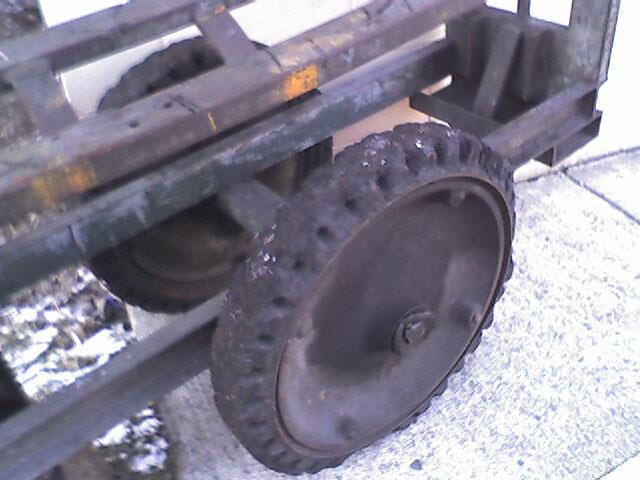 A 50-year-old cushion tyre. |
The rise of forklift technology and the emergence of 24/7 distribution warehouses have resulted in forklift tyres working harder than before. The modern pneumatic tyre was invented more than 100 years ago and solid and cushion tyre technologies are more than 50 years old. Is forklift tyre technology up to speed?
Christine Liew reports.
Tom Dell has been in the tyre industry for more than 30 years. He once had his own tyre business but, after selling to Solideal Canada, he now works as vice president of sales & marketing for Toronto-based Solideal Canada (formerly Unitrac Industrial Tires Inc). Solideal Canada manufactures forklift tyres, construction, off-the-road tyres and rubber tracks.
He told
Forkliftaction.com News he was dubious about the current advance of forklift tyre technology.
"Today the quality and technology built into forklift tyres are as high as they have ever been. However, technological advancements with forklifts, along with facilities in which forklifts work 24/7, have put large demands on this dated forklift tyre technology," he said.
John Boyd Dunlop developed the pneumatic tyre for his son's tricycle in 1887. He obtained a patent for it in 1888. Most engine forklifts use pneumatic tyres. Electric forklifts use solid or press-on tyres, which have been around for more than 50 years.
(In the UK, solid tyres (pneumatic profile) are known as resilient solid tyres. They are pneumatic shaped solids in the USA, PPS in major European markets and, in some regions, puncture proof or super elastic. Press-on (lower profile) tyres are made of rubber/polyurethane bonded to steel bands. Depending on the tread design, Watts Industrial Tyres, UK, calls them cushion or plain. In the USA, they are called traction or smooth.)Dell said forklift tyres were cheaper today but less durable because of "how they are used and who uses them". Reduced durability has cost implications because it is expensive to change tyres, especially if forklifts are in regional areas.
The Unitrac facility, in Toronto, Ontario, operates nine mobile press trucks that instal 2,500 to 3,000 solid tyres remotely at customer locations a month.
"[However,] if you go to Winnipeg, Manitoba, there is no mobile equipment that would instal forklift tyres," Dell said. Changing a forklift tyre is a complicated, costly process. A CAD150,000 (USD138,844) truck with a CAD10,000 (USD9,056) tyre press and a trained technician is needed. A customer can receive a three-hour bill at CAD60 (USD54) an hour to have tyres installed by a forklift distributorship's mechanic.
Jean-Francois Ferron, design engineering manager at Toyota Industrial Equipment SA, which has a manufacturing facility in Ancenis, France, said forklift tyres were crucial to a forklift's productivity and safety.
Tyres' rolling resistance impacts on the maximum speed of the forklift and tyre durability. The higher the resistance between tyre and ground, the more energy is required to move the forklift. Reducing rolling resistance can help fuel efficiency.
"Tyre durability [which relates to truck productivity] depends on rolling resistance and material composition of the tyre. If a tyre manufacturer can reduce rolling resistance and improve the chemical composition of the tyre, we can expect better durability," Ferron said.
"We have experience with some brands of tyres for which the stability and durability are much better than their competitors. When we sell a truck, depending on the type of tyres we mount, performances are not the same."
China demand for raw materials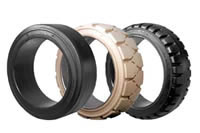 Solideal rubber press-on tyres. |
Apart from durability, the forklift tyre industry has several things to contend with. Tyres may be cheaper, in Tom Dell's opinion, but raw material prices have hiked in recent months. Many have attributed that to high demand for raw materials in China (
Forkliftaction.com News #248). Additionally, tyre companies must deal with imitation tyres from China.
However many see China as an opportunity, not a threat. Richard Blacker, from Sydney-based Bearcat Tyres Pty Ltd, an Australian industrial wheel and tyre distributor owned by Solideal International Group, said Solideal's China manufacturing base had been running for five months.
"We had to look at another manufacturing base. China was the way to go. China has a very high import duty. For us to get products into China, we had to pay the duty, hence the initiative to build a facility," he said.
Blacker said Bearcat would receive tyre shipments from the Qingdao plant in the coming weeks. Solideal's European headquarters controlled product quality tightly and any product that did not meet the mark would not be accepted.
On Chinese tyre manufacturers, Blacker said some did not have ISO approval ratings but major ones did. "The quality is not too bad but some do not meet the high level of quality the Europeans and Americans have.
"Generally speaking, people prefer high-quality, deep treaded tyres compared to cheaper, low-depth treaded tyres," he said, maintaining Chinese manufacturers were not a threat to European and American manufacturers.
He agreed tyre technology had been "fairly static over the last 20 years" but conceded forklift tyre manufacturers were looking at ways to improve tyres.
The NMW challengeTyre manufacturers are now developing non-marking white (NMW) rubber compounds. Warehouses, especially in food and pharmaceutical industries, do not like black stains left by black tyres. But the black carbon in tyres is what, industry members say, gives tyres their long life.
Dell said the use of NMW tyres was popular in warehouses.
"Warehouses [in Canada] today are sparkly clean, immaculate and with newly-painted machinery. There are no more sweatshops. Sweatshops are gone.
"Non-marking rubber compounds continue to advance. There is an ever-present challenge to develop a NMW rubber with the same life as a typical black rubber. Today all manufacturers have this goal and it is close to being realised."
Richard Blacker said Bearcat Tyres was changing the compound for its NMW rubber.
"We're (Solideal) using a grey compound instead of a white compound. It's 20 per cent longer life and 10 per cent cheaper than previous NMW rubber. It's the black stuff which makes it last longer."
Blacker thought tyre companies could produce more durable tyres.
"Tyre companies can certainly produce a long-wearing tyre but it shows in the price. At the moment a lot of tyre testing is going on, using a lot of European tyres.
"But research & development costs a lot of money and these projects take a lot of time." He said the rising cost of raw materials did not help.
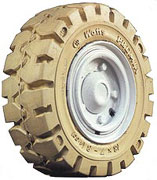 A non marking white Watts Premia tyre. |
Watts Industrial Tyres, Lydney, UK, a leading global tyre manufacturer, is working on ways to improve its rubber compounds. Watts exports 60 per cent of its pneumatic and solid tyres to more than 60 countries and has subsidiaries in USA, France and Germany.
Carlo Piccirilli, Watts sales & marketing director, said compound technology had to keep pace with the "new generation of forklifts that were more powerful today than 20 years ago". Watts was working with the OEM forklift industry to ensure tyre design met new forklift technology's demands, he said.
"We are looking at compounds with higher heat resistivity as well as new developments in NMW and electrically conducting tyres." Piccirilli said Watts was developing a compound with anti-static properties but would not comment further.
Asked to comment on Watts's NMW rubber, Piccirilli said the important carbon black ingredient was being substituted with different compounds.
"In many cases, a NMW tyre will last as long as a black tyre and it's a misconception in the industry if that is thought not to be the case. Although carbon black is an important ingredient for optimising wear, when producing a NMW tyre the blacks are replaced with silica-based compounds giving it the same performance as a black tyre."
Piccirrili did not give differences between the life of NMW and black tyres. He said it depended largely on application, loads and working environments but, generally, he saw "marginal differentials in wear rate" with Watts's compound development.
Having historically manufactured in Europe, Watts now has a joint venture with Chinese manufacturer Guizhou Tyre Co Ltd, in Guiyang, Guizhou Province, which was established in 2000. Watts and Guizhou co-operate on technology, distribution and manufacturing.
The China Industrial Truck Association said China's forklift sales reached 75,000 units in 2005. China has 340,000 forklifts in service and forklift sales are expected to reach 120,000 units by 2010 (
Forkliftaction.com News #257).
The non-marking black tyreVulkollan is a raw material produced by chemicals and pharmaceutical giant Bayer AG of Leverkeusen, Germany. A member of the polyurethane family, it costs about 2-1/2 times more than rubber, and is used by tyre manufacturers to make solid tyres and wheels. Tyre manufacturers using the orange-brown coloured material must use the Vulkollan name in their tyres.
Belgian family-owned tyre manufacturer Vulkoprin NV has been making Vulkollan tyres and wheels for more than 40 years. "Vulko" in the company name comes from Vulkollan, "pr" stands for pour, French for "for", and "in" is from the Dutch word for industry. Vulkoprin considers itself a specialist in Vulkollan tyres, having perfected its production process over the years.
Sales and marketing manager Philippe Vindevogel told
Forkliftaction.com News about 95 per cent of European OEMs used Vulkollan tyres and wheels for electric warehouse forklifts because other materials could not meet the forklifts' high specifications.
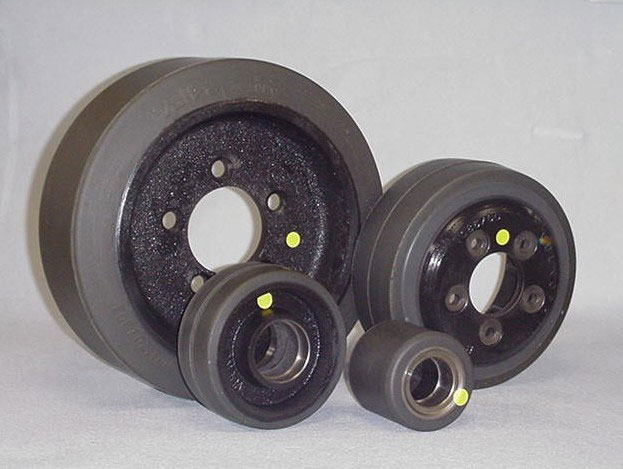 Vulkollan wheels are marked as electrically conductive by a yellow dot. |
"Vulkollan has the highest load capacity and it's to do with specific mechanical properties of the material itself. It has three to four times higher load capacity than wheels with the same dimension in rubber and slightly higher than polyurethane.
"It is very heat resistant, its mechanical properties not changing much in a wide range (-35C to 85C) compared to -5C to 50C for rubber/polyurethane," he said. Its heat resistance has seen Vulkollan tyres used in roller coaster trains.
Vulkoprin makes press-on Vulkollan tyres (Vulkollan bonded onto steel rims) and Vulkollan wheels. The manufacturer is continually "redesigning the wheel" to optimise its performance for specific customer applications.
An example is Vulkollan electrically conductive wheels, introduced in 2005.
"It's not redesigned from zero but based on a standard. It can be used in areas at risk of fire and explosion from explosive or inflammable particles," Vindevogel said.
The Vulkollan electrically conductive wheel is non-marking and black, instead of orange-brown, the natural colour of Vulkollan. The black colour was the result of a "secret" additive to Vulkollan that made it electrically conductive, Vindevogel said. Anti-static wheels existed in the market but Vulkoprin was currently the only manufacturer producing electrically conductive Vulkollan wheels. (
Editorial correction: Räder-Vogel of Hamburg, Germany, also produces electrically conductive Vulkollan wheels/ July 2006)
While Vulkoprin was not hit by rising rubber costs, high prices of steel and oil had created problems.
"There is a lot of pressure from the customer. Basic ingredients are going up, [but] the customer is asking us to reduce prices.
"But that is the problem all other Vulkollan tyre manufacturers have. We all have the same weapons to fight with. That's the game we play in," he said.