In Part 1, we saw how a big lift operates in a different environment to a small lift. Big lifts not only have larger load capacities but are heavier machines with bigger components and engines. In this feature, we explore three current trends in the design and engineering of these machines: the use of electronic technology, the simultaneous increase in load capacity and decrease in machine size, and operator comfort.
Big lifts carry big loads that, as William Lowry, from Lowry, said, are often costly and sometimes irreplaceable. While care is taken with loads, the safety of big lift operators must also be considered. These trends, if not implementing operator safety, are taking it into account. Christine Liew reports.Trend 1: Electronic revolutionTracking loadsEarly this year Kalmar established a new business unit, Kalmar Intelligence & Automation, to focus on developing and marketing on-board smart features for container handling equipment.
Although
Kalmar spokesperson Lotta Sundstrom cites safety and driver environment improvements as current trends in design and engineering for big lifts, she said the biggest trend involved electronic technology.
"The big change in the last few years is the 'electronic revolution' and it seems to be endless," Sundstrom said. "The biggest trend is new tools for communication, where you can monitor machines' performance via the internet and global positioning systems (GPS)," she said, adding that Kalmar used GPS in its container handling equipment.
Kalmar offers two GPS-based products, Smartrail® autosteering, a container position verification system for RTGs (rubber-tyred gantry cranes) and Smartpath®, a container position verification system for straddle carriers and RTGs.
Using differential GPS technology, Smartrail® steers the RTG along 'invisible' tracks, relieving drivers of the need to steer and allowing them to travel at maximum speeds between lifts and concentrate fully on picking up and setting down containers.
The Smartrail® system is supposed to be simple to install and maintain as there are no buried wires, transponders or painted lines to be maintained. It also records new positions of handled containers, saving the time spent looking for lost or misplaced containers.
The majority of Kalmar RTGs that have been ordered over the past two years have been fitted or retrofitted with the Smartrail® system. They include cranes delivered to terminals in New Jersey, Oslo, Dublin, La Spezia, Dunkirk, Livorno, Kumport and St Petersburg.
"(Another) feature that is getting more use is what we call remote monitoring interface (RMI), a system enabling the operation of a large number of machines to be monitored remotely by a single operator in the terminal control room. It is currently used for RTGs but will be used in many more Kalmar machines in future," Sundstrom said. RMI is a monitoring and maintenance software used in computerised Kalmar container handling machines.
"Other communication options have to do with service. The service technician can add new features, track problems and do preventive maintenance via his laptop and mobile phone," Sundstrom said.
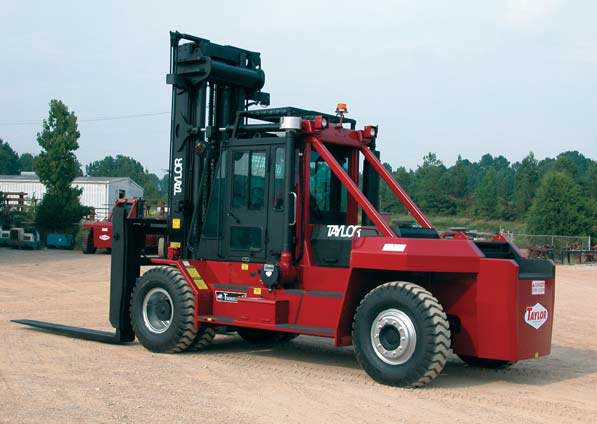 Taylor TH-350L |
Robert Taylor, president of
Taylor Machine Works, said he thought electronic technology would bring the most impact to the industry.
"The (greatest) change we will have in the future will be in integrated control, GPS tracking, remote monitoring and all the features technology brings us.
"We have been intensely testing new technologies to ensure durability and longevity are number one. We are moving forward with ergonomics and efficiencies of integrated control systems to ensure we have the lowest life-cost product on the market," Taylor said.
SafetyWilliam Lowry, from
Lowry, said his company offered a computer-generated capacity verification program free to customers to help ensure maximum load weight and load centres for big lifts were handled effectively.
"Maximum load weights and load centres are the responsibility of the operator. In the US, all operators are required to be trained to OSHA standards and that includes load weight and load centre verification," he said.
"A load centre is the halfway distance of the load to be handled measured from the front face of the forks. Most lift trucks up to 30,000 lbs are measured at a basic 24 inch load centre.
"As the load centre increases, available capacity decreases and it is extended load centres that often cause operational problems.
"At Lowry, real base lift truck capacity requirements are computed through an engineering program that converts the known weights and load centres into an inch-pound calculation.
"The total inch-pounds required for a particular application are recomputed back into a suggested model and capacity that will safely handle the maximum load weight and maximum load centres on a customer application basis," Lowry said.
"At Lowry we have an application and capacity verification survey we ask dealers to complete and sign with their customers.
"Having advance knowledge of maximum weights and load centres, the type of loads and the working environment, allows us to select the best possible capacities and specifications to safely handle the customer's product."
Lowry also told Forkliftaction.com News about the APC controller (APC), an electronic control box that is interfaced electronically with the big lifts' transmission.
"The APC is a new feature, a transmission controller that is pre-programmed with safe shift and speed parameters. It prevents operators from exceeding safe shifting and operational speeds," Lowry said.
"Go into any high-cycle production or warehouse facility and look at the floors. Black tyre marks are often the result of operators travelling, shifting and braking at excessive speeds.
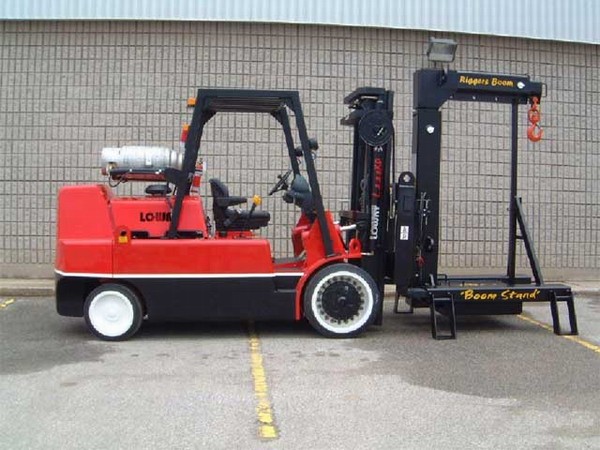 Lowry L220XD |
"What you don't see is thousands of dollars in damage being done to the transmission, drive axle, steer axle and brakes and mast and carriage assemblies. The APC slows that cycle down and, in many cases, eliminates the potential for such damage," he said. The pre-programmed safe transmission shift and speed parameters protect big lifts' mechanical components from poor drivers who operate the machines in an unsafe manner.
"For example, a driver may attempt to shift from forward to reverse direction at high speed. Imagine doing that in your car and the mechanical damage it would cause. Imagine doing that one to 200 times a day for five years. APC will not allow the operator to complete the shift if the speed is too high."
Greg Pannia, from
Omega Lift Manufacturing Inc, said using a controller to control speeds and other functions had changed the way machines moved and operated.
"We also have a way to do things to the machines online and in real time, in case of breakdowns. Everything is on a screen in front of the operator and all functions are off a joystick."
Trend 2: Compact sizeIn Part 1, we mentioned that
Rigger Xtreme and
Hoist were two manufacturers who claimed their big lifts were physically smaller than average big lifts. Joining the trend is
Lowry, which is making advances in compact design but with increased capacity.
William Lowry said that, compared to the same capacity made 10 years ago, his forklifts were becoming more compact and having bigger load capacities.
"There has been a market-driven requirement by heavy lift customers to manufacture more capacity in a very compact, highly manoeuvrable design but at the same time they are also demanding higher mechanical reliability and productivity.
"A few inches in width or length and turning radius are a big deal in the forklift business," he said. "New models like the L300XD will lift 30,000lbs (13,608kg) at 24 inch load centres but this model is considerably smaller in width and length than older models of similar capacity yet equal in gross body weight."
Lowry said standards set by OSHA/ANSI as a guide for OEM manufacturers would set many design parameters.
"As forklifts get smaller, they can only do so within OSHA/ANSI requirements for safety," he said.
"Lowry has, in the heavier lifts, been a leader in width at only 56 inches wide from 18,000lbs through to 35,000 lbs. Most of our competitors are at least six inches wider.
"OSHA regulations for rearward visibility, combined with the very narrow widths we have already accomplished on our heavy lifts, have brought us to a point in design that may allow a few inches of future savings but nothing radical.
"We already have the lowest point of gravity in our designs and use extensive internal counter weighting to accomplish safe lifting capacities in the smallest frames possible," he said.
Rigger Xtreme president Michael Salter said increased capacity and smaller size was also a design and engineering trend for his company. However, he stressed that the safety of his machines would not be compromised.
"We always make our trucks well within the safety limits of the load picking. However, there are limits to what you can do. Up to a certain size, 120,000lbs (54,431kg), we can keep the main base weight down to 42,000lbs (19,050kg). After that, the base weight goes up. So it affects price and weight."
The base weight is the machine's shipping weight, not its fully assembled final weight. The biggest forklift Rigger Xtreme is currently building, for its client Precision Tube, has a base weight of about 98,000lbs (44,452kg) and its final weight will be about 170,000lbs (77,110kg). The forklift will have a capacity of 200,000lbs (90,718kg).
Trend 3: ErgonomicsFor
Hoist, which claims to be the world's largest manufacturer of compact cushion-tyre trucks, its trend was to "make the operator comfortable as he does his job".
"Our trend is improved ergonomics. Make it easy and safe (for the operator) to get on and off the forklift. Give the operator the best possible visibility to increase productivity and safety," Hoist sales manager Terry Troutman said.
SMV Konecranes' 10-60 tonne Spectra range has also been designed with operator comfort in mind. The company said on its website, in order to work efficiently and safely over long shifts, the operator must have a really good working environment.
"Our forklifts have what is probably the best cab on the market in terms of visibility, ergonomic design and comfort
"The cab is designed with large windows that give the best possible visibility in all directions and all controls are positioned comfortably within reach and view of the operator."
The Hyster H1150HD-CH container handler, which is working at P&O Ports Louisiana, has the improved ergonomics of the ComforCab II which makes it easier to exit and enter the truck.
Port equipment manager Gus Bertucci said:
"Our operators say it takes much less effort to get in and out because there's more room. They don't have to squeeze in because there are no controls in the way. It's a lot more comfortable without being congested."
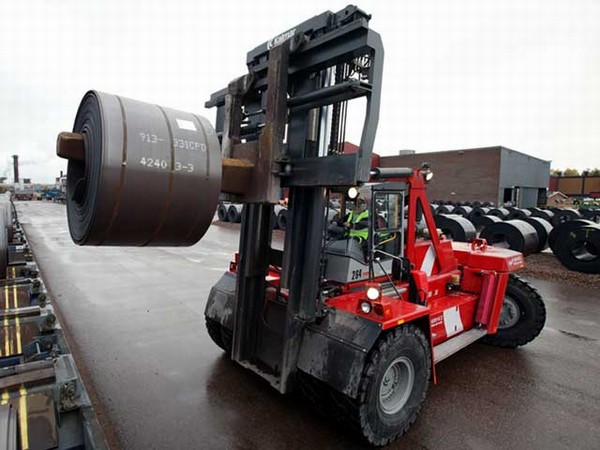 28-tonne Kalmar DCD |
Kalmar, which claims to be a frontrunner in ergonomic design, has a wide range of options to give the best driver environment possible.
"(For our Delta Spirit cab), there are a host of possible individual settings and extras for customers to choose from. For example, for our paper handling forklift, we offer the Kalmar Delta Spirit Space, a cab modified for optimum vision and comfort. The driving compartment can be rotated through 180 degrees and the turning of the driver's seat only requires a gentle movement. The entire driving compartment, including the pedals, steering wheel, controls and computer equipment, follows the seat's movement," Sundstrom said.
Click here to see more photos of big lifts in our Photo Gallery