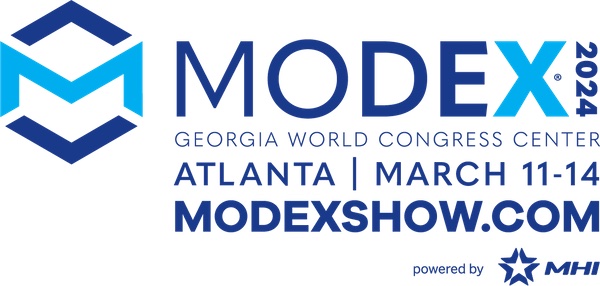
The biggest-ever MODEX has wrapped up, with many of the 1,200 exhibitors focusing on new technology to solve the ongoing labour shortage being experienced around the globe.
The biennial four-day supply chain trade show at the Georgia World Congress Centre in Atlanta attracted a record 48,733 registered attendees, one third more than the number of visitors to MODEX 2022.
The trade show featured the latest in supply chain technology and innovation in North America, with a strong focus on automation, robotics and autonomous vehicles, devices that can augment, supplement or replace human labour, which is in short supply in most developed markets.
At the exhibition, VisionNav Robotics launched its latest automatic trailer truck loading and unloading solution, the VNST20 PRO automated guided vehicle (AGV), which can load and unload a trailer truck in 45 minutes.
The VNST20 PRO, which has a rated load capacity of 2 T, will be available in the US from 2025.
The new AGV combines VisionNav’s VNST20 autonomous forklift with fleet scheduling software and 3D LiDAR SLAM technology. It’s designed for trailer trucks, automating loading, unloading and manual handling tasks.
VisionNav says the VNST20 PRO is compatible with a wide range of trucks in North America and Europe, and can be tailored to a variety of pallets, including EPAL and CHEP.
The FPSS1500 pallet shuttle is available in two models, one for ambient environments and one for cold environments
Singapore-based HWArobotics launched four new product lines at MODEX: three tote shuttles and a pallet shuttle.
The company is seeking to further its push into the North American market after Canadian third-party logistics (3PL) business Darwynn installed its solutions last year.
HWArobotics’ stand showcased its new SLS300 standard tote shuttle, SLS400 variable tote shuttle and SLS600 3D tote shuttle, as well as the FPSS1500 pallet shuttle, which has a model for room temperature environments and one for cold storage.
“The recent deployment of HWArobotics shuttle systems by Darwynn demonstrates how our technology can be up and running quickly and effectively, automating and optimising logistics and storage processes,” says HWArobotics general manager Sky Chen,
“Our strong global customer base, including Bosch UAES, Hisense Hitachi, SONY, iCOOP, Shein, Joyson Safety Systems, JD.com and Forvia, is testament to the capabilities we offer to companies seeking intelligent upgrading of their warehouses and manufacturing plants.”
Sure Sort X can handle customer-sortable items weighing up to 9 kg
Opex Corporation launched its OPEX Sure Sort X automated sorting system at MODEX, as well as the OPEX Xtract order retrieval system.
Opex says the combination of the two systems meets customer demand for one integrated solution to sort, retrieve and automatically transfer products into the final container.
Sure Sort X can handle items 60% smaller, nearly 20% larger, and up to 300% heavier than its predecessor, all while maintaining a consistent throughput of up to 2,100 items per hour.
This system can handle customer-sortable items weighing up to 9 kg and sort items into a configurable array of mixed bin sizes and types.
Opex’s iBOT delivery vehicles can manoeuvre throughout the Sure Sort X system with the ability to change destination in real time.
Sure Sort X can operate in both chilled and ambient environments and the system can be installed in as little as a week.
OPEX Xtract can be added to any Sure Sort X system by adding retrieval iBOTs to work in conjunction with the traditional sortation iBOTs.
Piaggio Fast Forward's kilo has a payload of up to 130 kg
Piaggio Fast Forward (PFF), the Boston-based subsidiary of the Italian scooter maker Piaggio Group, presented kilo, a hands-free flatbed robot with a payload of up to 130 kg.
The kilo model uses the follow-me technology installed in two previous models of PFF robots available in the US, gita and gitamini.
The Piaggio Group is already planning to implement kilo on the new Moto Guzzi production lines to assist operator manoeuvres.
Piaggio Fast Forward chief executive officer Greg Lynn says: “From manufacturing to any industry that relies on the repetitive movement of goods across campuses and production facilities, PFF’s autonomous technology allows our robots to safely move with and around workers in complex environments, streamlining workflows and increasing productivity.”
Designed to work alongside humans, kilo uses PFF’s proprietary Travel on Known Paths autonomous behaviour software, which gives the robot the ability to follow an operator or move autonomously.
Schneider Electric launched two new Lexium collaborative robots (cobots) at Modex, and foreshadowed the release of another new model.
On display at Schneider Electric’s MODEX booth was the company’s new Lexium RL 3 and RL 12 models, as well as the Lexium RL 18 model which will be released later this year.
The new models are part of a full line of robotics and automation solutions designed for the warehouse/logistics, life sciences and consumer packaged goods industries.
The cobots can be integrated into Schneider Electric’s EcoStruxure system to enable collaborative data flow from shop-floor to top-floor, by connecting smart products, robots, controls, software and services.
Third Wave Automation launched the autonomous TWA Extended Reach forklift
Third Wave Automation (TWA) also focused on solving labour challenges in warehouses at its MODEX exhibit.
As well as launching a new extended reach high-lift forklift model, TWA also showcased its Armada Fleet Management System, which enables one operator to control six to 10 forklifts remotely.
The shared autonomy platform combines a fully automated forklift system with remote operations. This means if a robot has an issue, it asks for help and the remote operator can solve it from an office instead of a dangerous warehouse floor.
“By offering a solution that supports both fully autonomous forklifts and the ability for remote operators to take over when needed, Third Wave Automation can drive greater productivity at existing staffing levels, while improving safety and operational flexibility," says company founder and chief executive officer Arshan Poursohi,.
The TWA Reach can operate in 10 ft. (3 m) aisles up to 366 in. (9.3 m) high, moving products from staging lane to rack and back with no handoff to other systems or humans. The new autonomous TWA Extended Reach extends these capabilities by two times.
Atlanta-based Fortna tackled the typically labour-intensive process of consolidating and transporting small orders away from sortation systems at its MODEX stand.
The company launched Fortna OptiSweep, which uses Geek+ robots to collect orders from sorter divert locations and bring them to specially designed goods-to-person locations to deposit orders for bulk consolidation and outbound processes.
Fortna WCS software seamlessly orchestrates the workflow, managing the mobile robots and communicating with the sorter and consolidation stations to maximise efficiency and balance product flow.
FORTNA OptiSweep can replace both manual operations and legacy technologies such as the bombay sorter.
It eliminates the need for workers to bend and reach into bags to move items and substantially cuts the distance and time spent walking in the warehouse.
Omron Robotics and Safety Technologies used MODEX to launch its new autonomous mobile robots (AMRs) with lifter and roller modules from ROEQ.
A lifter top module enables an AMR to drive underneath the cargo, lift it up and transport it to the desired location, while a top roller makes sure that the cargo is seamlessly transferred from the AMR to a conveyor station, providing a fully-automated, efficient logistics cycle.
“Manufacturers are adopting AMR technology at a staggering rate as the world moves forward from the supply chain crisis inflicted by the pandemic and it’s never been more important to launch complete, out-of-the-box solutions accelerating production automation projects,” says Kyle Hable, group product manager, OMRON Robotics and Safety Technologies.
Omron’s mid-range AMRs, the MD-650 and MD-900, are now available in the US and Canada.
The Reshape platform has turnkey and customisable solutions
American startup Reshape Automation, meanwhile, is automating the automation process itself.
Targeting small and medium manufacturers and logistics enterprises, Reshape Automation’s platform guides manufacturers through a curated marketplace of top automation brands, products and turnkey solutions, eliminating the need for extensive research and vendor vetting.
Artificial intelligence (AI) agents are available to address questions and provide guidance.
"Manufacturers in the US are fighting an uphill battle with labour shortages,” says Reshape co-founder and chief technology officer Carlos Vanegas.
“We owe it to them to put the latest advances in AI to their service so that they can adopt automation as a low-risk and trustworthy ally to win that battle.
"Our AI agents act as a navigational aid throughout the manufacturer's automation journey, starting from the initial discovery and design phases.”
See other event highlights in our MODEX Gallery. Looking for a round up of developments and insights from this year's LogiMAT? Read our report here.