Forklifts will play a key role in the development of radio frequency identification (RFID) technology. Raymond Corporation and Crown Equipment Corporation are among the forklift manufacturers with high interest in RFID. Other companies like International Paper Smart Packaging and LXE Inc are developing forklift-based RFID readers. Roger Renstrom and Christine Liew report. At the RFID Living Lab in the Connect Logistics warehouse in Edmonton, Canada, Raymond is working with Tibbett & Britten Americas, Toronto, Canada, IconNicholson, New York, and Econorack Group, Mississauga, Canada, on an RFID project. The RFID evaluation effort began in late 2003 and is set to continue for an undefined period. The goal of the project? To measure RFID technology in a macro sense. The project includes equipping and testing RFID on Raymond forklifts, pallets, carton storage locations and dock doors used in the warehouse, which handles logistics for the Alberta Gaming & Liquor Commission.
Raymond spokesman Kevin Trenga said the joint venture helped to assess the value, productivity and return on investment of RFID in the materials handling world.
"RFID requires no physical contact between the pallet or case and the scanning device. That means lift truck operators do not have to dismount or otherwise expend effort and time to record the receipt, movement or placement of loads," Trenga said.
Crown maintains it has interest in RFID but would not disclose details of its pursuit of the technology.
"RFID will have increased importance to the materials handling industry in the near term," a Crown spokesman said. "As a result, the value of RFID and its return on investment for the industry is something that we continue to evaluate with great interest."
What is RFID?The first RFID deployment in the US industry was at General Motors in 1984, said ESYNC's principal John Hill in an RFID article in MHIA's spring 2004 newsletter. Tags were attached to chassis carriers and served as licence plates that, when read, triggered just-in-time delivery of appropriate components for a given vehicle to the assembly line.
Since then, RIFD has been deployed in hundreds of applications where environmental constraints or the absence of line-of-sight access to tags precluded the use of barcoding.
RFID works like a barcode but with significant differences and advantages. The non-line-of-sight and non-contact nature of the technology allow tags to be read through a variety of substances such as snow, fog, ice, paint and other visually and environmentally challenging conditions where barcodes or other optically read technologies would be useless.
For example, in the automotive industry, RFID systems are used to track vehicles through assembly where tags must perform even after repeated subjection to temperatures of 150 to 200 degrees Celsius and being painted. A main objective for the use of RFID in that environment was verification of a vehicle's identity before execution of given assembly tasks.
Although costlier than the barcode, RFID has become indispensable for a range of automated data collection and identification applications that would not be possible otherwise.
Forklift-mounted RFID readersA basic RFID system consists of three components: an antenna, a transceiver (with decoder) and an RFID tag. The antenna emits radio signals to activate the tag. Antennas are the conduits between the transceiver and the tag. They are available in different shapes and sizes and can be mounted or built into different surfaces. For example, they can be mounted on a toll booth to monitor traffic passing on a highway.
The antenna is often packaged with the transceiver and decoder to become a reader, which can be configured as a hand-held or fixed-mount device. LXE Inc is developing a forklift-based RFID reader that could save users money.
LXE director of product management Dick Sorenson told
Frontline Solutions magazine how.
"With a portal-based solution, a company may have to outfit 100 dock doors with readers. From an economic standpoint, there are tremendous savings if they only had to outfit 10 or 15 forklifts," Sorenson said.
The reader emits radio waves and, when an RFID tag passes through the electromagnetic zone produced by the antenna, the reader's activation signal is detected. The reader decodes the data encoded in the tag's silicon chip and the data is passed to a host computer for processing.
LXE has teamed with Sirit and Intel to develop forklift-mounted readers. LXE and Sirit previously collaborated to develop LXE's hand-held RFID readers.
Sorenson said readers would most likely be integrated with the moving part of the lift truck to read location tags on multi-storey rack shelving. Engineering challenges arising from that include protecting the reader from shock and vibration, providing power to the reader from the cab and configuring the antennas to avoid interference.
Vehicle-mounted readers, used in conjunction with RFID pallet and location tags can improve efficiency and provide additional visibility in a warehouse.
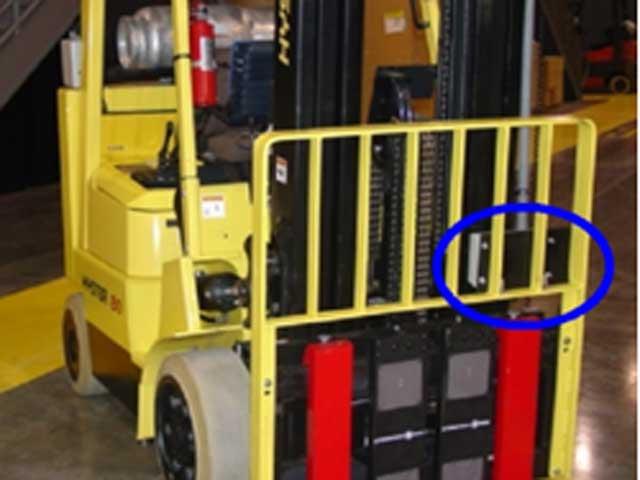 IP Smart Packaging's forklift-mounted RFID reader (in circle) |
Meanwhile, International Paper (IP) Smart Packaging, the RFID products and services provider and systems integrator that is part of global paper and forest products company International Paper, has announced it is offering the first commercially available RFID reader system mounted on a forklift. The RFID-enabled forklift could be used to track RFID-tagged products like cases and pallets as they move through warehouses and loading areas.
According to
RFID Journal magazine, companies can buy a complete forklift with the reader already installed from IP Smart Packaging or they can purchase a new forklift through one of two forklift manufacturers whom IP Smart Packaging has developed an agreement with. The names of the manufacturers are confidential but if a company already had forklifts that it wanted to use to track tagged products, IP Smart Packaging would retrofit the vehicles with readers, antennas and cabling.
Like LXE, IP Smart Packaging is finding durability is the key to functionality of forklift-mounted readers. Hence IP Smart Packaging has developed special impact-resistant antennas to be deployed on forklifts and has partnered with other RFID equipment manufacturers to develop "ruggedized" readers. The reader and antenna are designed to withstand the vibrations and impacts forklifts are subjected to in a warehouse environment.
Closed-loop applicationsMHIA executive vice president of professional development Dr Richard Ward said RFID applications in closed-loop manufacturing had existed for years.
RFID Journal reported International Paper had been using RFID-enabled forklifts, equipped with clamps to lift and transport tagged rolls of paper products, for the past two years. It has been doing so in its own operations and is currently using 20 such trucks at its paper mill in Texarkana, Texas. So far, readers on those trucks have captured 5 million electronic product code (EPC) reads.
Other manufacturers monitor tagged trays or totes circulating in a closed-loop facility.
John Hill said in the MHIA spring 2004 newsletter, that, to date, RFID had been deployed in controlled applications (closed-loop) where benefits for the user were relatively easy to quantify. However, the instant an RFID-tagged item left a domain, the levels of complexity and associated costs were compounded.
Problems emerge in open-loop systems where different and sometimes conflicting RFID equipment used by multiple retailers, retail suppliers and other supply chain users make it problematic to facilitate tracking from suppliers to retailer. "Folks are still looking and piloting open-loop systems," Dr Ward said.
Deloitte Consulting LLP's global RFID technology integration lead consultant John Greaves said numerous forklift makers had attempted to solve issues about the use of forklift-mounted RFID readers in open-loop systems.
"Even if one succeeds, the process of passing the amended truck specifications past Occupational Safety & Health Administration, your insurers, the union representative, and the significant discovery process in the software and forklift truck interface, lead me to believe that a pioneer of extraordinary resolve and budget will be needed."
The Association for Automatic Identification & Mobility (AIM), is more optimistic:
"It is highly unlikely that the technology will ultimately replace barcode - even with the inevitable reduction in raw materials coupled with economies of scale, the integrated circuit in an RFID tag will never be as cost-effective as a barcode label. However, RFID will continue to grow in its established niches where barcode or other optical technologies are not effective.
If some standards commonality is achieved - whereby RFID equipment from different manufacturers can be used interchangeably - the market will very likely grow exponentially."