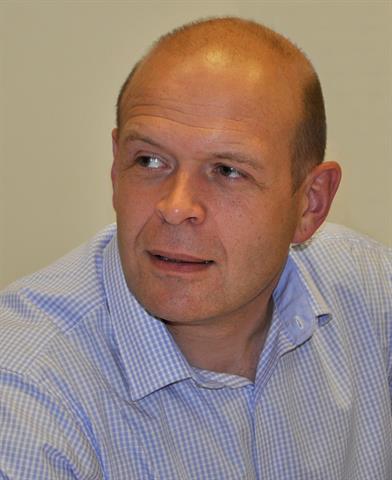 Stuart Taylor |
Stuart Taylor is Managing Director of Mentor FLT Training Limited, the UK's leading provider of training and associated services for all types of materials handling equipment and workplace transport.
Many businesses that rely on forklift trucks see fluctuations in demand that require them to take on additional staff. But, when recruiting, it's important to remember the impact that an influx of new starters can have on a site's accident risk.
Research shows that, on average, new workers are just as likely to get injured during their first six months in a new job as they are during the entire rest of their working life.
This means they're more than three times as likely to have an accident in that first six months than someone who's been in the job for five years.
Why is this?Well, these accidents often arise when the worker lacks experience in the role and/or familiarity with the work environment. As a result, they may have trouble spotting hazards; they may not be used to the controls of the equipment; they may be unfamiliar with site layout and safety measures; and they may have picked up bad habits in their previous role.
Of course, these accidents don't always result in injuries, but the costs and disruption associated with dropped pallets, dented racking and damaged trucks can still cause serious issues, particularly at your busiest times of year.
Get the most from your new employeesThe benefits of taking on those extra members of staff can be quickly lost if your increased productivity is cancelled out by increased disruption. To get the best value from your new employees, you need to make certain they have the specific skills and knowledge they need to become a safe and effective part of the team.
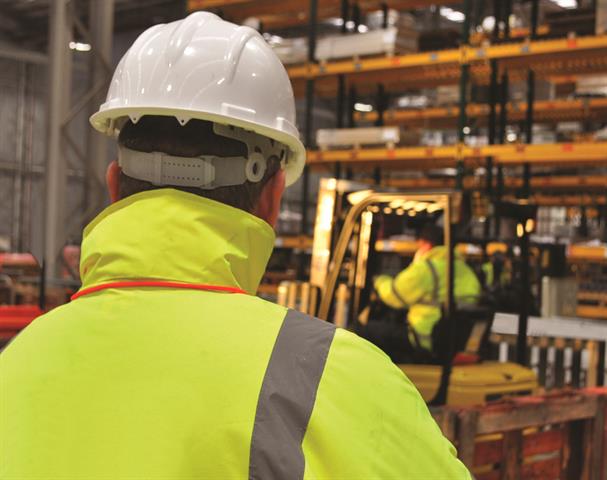 New workers are more than three times as likely to have an accident in that first six months |
A vital first step is evaluating the skills and knowledge of all new staff and checking their documentation is valid. You need to establish what - if any - accredited training they have recently received, and how closely they follow best practice, so you know exactly what training they'll need before using equipment.
The best way to ensure your new operators are safe and ready for work is to ensure they have undertaken all three required elements of training outlined in the
Approved Code of Practice, L117: basic training, specific job and familiarisation.
Considering their training needs does more than keep workers safe or minimise disruption; it ensures you comply with the law, too.
The HSE's definitive guidance on forklift operations - L117 Approved Code of Practice for Rider-Operated Lift Trucks - makes clear the need for proper training and supervision of all staff, including new starters.
And remember, it's not just operators who need training. You may employ seasonal staff who have never worked with or alongside forklifts. They won't be aware of the associated dangers... and yet, it's these pedestrians at the greatest risk of injury. HSE statistics show that 57% of those injured in forklift accidents were on foot at the time of impact.
Giving staff proper training will not only provide the skills they need, but also the confidence to stick to best practice and a full understanding of the potential consequences if they don't.
Training shows staff that you take safety seriously and that their welfare is valued, even if they're only with you for a while. A safe working environment has a positive impact on staff morale, and that, in turn, can have a positive impact on productivity.
After all, the better prepared your new starters are to start work safely, the more seamless their integration into your team, which ultimately benefits them, their colleagues, and your bottom line.