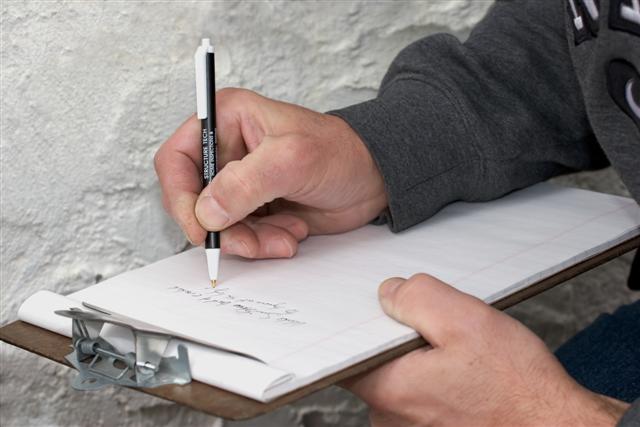 Supervisors should be routed through the same training as their operators. PHOTO: dreamstime.com |
Rob Vetter is technical director and managing partner with the Ives Training Group, in Blaine, WA, USA, a leader in North American mobile equipment training systems since 1981.
It is encouraging to see the improvements in the attitudes and actions of workers, supervisors and employers toward forklift safety since I entered the workforce back in the mid-1970s. Back then, forklift safety was conveyed passively and almost never enforced to any effective degree. It was my experience that if you wanted to be safe, you had to ask for things like training and PPE, which was begrudgingly and often poorly distributed.
This is largely not the case today as the increased development and enforcement of forklift safety regulations over the years have raised the awareness of forklift safety among employers which, in turn, has allowed them to realise many potential financial gain,s, made possible through using their forklifts and all of their mobile equipment safely. Likewise, operators who have realised that working safely is not merely a matter of following rules and avoiding discipline, but a means to living their personal lives to the fullest by avoiding the devastating consequences of injury suffered at work are enjoying the core benefits of working safely.
However, there is one link in the chain between employers and operators that, in my opinion, is lagging behind the others in terms of receiving the information and training needed to do their jobs properly, and that group is supervisors.
Supervisors are often overlooked in the overall safety plan of many companies, which creates a critical flaw that ultimately weakens the safety chain, often to the point of failure.
It's not that supervisors don't get the information and training they need to keep themselves safe, but that they don't get the information and training needed to ensure that the operators under their watch are working safely. Hence, the critical flaw that creates the opening for operators to work unsafely or otherwise contrary to any training received is because their supervisors lack the knowledge to recognise the situation - much less correct it, as is their duty.
Recognising this situation is one small step for employers, but doing something about it is the one giant leap they must make if they expect to enjoy the benefits of a well-implemented and maintained forklift safety program. The key word here is
maintained, in that it incorporates ongoing, sustained effort directed toward consistent and dedicated delivery, enforcement and improvement of the overall safety plan at every link in the chain,
especially the supervisors!
Supervisors must be involved in the safety plan. It is their duty and responsibility to ensure it is delivered, understood and carried out by every operator on their crew every hour of every day. To do that, they must be given as much knowledge and training as their operators and the means to recognise, correct, reward and/or discipline operators who do not follow safe work procedures as per their training.
Wherever possible, supervisors should be routed through the same training as their operators. The goal is to provide them with information and knowledge about how to properly and safely perform the work that the operators under their supervision perform. There is no need to evaluate their competence in job-specific tasks unless they are expected to perform such tasks. By participating in this training, supervisors are more able to actively and effectively
supervise workers. Where it is not possible for supervisors to undertake the training their operators do, some effort must be made to equip them with basic information of how and why workers are being trained to use the equipment to do their jobs. This basic information could be conveyed to supervisors through abbreviated training sessions that do not include the practical hands-on components of full operator training sessions, briefing sessions where only safe work methods and procedures are reviewed or perhaps simplest of all, providing supervisors with job-specific checklists containing "must do" safety items that they could use as a quick reference while monitoring operators.
There is no doubt the accessibility, quality and general buy-in of forklift safety and operator training throughout all levels of business and industry have increased exponentially. Employers and workers are now enjoying the numerous benefits that may be realised through working safely with the equipment from corporate financial efficiency to the most precious asset of all, quality of life, if not life itself. However, there is work to be done to improve the strength of the safety chain which can be achieved relatively easily by including supervisors in the mix and providing them with job- or task-specific knowledge and empowering them with the means to ensure that forklift safety training marks the beginning of the process, not the end