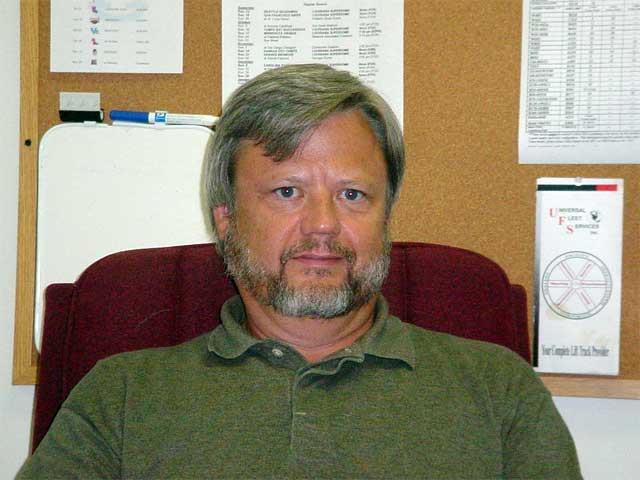 David deGruy ... insurance a motivator |
Safety product spending - a balancing act between the benefits and the bottom line
Innovative forklift safety products are continually being created and refined and are available worldwide at relatively reasonable cost. On the face of it, the benefits of these products would seem self-evident - especially the element of insurance against lost production or the expenses associated with accidents. But among end-users, this is not always the case, writes
BERNARD LEVY in the first part of this special report.
BROWSE through the sales catalogue of any major forklift supplier and the range of products can generally, and quite fairly, be described as mind-boggling, given the sheer volume and variety on offer.
Items in their thousands are listed and/or illustrated, ranging from brand new forklift trucks in different sizes and capacities, to a virtual galaxy of accessories and spare parts often running into the many tens of thousands.
Peppered among these awesome selections are products designed to improve and maintain forklift workplace health and safety - but which almost invariably account for just a miniscule fraction of total sales.
Why? According to key industry players such as suppliers, fleet managers and trainers, while end-users are the ultimate target of the push for tougher workplace safety standards, there is lingering resistance in some quarters to allocating money from equipment budgets to purchase safety products.
The reasons are manifold, but chiefly, it's an issue that boils down to justifying the expense in an atmosphere of uncertainty about the return on the investment in real or measurable terms - in essence, how to explain the cash outlay and potential benefits to senior management or the board.
Regular equipment servicingTony Stewart, engineering services manager in the building and engineering department of leading UK-based haulage and distribution group, Wincanton, said good maintenance practice was as important as buying new safety products.
"Maintentance of equipment is an issue Wincanton considers very carefully in relation to safety, but that is not the case across the board in industry," Stewart said.
"We have a policy that all our warehouse equipment, including our forklifts, is serviced at a minimum of every three months.
"This is more often than the period that most forklift manufacturers and others recommend in most cases and is designed to ensure that the condition of every vehicle is maintained at the very highest level at all times."
Ranked among Europe's top three supply-chain groups servicing retail and wholesale outlets in 15 countries throughout the UK, the EU and parts of Eastern Europe, Wincanton generated turnover of almost GBP1.7 billion (USD3.1 billion) to produce an adjusted operating profit of GBP43.2 million (USD78.8 million) in 2003.
Employing 25,000 people and with 1.9 million square metres of warehousing space, the company operates 5200 on-road distribution vehicles and more than 3000 pieces of powered equipment, including counterbalance forklifts, pallet trucks and order pickers.
Stewart said other issues that had significant impacts on the rate of injury and death in the forklift industry were training and the calibre of staff employed to drive forklifts.
"With training, we comply with the UK's RTITB (Road Transport Industry Training Board) standard for all our operators," he said.
"But the reality is that warehouse operators are not all that highly paid so this can affect the calibre of the person operating machinery such as a forklift.
"In some cases where you have a person at the low end of the scale, this is really not the ideal person to be putting behind the wheel of a high-value piece of equipment.
"But unfortunately, that's the nature of the warehousing business."
Stability controllers importantStewart said Wincanton used a wide range of standard, as well as more innovative, safety products to overcome variations in the level of operator competence.
The newer products complemented the more standard safety range such as beacons, reversing beepers, height indicators, load indicators and others.
He said stability controllers played an important role in improving safety and the forklifts Wincanton purchased from Sweden's Atlet and the UK's BT Rolatruc were delivered with the device installed.
"Basically, these take the control away from the driver and slow the fork truck down when they're going too fast around a corner," he said.
Another device the company had fitted to its forklifts to improve safety was an electronic logging unit.
"The system replaces the standard key and either has a keypad or proximity card reader which controls who can and cannot log on to drive a fork truck," Stewart said.
"It ensures only trained and approved operators can drive our trucks."
Improved safety levels had also been achieved by installing cameras capable of looking down the fork - especially helpful when operators were picking up pallets at height.
Wincanton, along with other major distribution companies, is presently trialling a new reach truck from Linde that provides significantly improved visibility for the driver.
In the prototype stage, the new machine has a completely different mast configuration to older model reach trucks and is scheduled for release mid-2005.
Increased insurance costsDavid deGruy, president of Alabama-based Universal Fleet Services (UFS), which specialises in forklift and rolling stock procurement and management for Fortune 1000 companies, said forklift safety had increased in importance because of the increase in insurance costs and the number of accidents, as well as the availability of safety options for forklift equipment.
"OSHA (Occupational Safety & Health Administration) driver training requirements have also further increased awareness of forklift safety," he said.
"Virtually all large companies today have some variation of a safety program built into their equipment specification packages, for example, fire extinguishers, back-up alarms, etc.
"The bottom line here is to spend money intelligently.
"There are many products on the market that can make an operation safer when correctly employed, but management policies and practices are just as essential.
Management role"For instance, installing impact sensors on equipment is costly, but yields no return unless management is willing to take appropriate action relative to the repeat offenses," DeGruy said.
"Operating areas should also be kept clean of debris such as boards, pallets, paper and oil.
"Simple housekeeping issues are often overlooked but can be a high contributor to accident prevention."
DeGruy said the safety regulations set forth by the American National Standards Institute (ANSI) and OSHA were now far better than they were several years ago, but were still the bare minimum for an effective program.
"Additionally, cultures need to be changed," deGruy said.
"Operators need to be fully trained and pedestrians need to understand they are also 'responsible' for their own safety.
"As the old saying goes: 'Safety is an attitude'.
"Currently, there is 50% bonus depreciation for equipment delivered prior to year-end.
"But, investment in safety and safety equipment can return savings in many areas - reduced product damage, lower insurance costs, reduced building damage and reduced forklift damage are only a few."
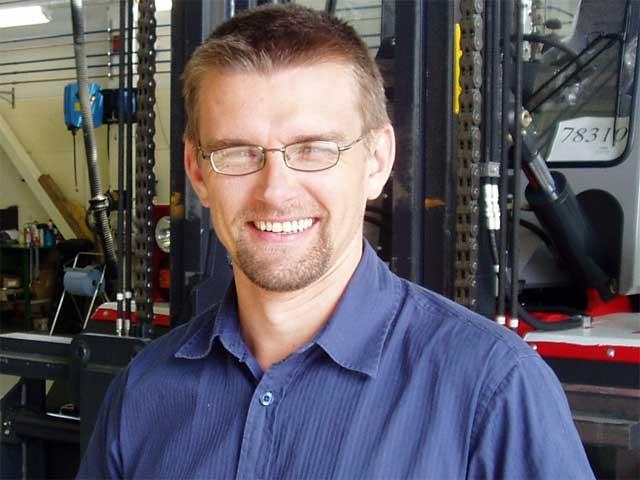 Hakan Larsson ... at the forefront |
Northern Europeans 'pioneers'Design manager for medium-range forklifts at Kalmar Industries in Sweden, Hakan Larsson, said that like other companies, Kalmar had been in the forefront of developing new and safer equipment for many years.
An example was the Kalmar DCE range, which featured a new counterweight mast and cabinet that provided better visibility, making forklift operation safer.
The company had already released 9-18-tonne models of the DCE, and lighter models in the 5-9-tonne range would go into production soon.
"Another important product from the safety point of view is our turnable driver position within the cabin itself," Larsson said.
"Being able to turn the whole seat, the steering wheel and the pedals as one unit means you can gain better visibility for a load that is difficult to see from a front-on direction.
"This innovation is similar to our levelling cabin which can be raised and lowered by a mast at the back of the machine, allowing better visibility for certain loads like a large tub of molten metal that needs to be poured accurately."
Larsson said it was clear that companies were now spending more on safety products and features.
"The figure is increasing as companies see the benefits of applying safety products," he said.
"The northern European and Nordic countries have been pioneers in this area and other nations and regions are catching up.
"Developing countries in place like Africa are not at the level of Europe, but they getting there gradually.
"The issue really comes down to how much extra companies are prepared to spend to add safety features to machines, above and beyond the requirements of the regulations.
"The percentage increase in cost to add the safety features can be quite considerable on a small machine, but for a larger machine, relatively speaking it's not such a big amount."
Universal Fleet Services' David deGruy was more specific.
"Our estimate of product safety expense would involve both equipment and operator categories," he said.
"I would estimated safety-related expenses for each new unit delivered today would average approximately USD1200.
"Safety-related expenses for each lift truck operator would be about USD1000 annually."
Lip-service to safetyTVH Australasia's general manager, sales and marketing, Rob Whitmore said that in his experience, some companies had a corporate culture that tended to pay lip-service to safety, sometimes skimping in replacing faulty equipment or parts.
"This could take the form of replacing a reversing beeper, adding a seatbelt to a seat, replacing a seat when it's worn, or other products that overall enhance the safety of a forklift," he said.
"Over the years, I've seen examples where company cars get serviced without hesitation, but when somebody calls for a piece of safety equipment, lots of questions are asked.
"As a result, shortcuts may be taken - and that could involve anything from a simple piece of lifting equipment to a worn fork tyne that needs replacement, etc."
Whitmore said that while there was a major focus today on reducing lost-time injury, even simple things like replacing a worn seat sometimes did not receive the sort of priority it deserved.
"If a seat gets torn, exposing damaged springs or bits of jagged metal, that seat can be replaced inexpensively for around USD100 rather than being re-covered," he said.
"People may not consider that necessarily a safety issue.
"But an operator with his leg torn open is going to cost the company time in the workplace, and potentially, a huge compensation claim."
Safety seen as expenditureMichael Riley, state training manager with Asia-Pacific freight and express parcel distribution company Toll IPEC, said an inhibiting factor in the purchase of more forklift safety products was that some companies' occupational health and safety departments were not allocated their own specific budget.
"Occupational health and safety is seen by some companies as an expenditure, so money is spent on safety products or maintenance on an ad hoc basis," he said.
"These departments have to argue for every safety dollar, so that's not really conducive to adopting a proactive company approach to workplace safety as a whole."
Riley said that during some company assessments, he had observed apathy among supervisors monitoring forklift activity.
"Rather than having a consultative approach with operators, they might turn a blind eye to issues such as speed or not wearing seat belts, particularly on counterbalance forklifts," he said.
Other important issues impacting on workplace safety included insufficient or infrequent pre-operational checks on equipment, sloppy practices while loading and unloading in the back of trailers and using lower-quality and non-approved pallets in multi-storeyed rack structures.
"Companies should be using high-standard Chep or Loscom pallets, which are designed to lock to the racking.
"Some businesses tend to use plain pallets or 'skids' which can easily be unbalanced and spill their loads - especially if the rack they are being stacked onto is accidentally bumped during the loading."
Riley said the use of unapproved pallets often resulted from ignorance about the potential dangers.
"My experience is that people high up in an organisation may understand the safety issues, but these are not effectively communicated down the chain of command," he said.
"But it has to be said forklift operators are quite accommodating when presented with new safety obligations and responsibilities, even though these represent an extra work load.
"They'll generally work with the system rather than against it."