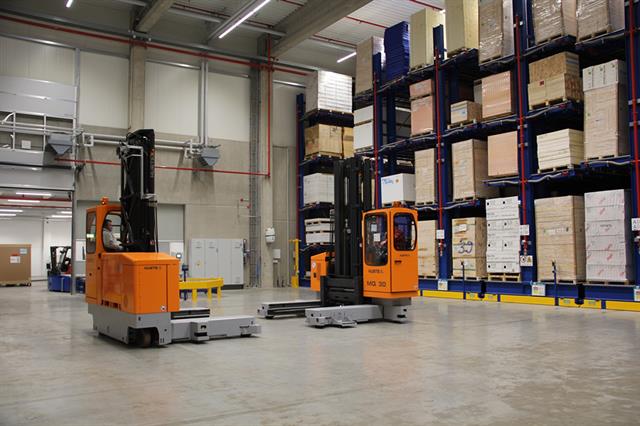 Two Hubtex MQ 30 electric multidirectional sideloaders perform pallet handling duties in Gaugler & Lutz' new logistics centre in Aalen-Ebnat. |
Effective materials handling and warehouse management is crucial to the success of a company, which is why Gaugler & Lutz oHG is banking on an intelligent storage system at its new logistics centre in Aalen-Ebnat (Nord) in Germany.The leading supplier of core materials and products for lightweight manufacturing has installed a 12-metre-high cantilever racking system spanning 2,200 square metres, creating enough storage space for roughly 2,500 pallets. The pallets are transported around the warehouse by two MQ 30 electric multidirectional sideloaders supplied by
Hubtex Maschinenbau GmbH & Co. KG. The sideloaders transport goods across the new mobile racking facility with the aid an inductive guidance system. The forklifts precisely place the pallets in the designated location using the semi-automated positioning system, while making ideal use of the storage space available. As such, Gaugler & Lutz is able to benefit from maximum storage capacities thanks to optimized logistics processes.
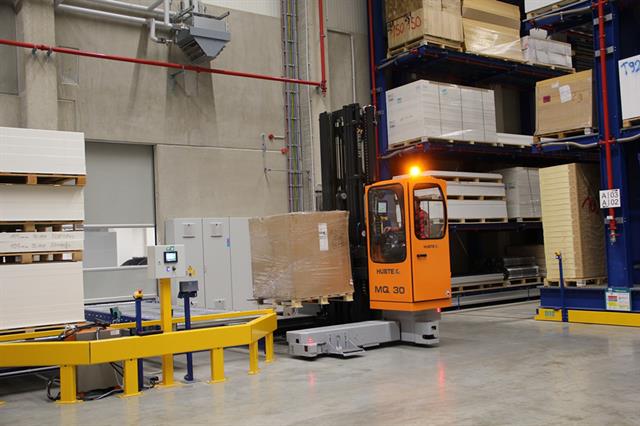 Hubtex convinced Gaugler & Lutz to put its faith in the company by presenting a tailored interface concept facilitating the ideal incorporation of vehicle and handling technology in the complex facility. |
Gaugler & Lutz oHG specialises in lightweight and sandwich-structure construction, along with the production and sale of sport, rehabilitation and leisure products. Based in Aalen-Ebnat, the family-run company supplies construction components for wind turbines, road and rail transport, and shipbuilding. At its industrial joinery facility in Aalen-Ebnat, Gaugler & Lutz processes balsa wood and foam materials, primarily of the rigid variety. These materials are used, for example, to strengthen wind turbine rotor blades. The processed materials had previously been stored in three warehouses in Ebnat-Sud. Due to the growing demand for lightweight materials, the company decided to build a cutting-edge facility with areas dedicated to production, logistics and administration. In order to completely replace the existing warehouses, the company needed a solution that made optimal use of the available space, with the objective of storing a maximum number of goods in the smallest space possible. Gaugler & Lutz therefore built a cantilever mobile racking system spanning 2,200 square meters, and thus created continuous racking for storing pallets.
Optimising space for pallet storage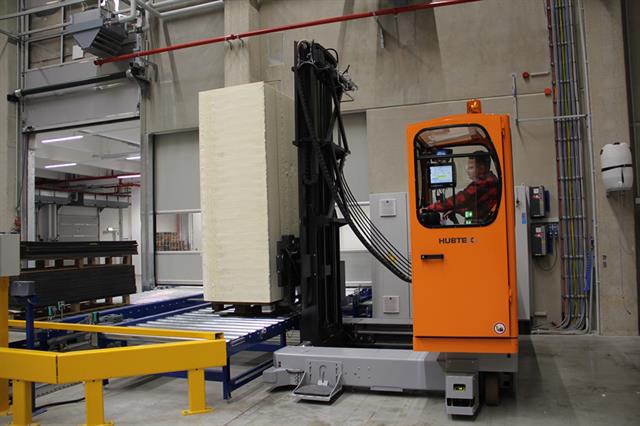 After being measured, the goods are transported into the warehouse on a conveyor belt, before being picked up by the MQ 30s. |
"We store and remove up to 120 pallets of raw materials on a daily basis," explains Dr. Rudiger Wittenbeck, project manager for process optimisation at Gaugler & Lutz. The various material formats and varying pallet sizes made it difficult to precisely store materials while making optimum use of the available space. Before the new logistics centre was built, goods were stored in standard shelving units or simply stacked on top of each other. Frontloaders transported the pallets to their destinations. "We were therefore unable to make optimum use of our storage space. Due to the rising demand for our products, we always needed more room," explains Vanessa Iliadis, who is responsible for logistics processing at Gaugler & Lutz. "After implementing our semi-automated warehouse logistics system at the new site, transportation and storage are now much more effective." In search of a partner that could supply the right vehicle for transporting the pallets in the mobile racking system, the specialist in pre-assembled construction components turned to Hubtex. The manufacturer of special-purpose vehicles for transporting bulky goods convinced Gaugler & Lutz to put its faith in Hubtex by presenting a tailored interface concept that ideally incorporates vehicle and handling technology in the complex facility. Hubtex also ensured optimal alignment between vehicle and warehouse management system.
Optimised routes through inductive guidance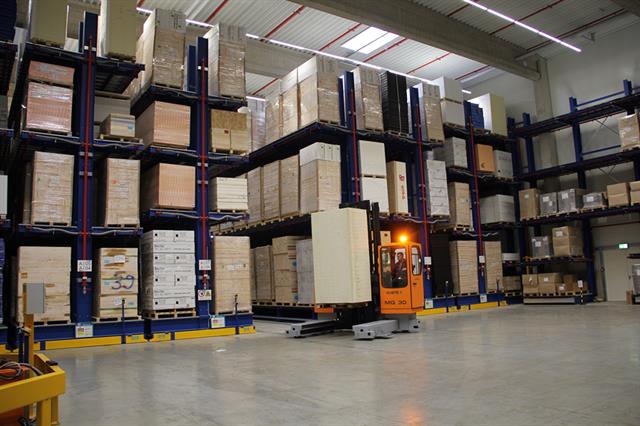 After the driver is given the goods' storage location via the process technology system, the designated racking system aisle automatically opens up. |
The racking system comprises 12 cantilever transfer trolleys, each with three to five continuous storage levels installed one above the other, along with two fixed rows of racking connected to the sides of the building. Since the pallets and the materials stored on them do not come in standard formats, the length, width and height of the goods are measured using a light-based device. The materials are then weighed. The dimensions and overall weight of each carrier determines where the goods are stored. After being measured, a roller conveyor system transports the pallets into the warehouse, where forklift driver Denis Velichko picks them up on the
Hubtex MQ 30 and scans the affixed bar code. "The ideal storage location is clearly determined by the dimensions and weight of the load and is communicated to our forklift driver through our process technology," explains Vanessa Iliadis. The designated aisle in the mobile racking system then opens up automatically. The driver lines up the vehicle in front of the aisle on the inductive wire and then sets the electric multidirectional sideloader in motion. The vehicle then positions itself at the right location in front of the racking. The racks must be positioned very precisely to enable clearance of just a few millimetres for the route guidance system and prevent contact with racks or goods.
Rack fire suppression system: Precision required to protect 4,000 sprinklers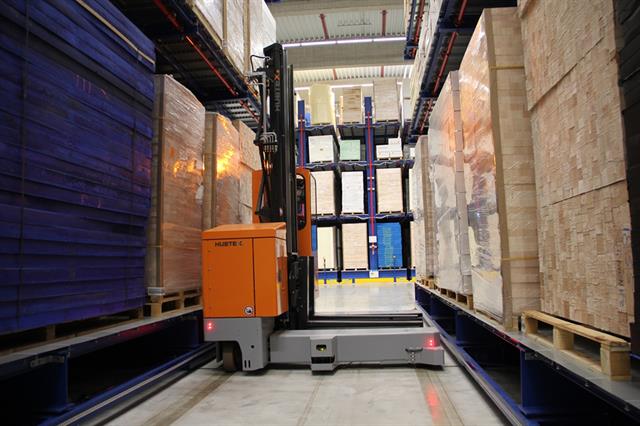 The driver lines up the vehicle in front of the aisle on the inductive wire and then sets the electric multidirectional sideloader in motion. The vehicle then positions itself at the right location in front of the racking. |
The lifting mast automatically stops once it has reached the required rack height. Freely configurable with 99 positions, lifting heights are preselected using the
Hubtex Load Manager. Once the driver has confirmed the end position, the pallet is then stored in the designated space with exceptional precision. However, the forks can be raised no more than just 10 cm below the sprinklers installed on the bottom of every rack. "Our rack fire suppression system comprises approximately 4,000 sprinklers," says Dr. Rudiger Wittenbeck. "Positioning the pallets precisely without damaging the sprinklers was an additional requirement for forklift operation." The automatic fire suppression system is required by law due to the unpacked foam plastics and helps prevent fire from developing. In addition, the multidirectional sideloaders feature personal protective systems. Laser scanners on the vehicle continuously monitor the aisles between the racks, detecting people or objects that are in dangerous proximity to the forklift. The system automatically reduces the vehicle's speed before bringing it to a halt.
Protecting goods through modern warehouse logistics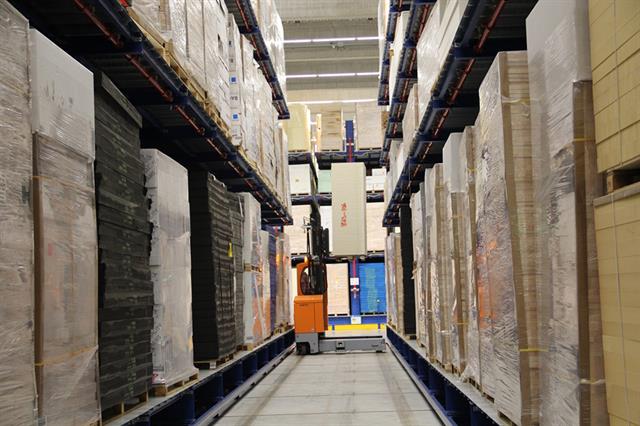 The lifting mast automatically stops once it has reached the required rack height. The process is controlled by the Hubtex Load Manager. |
The electric multidirectional sideloaders are guided along their paths, ensuring precise positioning of the vehicles. The inductive guidance system in the mobile racking facility guarantees maximum safety, more or less ensuring that racks and goods are never damaged. Optimised routes within the warehouses help save time when storing and retrieving goods. The use of Hubtex forklifts enables goods to be stored in the smallest possible amount of space, as the space between each row of racks can be kept to a minimum. "Thanks to our mobile racking system and the
MQ 30 multidirectional sideloaders, we have halved the amount of storage space required," stresses Dr. Wittenbeck. "Everybody who took part in this complex project was closely involved and worked together extremely well, which is why we were able to get the warehouse management system, vehicle, sensors and rack system in perfect sync with one another." The outcome: exact positioning of storage location coordinates and delicate handling to protect goods from damage. In addition, the
Hubtex Load Manager supports safe storage by preventing the forks from piercing the racking. Gaugler & Lutz will keep faith in the Fulda-based forklift manufacturer moving forward, with plans for the Hubtex electric multidirectional sideloaders to be equipped with vacuum suction equipment. Order-picking with the "Vacumat" will enable fragile materials to be protected from damage during handling, while also making life easier for employees when transporting bulky and heavy goods.
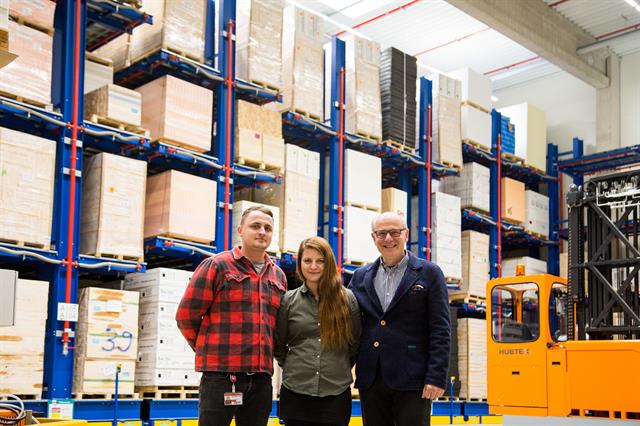 From left to right: Denis Velichko (logistics expert at Gaugler & Lutz), Vanessa Iliadis (responsible for logistics processing at Gaugler & Lutz) and Dr. Rüdiger Wittenbeck (project manager for process optimisation at Gaugler & Lutz) |
|
For more information, please contact:
HUBTEX Maschinenbau GmbH & Co. KG
Mr. Michael Robig
+496618382219
+49-151-14711052
Send an email
www.hubtex.com