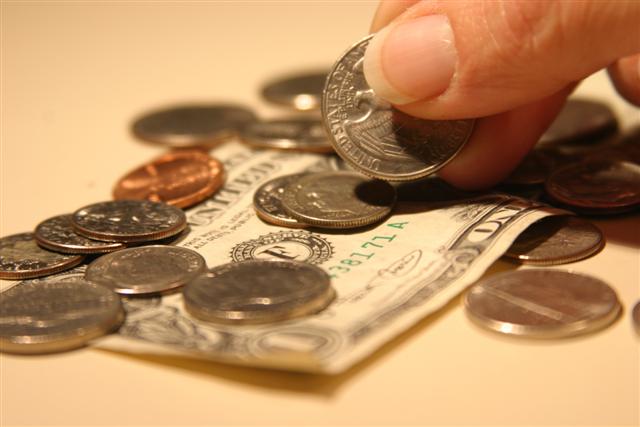 For every dollar invested in safety training, an average return of three to five dollars may be realised in return. PHOTO: SHUTTERSTOCK |
Rob Vetter is technical director and managing partner with the Ives Training Group, in Blaine, WA, USA, a leader in North American mobile equipment training systems since 1981.
There is no doubt that the economic seas are rough at the moment. Companies that have managed to endure the turbulence this far are battening down the proverbial hatches and trimming fat wherever they can. The economic developments over the next several months will influence many corporate decisionmakers as to where their dollars are spent.
Unfortunately, the costs associated with safety training are often deemed a non-essential expense and funding the same is often decreased or eliminated. This type of decision can yield tragic results from both personal and economic perspectives. People get injured and killed, equipment and product get banged up and all kinds of costs mount up. Ultimately, the costs associated with not training often exceed the amount "saved" by a very wide margin, and margins are what it is all about, especially profit margins.
Current statistical data supports the positive financial returns possible on every dollar invested into a well constructed, delivered and maintained safety training program. Most of these data point to one inescapable fact: TRAINING PAYS! Consider the following information...
Return on Investment (ROI)Many studies show that for every dollar invested in safety training, an average return of three to five dollars may be realised in return. In today's economic climate, scratch that, in any economic climate, that kind of ROI is a virtual windfall.
Show Me the Money!The financial returns that come from avoiding the huge costs associated with workplace safety incidents typically result in lowered net operating costs. In other words, if you are having workplace incidents, your operating costs are higher. Well directed safety training will not generate income but will help your company keep more of the money it does generate, and that kind of money is the best kind of all; it's called profit. Following are just a few examples of where additional costs could be avoided through proper safety training:
* Personnel Injuries - Even seemingly minor incidents can have significant financial implications especially as they relate to insurance rates for workers' compensation premiums as well as buildings, structures and equipment.
* Equipment Damage - Poorly trained and/or untrained operators using your equipment are more likely to damage it. This will cause maintenance costs to rise and repair costs to potentially skyrocket.
* Product Damage -Untrained operators will likely spill and/or stab loads, bang into things and generally handle your product roughly, causing damage to it, and your pocketbook.
* Regulatory Assessments - When injuries occur, claims and reports are filed to various agencies like regulatory authorities and, of course, insurance companies. The frequency of these occurrences will usually raise the profile of your company with these agencies and increase the likelihood of inspection. Such inspections often yield monetary assessments that in some cases can be very costly.
* Litigation - If it should get to the point where lawyers are involved, the associated costs can increase exponentially. Involvement with legal entities may also bring negative attention to your company which could have an equally negative effect on sales.
* Credibility - If your company subscribes to international standards (like ISO for example), a well managed and comprehensive safety program is listed within the compliance criteria of such standards. Insufficient safety training can result in certification of compliance with a given standard to be denied for applicants and possibly revoked for existing members. Either way, your sales will suffer.
* Employee Morale - If the management of a given company puts more effort into talking about safety training than it does into actually developing, delivering and maintaining it with integrity and support, the transparency of the situation becomes apparent to the employees very quickly and soon, they will put in as little effort as the management. Obviously, this type of situation fosters ill-will and even contempt between management and laboru with the worst result being injury or even death.
To put all of this into perspective for the purpose of making the connection between safety and profits, consider the following statistics:
* 70% of all compensable injury claims are directly or indirectly related to improper training, or the lack of any training at all.
* 95% of business executives report that workplace safety positively influences the company's financial performance.
* 61% of these executives state that their companies receive a return of $3 or more for every $1 invested in improving workplace safety.
* 90% report that they see a relationship between the direct and indirect costs of employee injuries.
* 40% define the direct/indirect cost ratio as being $1:$3 to $5.
* By combining direct and indirect costs, employers are paying between $155 to $232 BILLION annually!
Many companies continue along under the assumption that as long as costs do not spike year over year, everything is normal. Those same companies are usually appalled to learn the significant amount of money thrown away on the costs associated with little or no equipment safety training. They learn that in most cases, these costs are anything but normal.