A forklift is a key piece of equipment in any logistics chain, but buying a new machine may not always be the best financial or practical solution for all businesses. There are other options.
Melissa Barnett looks at forklift refurbishment and reconditioning.
A used forklift may better suit requirements but there are some essential questions to ask before buying a refurbished forklift or deciding to recondition equipment. Usually the decision is price driven. Reconditioning or buying a reconditioned machine is often a cheaper short-term option than buying new, but the quality and extent of the refurbishment will determine whether it will be a good long-term decision. Typically, a refurbished forklift with 2,000-4,000 hours will cost about -half to two-thirds the price of an equivalent new forklift. Luc Deleener, spokesman for Belgian used forklift and spare parts dealer Matermaco, says customers always decide what is of value when it comes to reconditioning a machine. Some believe EUR10,000 (USD 13,500) is the limit, others EUR1,000 (USD1,350) .
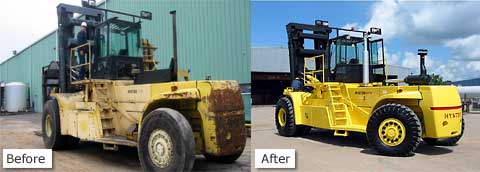 Hyster H970 Image courtesy of American Lift and Equipment |
Refurbished machines are not just used machines; they have had major work on engines and bodies and should come with a certification for all work done. It is recommended buyers have an independent inspection conducted on any forklift being considered for purchase. The first thing to consider when purchasing a refurbished forklift is the machine's history: where has it worked, what were the working conditions? Check whether the machine has a serial or model number, this will indicate whether it is branded equipment and give some indication of the origin of its parts. Check the forklift's hours and inspect all its parts to ascertain whether they are in good working order and are genuine. The cost of a refurbishment depends on its scope, the machine's age, the price of replacement parts and labour costs.
Fiorella I. Navarro Honores, of Spanish company Atica Servicios, believes the high cost of labour is the most prohibitive component in refurbishments. Suitably qualified technicians are scarce. Honores complains there is a lack of theoretical and practical training for forklift technicians in some parts of Europe. Lee Hamre, of Hamre equipment, California, whose company deals in forklifts of 50,000T. and above, believes there is a similar trade skill problem in the US and says it is very difficult to find good qualified technicians to work on large machines with computer controls. Carol Roberts, of American Industrial Transmission, says despite US trade schools offering more places, the number of graduating technicians has not increased and there will be continuing problems in the future. Those who are qualified are not 'average' forklift mechanics but highly trained technicians with electrical, computer, and mechanical skills and therefore more costly. In the USA, workshop fees can be $50-$65/hour.
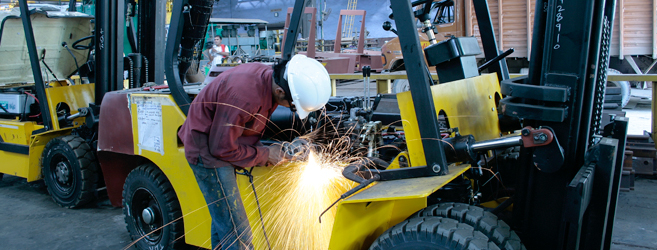 Forklift undergoing refurbishment at Volta's workshop. Image courtesy of Volta Forklifts,India. |
Most reconditioned forklifts tend to be internal combustion (IC) diesel forklifts. Although diesel forklifts require more maintenance during their working life, due to a greater number of moving parts than electric, they have a longer lifecycle and therefore are ideal for refurbishment. Deleener says he sees fewer electric forklifts reconditioned unless they are also equipped with specialised equipment, such as triplex 4.5m-4.8m masts. Electric forklifts, in contrast to IC machines, require less maintenance over their lifetimes but are more difficult to repair and reconditioning needs to be very precise. Deleener believes refurbishing the newer generation of forklifts is becoming less attractive for dealers like Matermaco, because current onboard technology is complicated and specialists are often too far from their customers to be of any help.
Hamre says most machines his company refurbishes are empty and loaded container handlers of more than 50,000T. He says 90% of the machines will be for export to third-world port operations. US companies don't tend to refurbish those types of machines when they have reached their use-by hours because of environmental issues, particularly in sensitive areas. They do, however, trade them in or resell them for refurbishment. Jerrel Djaidoen, marketing manager for Toyota Material Handling, in the Netherlands, says in his experience recently manufactured forklifts are popular but rare to find for refurbishment.
Top 10 things for forklift mechanics to check:- Any part that needs lubrication;
- Dirty oil or antifreeze;
- Clean radiators and transmissions. The engine fan acts as a vacuum, sucking dust and debris from the floor into the radiator, resulting in an engine that runs hot. Engines that have run hot over a sustained period of time inevitably have problems and damage;
- All pivot points. Steer axle pivots and kingpins carry a forklift's weight and can grind down if inadequately lubricated;
- Leaks - hydraulic fluid in the lift/tilt assembly shaft, battery water, motor oil and radiator fluid;
- Rust and weld seams;
- Tyre rubber for peeling or cuts;
- All safety devices - horns, strobes, safety belts, and operator space;
- Fans, belts and exhaust systems; and
- Most importantly, check the machine had been truly refurbished, which means it has been taken apart, operational and mechanical problems have been resolved and it has been tested before sale.
Parts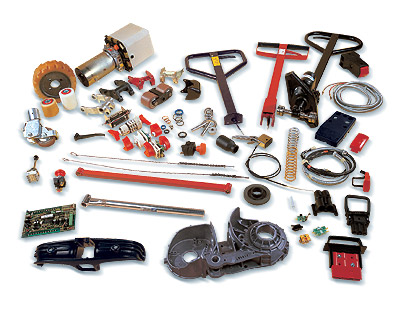 Parts image courtesy of TVH |
Sourcing parts for forklift refurbishment appears controversial. Parts can come from the internet, OEMs or specialised used and new forklift parts suppliers. Your budget will determine your choice. Parts can be OEM - own equipment manufactured - or non-OEM, also known as non-genuine, aftermarket or will-fit parts.
Generally manufacturers and most dealers to whom
Forkliftaction.com News spoke prefer OEM parts to be used when their equipment is refurbished. They argue OEM parts are better quality, last longer and come with a manufacturer's guarantee. Many forklift manufacturers have long lists of potential problems when using non-compliant parts and believe there is no guarantee non-OEM parts meet manufacturers' engineering specifications. Manufacturers argue that although the parts may come from the same supplier, non-OEM parts are often built with inferior materials. That is particularly evident in filters, brakes and computer circuit boards.
The reality is, refurbishers will use the cheapest or most readily available replacement parts. Even well-known forklift manufacturers source parts from third-party suppliers, called sub-assemblies, or remanufacture their own parts. Crown forklift part numbers often differ from their OEM part numbers because they use sub-assemblies from other major suppliers. Clark prides itself on its remanufactured parts used in refurbished Clark forklifts. The difference perhaps is that well-known manufacturers back their parts with warranties and a commitment to quality.
Djaidoen says since the Japanese earthquake and tsunami last March, Toyota has experienced difficulties with parts availability, forcing some companies to use non-original parts, but he admits price is also a consideration in choosing non-OEM parts. Frank Sterner, a solutions specialist at SJF Material Handling, in Minnesota, USA, recently wrote in MHW in support of Chinese manufactured forklift parts, arguing the issue is not about inferior quality but price. "Many Chinese parts manufacturers have produced parts for brand-name forklifts for years but now sell direct to the US market at significantly reduced prices to name brands," he says. Sterner says such competition is good for the refurbishment industry. Another issue is parts availability. Roberts says previously parts would be available for 40 years or more but now OEMs have reduced availability to 15-20 years on most forklift models.
Green and safeIn the USA, forklifts powered by electric and IC engines must be constructed to the American national standard for powered industrial trucks part ll. All operational forklifts, including reconditioned forklifts, require a certificate of thorough examination. In Europe and the UK, all forklifts, including refurbished equipment, must meet the Provision and Use of Work Equipment Regulations 1998 (PUWER standards) and the Lifting Operations and Lifting Equipment Regulations 1998 (LOLER standards).
Although it may be difficult for older refurbished forklifts to meet environmental standards in some countries, the refurbishment process is 'greener' than buying new. Roberts says casting new parts requires more energy and raw materials than remanufacturing. She believes the materials handling marketplace is becoming more aware of the lighter environmental impact of reconditioning and remanufacturing and responding positively.
ValueIn times of economic constraint, every dollar counts and the current market has encouraged growth of what was once a small cottage industry to a size where there are now factory reconditioned forklifts available in quantities attractive even to fleet users.
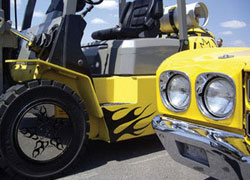 Masterlift's 2007 sales campaign "Pimp Your Lift" |
Some well-known forklift manufacturers, including Linde, Toyota and Flexi Narrow Aisle, recognise their machines' second and third life value, offering refurbished forklifts alongside new and used stock, together with refurbishment services and spare parts. "Over the past five years a thriving market for used Flexi forklifts has developed," says John Maguire, sales and marketing director for Flexi Narrow Aisle. "We have built up an efficient spare parts operation, which means Flexis are very cost effective to refurbish. Typically a used and refurbished Flexi will be sold for around 60% of its new price - a bit like a classic sports car which is worth almost as much restored as when [it was] new," he says.
Linde Material Handling's used and rental truck division head, Phillippe Mulot, says Linde sees forklift refurbishment as integral to its business and has refurbishment centres in all important markets, including China. It has 7,000 forklift technicians and 700 service support points worldwide for refurbishing machines, the same support level as Linde's new truck division. Mulot says Linde's strategy is to "strengthen the business with refurbished forklifts, especially in emerging markets, and offer additional services according to requirements and customer needs in those markets".