As forklifts are used in a growing range of applications, more of them are deployed in harsh conditions. These range from extreme temperatures to dusty environments and uneven surfaces.
To cope with these extreme conditions, a number of manufacturers have developed equipment that can withstand harsh environment and conditions. Here are some examples:
Jungheinrich Dusty Environment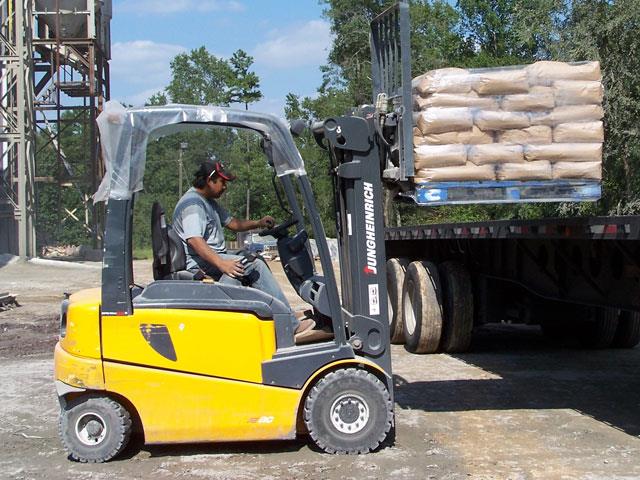 The Jungheinrich EFG 425K working at AW Cook. |
AW Cook Cement Products Inc of Hoschton, Georgia, has produced blended and special-order cement products for the US market for over 16 years. The privately owned company generates about USD50 million in annual sales and has 20,000 square feet (1,858 square metres) in plant area.
Prior to Jungheinrich forklifts, the company had been using 6,000lb (2,721.6kg) Clark and Daewoo LPG forklifts to manoeuvre and lift pallets of bagged cement ingredients and finished cement formulations that weighed about 3,000lbs (1,360.8kg). The pallets were lifted up to 15 feet (4.57 metres).
After AW Cook's forklift supplier closed, plant manager Mark Nations contacted Hoschton forklift dealer Complete Lift Service Incorporated.
Complete Lift sales representative Danny Andrews says AW Cook was dealing with a mixture of Georgia red clay, sand and concrete, clouds of dust, uneven floors, heavy loads and outdoor and indoor use of forklifts.
It doesn't get much worse than that, he says.
One day, Andrews drove an EFG 425K, 5,000lb (2,268.0kg) forklift to the plant. He left the 80 V, three-phase AC technology, four-wheel counterbalanced forklift with a 185-inch mast, for AW Cook to test.
Plant manager Nations called Andrews the next day and bought the forklift.
"It turns out the EFG had given his crew about 16 hours of work on a full charge, loading out 10 or 12 trailer truckloads of 2,800lb (1,270.1kg) pallets," Andrews says. "The loadmaster was actually refusing to use the old 6,000lb (2,721.6kg) LPGs again."
The air in a cement plant is full of powder and dust that can clog the motor in a DC truck or the engine radiation in an LPG truck. This can cause a forklift to overheat and break down, leading to loss in production and the expense of a service call. However, the three-phase AC motor in the Jungheinrich forklift is completely sealed from grit, powder and even moisture. Being sealed also means the forklift can be easily moved outdoors with no harmful effect to the motor from the elements.
The EFG 425K's components are encapsulated and thus protected to IP54 standard for heavy-duty applications in the dusty, dirty environment and outdoor conditions. The portal axle is fully integrated with the electrics, the AC drive motor is integrated in the axle and fully sealed and the differential as well as gears are integrated in the sealed axle. All connectors and lift and power steering motors are also sealed against dust and water.
Nations says the safety aspect of using an electric forklift over an LPG forklift clinched the deal for him. "No fuel tanks, which I consider dangerous, and no fumes."
HysterFreezer environment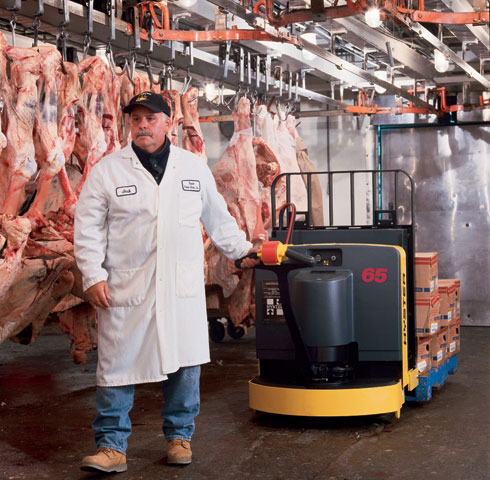 A Hyster walkie pallet truck in a cold room. |
Hyster Company says a major issue forklift manufacturers face is producing electric forklifts that can withstand cold storage/freezer environments where temperatures range from -40F to 32F (-40C to 0C) and perform in these conditions.
"One thing we learned is not all cold food warehouses are kept at the same temperature; certain foods require certain storage temperatures," says Hyster sales manager Bobby Hopkins.
In 2006, the US manufacturer released three environmental construction packages to meet the specific needs of the industry for selected class 1, 11 and 111 forklifts. The "cooler/freezer" (0F to 120F/17.8C to 48.9C) package was for high humidity or wet applications, the "subzero freezer" (-40F to 120F/-40C to 48.9C) package was for blast freezers and other sub-zero applications and an "extreme corrosion/washdown" (0F to 120F/17.8C to 48.9C) package for corrosive environments, food processing, pickling, tanning, salt and brine environments.
Hopkins says the key to a safe and productive operation in freezer environments is having forklift components that are not affected by cold or moisture - and protecting those components that may get affected.
The parts that need to be protected include electrical connections, system controllers and multiple switches. Some components may require special heaters to maintain their optimal operating range. When forklifts move from cold storage to warmer loading dock, Hopkins says a concern is moisture from condensation.
"We look towards sealed electrical connections, system controllers and other modifications to help facilitate these types of installations."
There is no special forklift driver training for the freezer application. However, operators need to understand and be familiar with the challenges of operating in a freezer application. They would be working with insulated work gloves that may limit hand and finger movement, wear extra layers or bulky clothing that could limit mobility and have ear muffs that may restrict hearing. They also need to brake smoothly and allow extra time for braking on a frozen surface due to potential for reduced traction. Finally, they need to be extra cautious when manoeuvring the truck in slippery conditions.
Nissan Cold and wet environmentAlatrade Foods LLC, which has poultry processing plants all over Alabama, recently acquired a Nissan walkie pallet truck that works round the clock, three shifts a day in temperatures averaging 42F (5.5C).
Mike Walker, plant manager at Alatrade, says it's not an easy environment for a forklift.
"It is wet, cold and extremely messy.
"The forklifts go in and out of trailers throughout the shifts and over dock plates, which is hard on the bearings."
Walker says he likes the fact that the Nissans are "heavier duty than the plant's previous forklifts".
The workers were unhappy with the old forklifts that weren't holding up. One of Alatrade's plant managers recommended the Nissan forklifts to Walker.
"The drivers like them better because they hold up better."
Walker says the forklifts had to be sprayed down at 900psi to be washed clean from all the muck that's in the poultry processing plant. The pallet trucks also have sealed switches to protect them from the cold and wet environment.
Forkliftaction.com News would like to thank Jungheinrich Lift Truck Corp, Hyster Company, Nissan Forklift Corp North America, AW Cook and Alatrade Foods LLC for contributing to this article.