklift. It is resistant to cover abrasion which takes place when materials being carried by the forklift shift on the skid and come into contact with the hoses. Catastrophic failure of hoses can cause dangerous oil spills which workers can slip on or result in oil injection injuries. The latter is particularly concerning because oil injection injuries do not look like much more than a pin prick but can cause significant health issues if not tended to by medical professionals, explains Hayes.
Martin McVicar, an engineer by profession and the managing director of Ireland's Combilift, sees good design and innovation as integral to Combilift's core business. He believes innovation can raise awareness of how not to do things, even if certain practices had previously been considered the norm. "In an ideal world, a solution can be addressed before it becomes a problem but, sadly, accidents or spotting the potential for an accident on a certain product are often the trigger for a re-think or a re-design," he says.
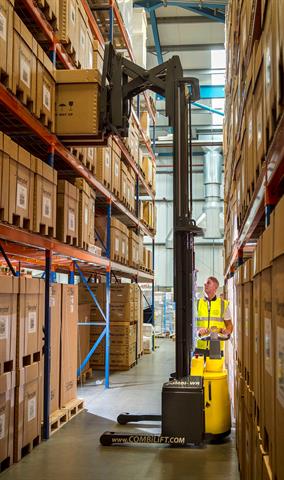 Combilift Combi-WR pedestrian reachstacker |
"We are strong believers in designing forklift trucks which are intuitive to operators. We take a lot of feedback from customers - managers, drivers and service engineers, who have often used other types of products in the past, and their experience is very valuable when designing new products," says McVicar. Combilift pedestrian trucks are a case in point - designed with a multi-position tiller from inception to avoid the problem on other brands of pedestrian truck where the operator has to be in between the racking and the truck in narrow aisles.
Design is a chicken-and-egg situation: what comes first - the problem or the solution? Without doubt, design is the core of all equipment manufacturing. How design addresses safety issues such as overloading, speeding, roll-overs and collision is an ongoing concern to everyone involved in the business. Lost hours, lost time, lost money and, most importantly, lost lives mean that forklift design must be stringent. The best prevention, some suggest, is training team members about the risks with systems and recognising failure modes before they happen. But operator awareness is only part of the safety story: how well a piece of equipment is designed to mitigate the failure modes is the other part of the story. As Rechnitzer insists, design is the stage of any project which represents the greatest opportunity for injury prevention.
Additional information and a special 'THANK YOU' to our sponsors:JAC Heavy Duty Import & Export Co., Ltd.: website------------------------------------
THE BACKBONE® FOR REACH TRUCKS STOPS STANDUP FORKLIFT UNDERRIDELakeport Metalcraft Inc: website------------------------------------
TOUGHJACKET TM ABRASION RESISTANT HOSE - BUILT FOR SAFETY
Parker Hannifin Corporation: website------------------------------------
10TH DOOSAN FOR META-TECHNIK KUNSTOFF KG
Doosan Corporation Industrial Vehicle: website------------------------------------
HANGCHA DISPLAYS THE 'NEW LOOK OF MADE IN CHINA' AT CEMAT ASIA 2017
Hangcha: website------------------------------------
TAILIFT TAIWAN INTRODUCES AN EVOLUTIONARY UPGRADE FOR THE POPULAR 9L SERIES
Tailift Material Handling Taiwan Co., Ltd.: website------------------------------------
Combilift: website------------------------------------
Tovel Manufacturing Inc: website------------------------------------
JCB Teletruck: websiteDid you enjoy this feature? There is still time to take up our 2018 early-bird contributor special!