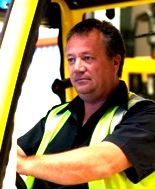 Steve Yates |
Steve Yates, motive power product specialist, has been with Applied Engineering Technologies (AET) since 2010, when his battery company, Amps was acquired by Adaptalift Hyster. Steve has had previous experience as a forklift technician, service manager and state manager at various materials handling companies.
Battery-powered industrial forklifts are used in a variety of applications and are becoming increasingly popular. These days, the benefits of battery electrics include longer running times, shorter recharging times and reduced emissions.
Battery electric forklifts range from small, motorised pallet trucks to much larger forklifts. Regardless of which battery electric forklift you have, there are similar hazards associated with batteries.
Battery HazardsTwo types of batteries are commonly utilised in industrial forklifts: lead acid and nickel-iron. Both of these batteries can pose health and safety hazards. This is mainly due to three factors: the sheer weight of the batteries, the gases emitted during charging (which can be highly volatile) and the corrosive chemicals that exist within the battery itself.
Due to these hazards, it is important that battery changing stations and employees are equipped with the right safety equipment in order to minimise any risks of danger.
Workplaces must have safety procedures in place in order to deal with any dangerous situations that may occur.
Here are a few safety tips to follow when changing your forklift's battery:
1. Any employees engaging in the changing or charging of batteries should always wear protective clothing.
2. Forklifts should be in a stationary position with the handbrake on and engine off before attempting to change the battery.
3. Battery-charging installations should occur in designated areas.
4. The designated installation area should be a smoke-free zone, with signs clearly indicating this.
5. In order to keep this area safe, facilities should be provided for flushing and neutralising spilled electrolyte, fire protection, the protection of charging equipment and the adequate ventilation for dispersal of fumes from gassing batteries.
6. A conveyor, overhead hoist or equivalent materials handling equipment should be available for handling batteries.
7. Vent captions should be checked to ensure they are fully functioning. The battery (or compartment) cover(s) should be open to dissipate heat.
8. Provide a carboy tilter or siphon for handling electrolyte.
9. Ensure that reinstalled batteries are properly positioned and secure in the forklift before operating the equipment.
10. Precautions must be taken to prevent open flames, sparks or electric arcs in battery-charging areas.
11. Tools and other metallic objects must never be left on top of uncovered batteries.
When dealing with forklift batteries, it is extremely important to change and charge them safely. These objects can be very hazardous if they are not dealt with in an appropriate manner. Safety procedures should always be followed to avoid any preventable work place accidents.