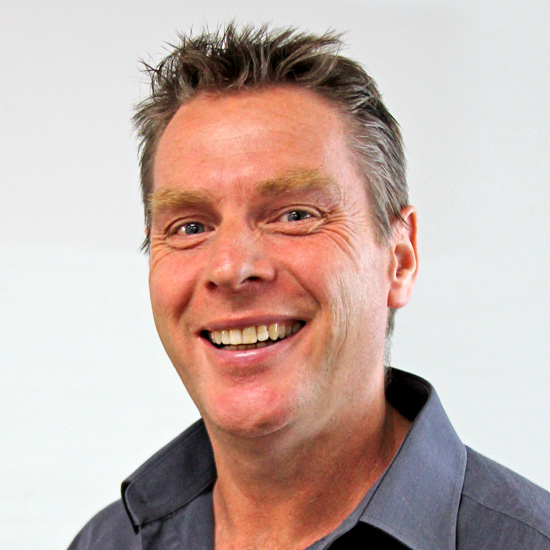 Grahame Don |
Grahame Don is Senior Business Development Manager - Industrial at RCT and is based in Melbourne, Australia. Don has extensive experience in sales and client relations in the Australian Materials Handling sector and joined RCT as Account Manager in 2014 before moving into his current role.
1. Brand-agnostic Fleet Management SystemsData is becoming an increasingly important tool to enable managers to make more informed decisions throughout many areas of the workplace. Fleet management systems (FMS) assist in providing data in relation to mobile plant: information which is often used to better manage fleet size and maintenance by monitoring utilisation. Other features can assist with compliance, training and safety. Especially if you have a business that runs a variety of equipment from different suppliers, I'd recommend a brand-agnostic FMS. This will spare the administration of different FMS platforms and the cost of combining data from different FMSs that often use different units of measurement.
2. Manage operator accessA common feature of a FMS is the ability to control who operates your equipment and which equipment they can operate. Some include the ability to conduct check lists and combine with additional features such as speed zoning. Ideally, the FMS should be capable of operating on a range of equipment. For example, in a warehouse environment, forklifts, order pickers, sweepers and burden carriers ideally could use a common platform, that is capable of being used across multiple sites, even multiple countries, regardless of the original equipment manufacturer (OEM) brand.
3. Out-of-service reportingUnderstanding why your fleet isn't working can be just as important as knowing what is working. When considering fleet management products, consider systems that enable you to understand your downtime. Is it always the same piece of plant? Is the downtime planned? Understanding more about this aspect can assist in better planning of maintenance, asset planning and cost management.
4. GPS zoningGPS speed zoning is a readily available feature which provides a geofencing solution for equipment that requires strict speed controls within specific areas of various industrial operations. In conjunction with speed limiter devices, logistics managers can preprogram specific speed settings for different types of equipment based on any number of unique requirements of the operations. For example, counterbalance forklifts can be programmed for a certain slow speed when operating inside an air freight handling warehouse or in an area where you can expect pedestrians. But if that forklift ventures out onto the tarmac for any reason, it can enter a separate zone and then operators will have different factors to contend with and have access to higher speeds. This sort of feature is more suitable for more spread out, open sites and is very flexible as managers can alter zone parameters easily.
5. Safety devicesInstalling simple pieces of equipment such as safety lighting is a cost-effective way to protect warehouse personnel and meet Occupation Health and Safety rules. Halo zones and smartspots awareness technology take the form of lighting beams specifically designed to be fitted onto machinery and project a visual caution mark onto the floor of your warehouse. This alerts people and other machine users nearby that a vehicle is approaching and that they should move to a safe area. Safety features like these are becoming an increasingly important part of industrial operations.