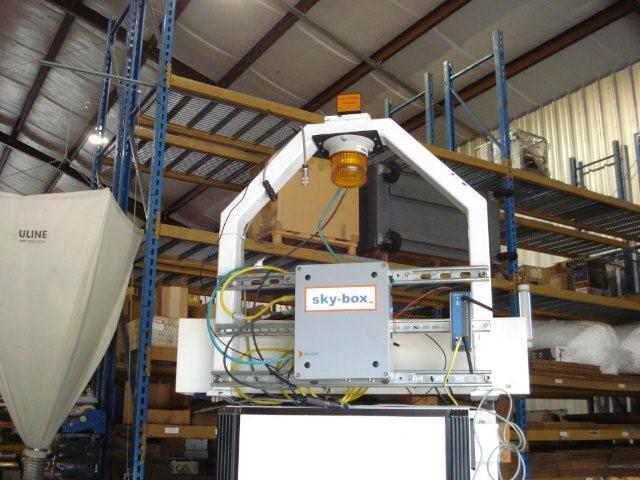 Sky-Trax Optical Position Sensor (orange box) mounted on a demo AGV together with a temporarily installed Sky-Box controller |
Sky-Trax's successful demonstration of its new materials handling technology has brought global positioning systems indoors and has the potential to help businesses work smarter.
The warehouse solutions company teamed up with Amerden AGVS in Florida recently to demonstrate Indoor Position Sensing (IPS). IPS is a technology, designed by Sky-Trax, capable of tracking mobile equipment and inventory in any building with pinpoint accuracy.
Sarah Sagin, vice president of marketing for Sky-Trax, says IPS can be compared to GPS because it provides an XY location, direction and speed. "However, the difference is IPS is designed to work indoors and to be more accurate - inch-accurate - and uses optical rather than radio wave technology."
The IPS sensor is a digital camera and image processor that is mounted onto a vehicle so it looks up to the ceiling. It works by capturing and processing an image of the ceiling at 10 times per second and based on what it has seen in the image, is able to calculate where it is in the building.
The demonstration at Amerden's facility involved retrofitting an automated vehicle originally designed to use standard laser guidance systems with Sky-Trax's IPS. With a few tweaks to the AGV controller software, the AGV was able to navigate freely within the warehouse, pick up a pallet and precisely move it to a new storage location.
Roland Anderson, president of Amerden AGVS, says only software modifications to the standard CB40 AGVE controller software were required for the demonstration.
"The end result opens the door to many exciting possibilities for vehicles, operating environments and specialised adaptations."
The IPS demonstration is part of the Sky-Trax's CCV (Centrally Controlled Vehicle) program. Sagin says this program is the next-generation AGV. "The system's design allows Sky-Trax to introduce the first remote controlled, free-roaming, automated indoor vehicle intended to work in the same work space as traditional forklifts.
"CCV does not need to be 'taught' any paths or have any pre-defined routes," she says. "It can move from any point to any other point just like a driven vehicle."
CCV does not require existing buildings to be modified or to undergo any additional capital modifications for it to be incorporated into a workplace. The program works cooperatively and safely with fleets of manned vehicles. All vehicles - manned and automated - are continuously monitored, tracked and controlled as a system to ensure optimal travel and routing.
Sky-Trax has been working on the CCV program for over seven months. Sagin says it was officially launched in April at the NA 08 Trade Show and Conference in Cleveland, Ohio.
Sagin comments one of the best features of CCV is how easy it is to install. "CCV is made to operate in any existing building. It is intended to operate in an environment that already uses Sky-Trax's Total-Trax.
"A CCV can be dropped right into that environment with software configuration."
Sagin adds CCV will eliminate labour costs as it automates standard repetitive warehouse operations. "Our first CCV is a driverless electric pallet jack. It can handle the horizontal transportation of pallets between the docks and storage racks - leaving manned forklifts to work more efficiently on loading and unloading trucks."