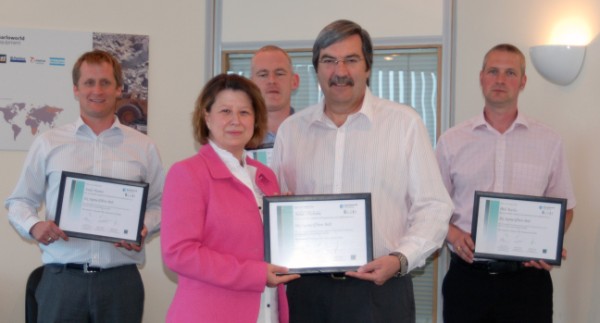 Barloworld Handling employees with their Six Sigma certificates. |
Barloworld Handling has used Six Sigma tools to achieve customer satisfaction and cut costs.
"One of the main areas of focus for our Six Sigma projects is the improvement of internal processes to achieve customer satisfaction," says Phil Marles, Barloworld's field service manager. "We also have a number of projects aimed at improving equipment reliability in the field."
Six Sigma methodology, a set of tools and techniques to improve the consistency and quality of process outputs, was first introduced in Barloworld in April 2008. Initially, six employees were trained to "Green Belt" standard by UK-based Paloma Consulting, and completed a comprehensive training program and several "improvement projects".
While Barloworld did not disclose details of the projects, seven of them were completed by the first group of Green Belts, "all with direct financial benefit and improved efficiency" for the company.
Barloworld says the projects resulted in fewer breakdowns, faster engineer response times, less waste and the improvement of new truck handovers.
"One key positive is that we have used the Six Sigma process to strengthen our working relationship with Hyster, helping improve the reliability of trucks in the field, and introduced improvements in manufacturing and quality testing," Marles says.
All Six Sigma projects are monitored for a minimum of 12 months after completion to ensure that improvements are maintained. At the end of July 2009, 10 more Barloworld employees achieved Green Belt status. According to Barloworld, future Six Sigma projects include partnering with key suppliers to improve its overall service offering.
Barloworld has been Hyster's exclusive UK distributor since 1956. It maintains over 30,000 forklifts a year with about 1,000 staff members and 18 customer support centres in the UK.