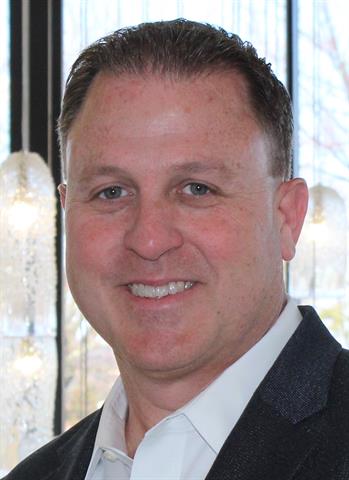 Shawn O'Connell |
Shawn O'Connell is president, Motive Power Americas for EnerSys, a global leader in stored energy solutions for industrial applications.
What do materials handlers want from their forklifts?At EnerSys, we work directly with forklift end-users and manufacturers, and we hear both groups answer that question in the same way: today's materials handlers want forklifts that are more reliable and less maintenance-intense. They want smarter, more connected vehicles that can deliver a better user experience - one that's more hands-off, with less downtime and a lower total cost of ownership (TCO).
Giving customers what they want and need will involve advances in forklift and battery design, but it will also require better communication and integration between vehicles and their power arrangements. Achieving that will require more communication and integration between forklift and battery manufacturers.
New product development roadmaps aheadIn a previous life, I served for many years in our Reserve Power business, working with Original Equipment Manufacturers (OEMs) serving Uninterruptible Power Supply (UPS) customers - large data centres, utilities and other mission-critical applications. Together, we worked very closely on systems that would deliver smarter, more connected end-user experiences.
Doing the same for materials handling vehicles calls for a similar approach. In part, that's due to the adoption of open source communication software and CAN (Controller Area Network) bus interfaces. To ensure that battery and charger systems can effectively "talk" to the vehicles through these tools, battery and forklift manufacturers will need to interact sooner in our respective product development cycles and get our product development roadmaps more closely aligned.
With all of that in mind, let me share where some of our recent product development roadmaps have already taken us and where some others are headed soon.
Thin Plate Pure Lead (TPPL) and lithium-ion (Li-ion) batteriesRising real estate and labour costs have materials handlers looking for ways to cut expenses and boost productivity, which in turn is driving demand for lower maintenance forklifts. Technologies such as Thin Plate Pure Lead (TPPL) and lithium-ion (Li-ion) can help.
Both TPPL and Li-ion batteries eliminate watering requirements and enable fast, effective opportunity charging. No watering means less labour and no risk of spills. Opportunity charging means no more battery changing and changing rooms, further reducing labour while freeing up valuable floorspace for revenue-generating activities.
TPPL and Li-ion battery solutions also provide different power options to best meet operational and cost requirements. For a fleet handling light- or medium-duty applications, TPPL batteries will provide the necessary power at a lower cost than Li-ion. For a fleet facing medium- to heavy-duty applications, Li-ion may be a better option.
Wireless charging and predictive battery managementWireless battery charging systems will also free up floorspace by eliminating the need for dedicated charging rooms. Labour demands will shrink too, as operators won't have to plug or unplug batteries - instead, they'll just drive the truck over a location on the floor
where a unit installed beneath it will automatically charge the battery. Enabled by the
CAN-bus interfaces and software I mentioned, the charger will "talk" to the truck and battery to help ensure a safe operation.
That same data communication has paved the way for battery management systems (BMS) with robust condition-monitoring and predictive analytics capabilities. Operators in the warehouse, or even in remote service locations, can now monitor the power system and often detect emerging problems
before they result in costly unplanned downtime or lost batteries. The battery operating data can also be used to analyse a fleet's overall power use, workflow and more, providing insights that can optimise the power solution.
Technologies converging in Automated Guided Vehicles (AGVs)TPPL batteries and predictive BMS are already part of the EnerSys product portfolio for materials handling, while Li-ion batteries and wireless charging solutions will be soon. In the not-too-distant future, we see all of these technologies converging to make Automated Guided Vehicles (AGVs) more cost-effective and user-friendly too.
AGVs already allow employees to focus on other tasks. Now imagine AGVs operating with virtually maintenance-free batteries, wireless chargers and predictive battery management systems. These already "hands-off" vehicles will become even more user-friendly as warehouse employees won't have to manually charge or even monitor charging anymore, or perform battery maintenance checks of any kind.
Powering tomorrow's fleets togetherThe potential for all of these technologies to come together and transform user vehicle experiences and boost warehouse productivity is here. Fully realising it, however, means companies like EnerSys will have to work with vehicle OEMs more closely than ever.
Gone are the days when we could just supply batteries based on a few performance specs. Powering tomorrow's warehouse vehicle fleets will require us to interact earlier and
more fully in our respective product development cycles. Ultimately, advancing technologies and evolving demands for better user experiences are driving changes behind the scenes that will be just as dramatic as anything on the warehouse floor.