Growing market demands on speed and load capacity call for new methods in the design of drive and load wheels with VULKOLLAN
® tread.
Constantly growing demands on speed and load capacity in materials handling: For decades, the high-performance elastomer VULKOLLAN
® has been the
industry's favourite high-quality wheel material for demanding materials handling applications. However nowadays, with
ever-growing market requirements, even the best VULKOLLAN
® quality is sometimes not sufficient to ensure the availability of equipments and appliances in intralogistics.
It is our aim to continue using the tried and tested VULKOLLAN
® as a
standard material. Therefore today, at RAEDER-VOGEL
®, we study the
interaction between wheel tread and wheel centre. The use of innovative wheel centre geometries, such as the
HSHL® (
High
Speed
High
Load
®) design, demonstrably increases the service life of wheels by up to 29 %.
Due to extreme demands on load capacity and more and more also speed of industrial trucks, customers report increased wear and even premature failure of VULKOLLAN
® wheels. Most users try to fight these problems by over-dimensioning or - if this is not possible due to the fact that the space for fitting the wheels is growing smaller and smaller - by replacing the wheels more frequently. Selecting a different wheel material is often only possible for niche applications. Therefore, if equipment availability and life-cycle-costs are taken into consideration, it becomes imperative to
redesign the wheels.
The material of choice for materials handling: 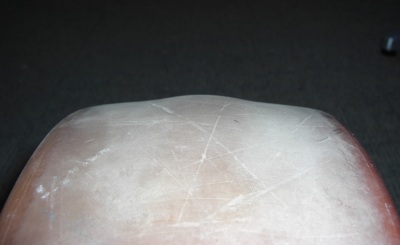 Typical damage: Axial displacement of the wheel tread while the wheels is externally intact. |
VULKOLLAN
® is the polyurethane elastomer with the highest performance. VULKOLLAN
® with the Shore hardness 93° Shore A is the well-proven material of choice for drive and load wheels from 40 to 920 mm (1.57 to 36.22 in) in diameter. It is the best solution for 90 % of all applications. This material is used for speeds up to 16 km/h (10 mph), in some applications up to 22 km/h (14 mph). VULKOLLAN
® with the hardness 95° Shore A is the first choice for even higher speeds (up to 25 km/h = 16 mph) and high demands on dynamic load capacity.
Heat build-up at high speeds can cause wheel failure:These days the top speed of reach trucks increases to 14 - 16 km/h (9 - 10 mph). The number of full-service or rental contracts is growing. Low level order pickers even reach speeds of 22 km/h (14 mph). In materials handling, the development is the same: The maximum acceleration increases to 4 m/s² with a top speed of 28 km/h (17 mph) - with 24 h continuous operation/365 days a year and 99 % availability.
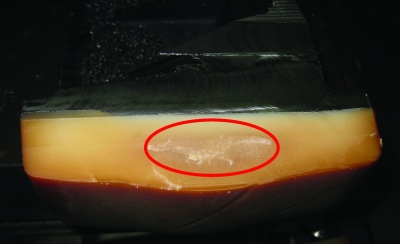 VULKOLLAN® wheel cross section: Because of flexing and the poor heat conductivity of VULKOLLAN®, heat builds up within the wheel material. The material liquefies and then crystallises again. |
In the above applications,
flexing combined with the
poor thermal conductivity of VULKOLLAN® causes
heat build up within the wheel material, especially over long transport distances. Typical damage symptoms are axial displacements of the cylindrical wheel tread, while the wheels show no external damage. The material liquefies and then crystallises again. The consequence: The wheel must be replaced.
Our solution: HSHL® (
HighSpeedHighLoad®) wheels:It is our declared objective to continue using the wheel tread material VULKOLLAN
® with all its positive characteristics as a standard material. Inevitably, this requires the
adjustment of the total system of wheel tread and wheel rim, tailored to meet customer requirements. The solution: Today we use the
HSHL® geometry (
High
Speed
High
Load
®).
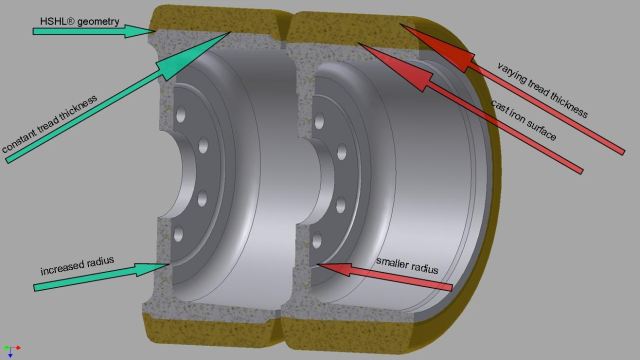 Comparison wheel with HSHL® geometry (left) and conventional wheel (right) - Click to enlarge |
|
On conventional VULKOLLAN
® wheels, tread thickness varies because of the draft angles of the cast iron wheel centres and core displacement. The cast iron surface is not machined.
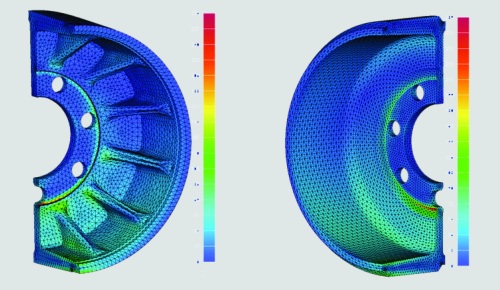 FEM analysis of wheel centre geometries - conventional version (left), HSHL® version (right) |
With the RAEDER-VOGEL
® HSHL
® contour,
uniform tread thickness is achieved through complete machining of the wheel centre. In the thermally critical area tread thickness is reduced. At the flanks, in the areas with the highest load and shear stress, adhesion is improved. Higher material thickness helps to avoid spontaneous tread separation. Together with the transmission manufacturers, we also
redesign the wheel centres for greater strength. Mechanical machining and the contact surface are optimised.
Already at the first design stage, the parameters wheel tread thickness and wheel centre geometry are validated by
FEM analysis. The new designs are also tested on the RAEDER-VOGEL
® wheel and castor test rig.
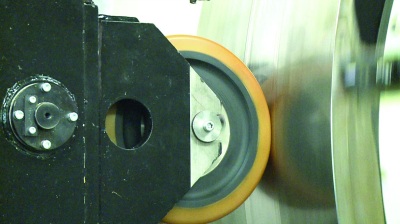 Destructive testing of a wheel on the RAEDER-VOGEL® drum test rig |
The reduction of the wheel tread thickness does not increase
surface pressure. Calculations as well as tests on our wheel test rig have proven that - for large radii - even at maximal load the surface pressure increases by max. 10 % and is far below 700 N/cm². Thus the wheels can be used on all standard industrial floors.
Damping is hardly affected either - the indentation of the wheel is reduced by a max. 0.1 mm/0.004 in.
Destructive testing of HSHL
® drive wheels for walkie trucks and order pickers on the drum test rig has shown that the
service life of the wheels increases by 29 %.
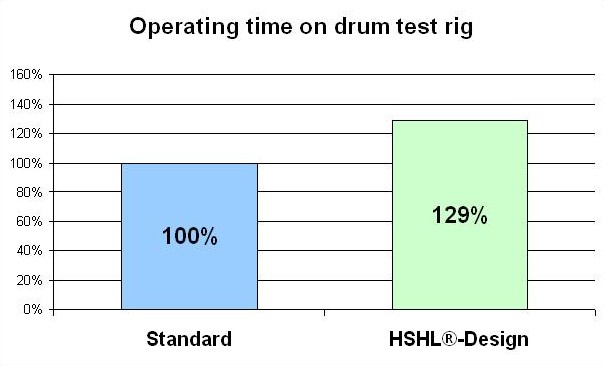 Comparison of operating times until complete destruction of standard and HSHL® wheels |
|
By consistent implementation of the above measures, RAEDER-VOGEL
® reduces the cost per unit by saving casting material as well as VULKOLLAN
®. At the same time, the performance characteristics of the wheels are improved because of lower heat build-up. The employment of resources is reduced, and the wheel life cycle is extended.
For more detailed information please contact Mr Bernd Dolk, Sales Director (
bernd.dolk@raedervogel.de).
For more product and company information, please visit our
shopfront or
www.raedervogel.de.
Click here to view the
RAEDER-VOGEL® ShopfrontVULKOLLAN® - registered trademark of Bayer AG, Leverkusen
HSHL®, HighSpeedHighLoad®, RAEDER-VOGEL® - registered trademarks of RAEDER-VOGEL®, Hamburg
Illustrations, Photos: © RAEDER-VOGEL®