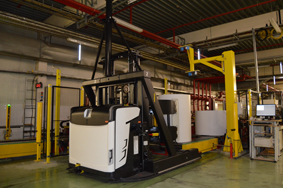 Investment in Rocla automated guided vehicles pays for itself after two to three years. |
Rolls of paper weighing up to 5000 kilos are transported using Rocla's Automated Guided Vehicles (AGVs) at the Sappi Alfeld GmbH paper mill in Alfeld, south of Hanover in Germany in the Niedersachsen region. This transport system, with its total of three vehicles, was commissioned in 2011.Transporting the paper rolls requires precision and meticulous work as the rolls can easily be damaged. This is why Sappi Alfeld decided to go for
Rocla's AGVs and the
MetRo warehouse management system (WMS). The MetRo WMS was developed jointly by Metsys and Rocla, and it is responsible for the management of the storage locations and allocation of transport requests to the AGV control system. The dynamic storage strategy is adapted to the needs of customers by means of the production data.
The
AGV operating area is lit only dimly, thereby saving on additional costs. No additional light source is required for operation of the AGVs. The vehicles find their way around by means of the reflectors secured to the walls and supporting beams in the warehouse. A rotating laser detects the distances to the reflectors and calculates its position by means of triangulation.
Manfred Rohling, departmental manager for this area, is very pleased with the performance and efficiency of the
AGV and the
MetRo WMS. "The vehicles operate reliably and do not take breaks. Not one roll has been damaged since they were commissioned, nor have we had to search for one."
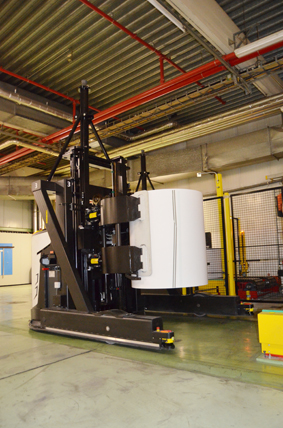 Rocla AGVs are very stable and can carry a load of up to five tonnes. |
Efficient and safe"Automated Guided Vehicles move more slowly than conventional forklift trucks," says Manfred Rohling, "but because they work constantly, they are generally more efficient than their predecessors."
One significant aspect is the safety offered by the AGVs. "We have had no accidents with the vehicles to date," says Manfred Rohling, standing in front of one of machines to demonstrate. With this, he shows how the vehicles recognice their surroundings and detect obstacles promptly: the vehicle comes to a standstill five centimetres away from his foot. When its route is clear again, continues on its journey.
The routes of these driverless transport vehicles are stored on each individual vehicle. Transport logic calculates the optimum route for a transport job, taking into account the origin, the destination and the position and status of each individual vehicle in the system. If another vehicle blocks the optimum route unexpectedly, an alternative route is selected.
Transport jobs can be assigned from all operator terminalsThe scope of supply for the entire system at Sappi included the
MetRo warehouse management system (WMS) and the
AGV system. There are interfaces to the existing roll conveyor system and the Sappi Mill Execution System (MES). A data interface provides the WMS with the master data for the rolls and the production data in order to create a process-related warehouse strategy.
This interface allows possible changes in production planning to be forwarded directly to the WMS and thus be taken into account when creating the warehouse strategy. Transport jobs can be altered right up until the time they are executed. The AGV control system constantly checks the optimum conditions for a transport job, so a job can be transferred from one vehicle to another just before the roll is picked up.
The system can be monitored via an operator interface at the control centre. The interface shows a graphic display of the warehouse, indicating the position and status of the vehicles in real time. Operators also have access to the WMS and the AGV job buffer. The system can be accessed here according to their user rights. It is possible to generate jobs, cancel jobs and assign different priorities to jobs. Areas in the warehouse can also be blocked so that maintenance work can be carried out. Precise information is also provided on stock status, system status, performance and statistics.
Minimal maintenance requiredSappi has a maintenance contract. Annual maintenance and repairs are carried out by a Rocla partner company. Some servicing measures are also carried out by Sappi itself. A detailed system and maintenance training allow staff to remedy minor issues themselves without problems. There have been no major repair requirements to date.
"Occasionally we find ourselves in situations in which we have to contact the 24-hour
Rocla Customer Service team so that we can rectify any potential problems together. But if a problem cannot be resolved in this way, our maintenance agreement requires a Rocla specialist to turn up on site promptly. That said, we are constantly attempting to learn more about the servicing of our transport vehicles," says Manfred Rohling.
Sappi also carries out battery maintenance itself. These are open lead-acid batteries weighing more than a tonne. Battery watering and compensation charging are all part of the regular maintenance to be carried out. Despite the fact that the vehicles are used to transport rolls of paper weighing up to five tonnes, the batteries have enough power to last about twelve hours. The batteries are charged at a station and are swapped manually by means of roller conveyors. The current batteries are the ones originally supplied, and they can still be fully charged even after two years of operation.
Two driverless transport vehicles are actually sufficient to meet the current needs of the Sappi Alfeld plant. However, according to Manfred Rohling the third vehicle ensures that transport can continue to take place smoothly; this is because the vehicles do not have to operate constantly, thereby easing their burden.
"This ensures a longer service life for our machines," says Manfred Rohling. "At our company, we like to take the long-term view."
Sappi GmbH in figuresThe
Sappi Alfeld GmbH plant manufactures a range of special papers, from a lightweight 17-gram paper to heavy 400-gram cardboard. The paper is produced from local raw materials using five paper machines. The plant, which is located south of Hanover on the river Leine, employs around 900 people working a three-shift pattern and has a proud history dating back 350 years.
The Sappi GmbH Group has a presence on three continents and manufactures both paper and cellulose. The group produces 6 million tonnes of paper per year. With its output of 3.5 million tonnes per year, the group is the biggest in the world when it comes to manufacturing cellulose. It employs 13,700 people in 20 countries.
For more information on Rocla's comprehensive AGV solutions please visit www.rocla-agv.comROCLA SOLUTIONS OYEmail: Send a message
Web: www.rocla-agv.comAGV Sales: +358 20 7781 332
AGV Services: +358 20 7781 312
P.O. Box 88,
FI-04401 Järvenpää,
FINLAND
Visit the Rocla ShopFront