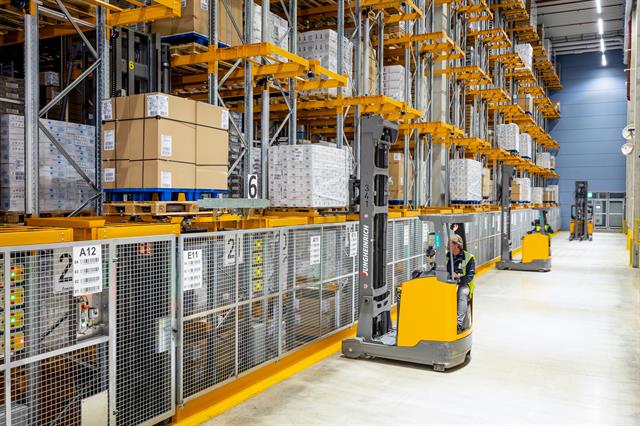 The Jungheinrich contour control system allows pallets to be efficiently moved to automated areas via reach trucks. |
Depro-Kautetzky from Wenkbach in central Hesse has ordered a comprehensive intralogistics package from Jungheinrich.
The order submitted by the company specialising in logistics services for the food industry includes the construction of a 12-aisle automated warehouse with 10,128 storage locations, as well as five ETX 515a automated guided vehicles (AGVs) from Jungheinrich.
The forklifts have telescopic forks, which can be stored at depositing heights of up to 12.8 m. Busbars are used to power the forklift trucks, which makes continuous operation possible.
A special feature of the Jungheinrich solution is the complete absence of conveyor technology for transferring the pallets to the automated area. The pallets are transferred manually by reach trucks. Contour control of the pallets takes place at a total of 36 cantilever transfer points. Sensors located above the transfer points check the load units from all sides for overhangs to ensure problem-free handling.
According to Wolfgang Schratz and Gert Kautetzky, joint managing directors of Depro-Kautetzky GbR: "The Jungheinrich contour control saves space, is particularly powerful and has high redundancy. Disruptions to operations are virtually eliminated. The system was recommended to us by ESM Ertl Systemlogistik GmbH from Minden, where it is used successfully. That is why we purposely planned from the inside out and developed the rest of the warehouse around the logistics solution."
Depro-Kautetzky relies on the Jungheinrich Warehouse Control System (WCS) for forklift and area access control. This frees the load carriers for storage in the narrow aisle warehouse and notifies the warehouse management system (WMS).
The first construction phase is planned for May 2019.